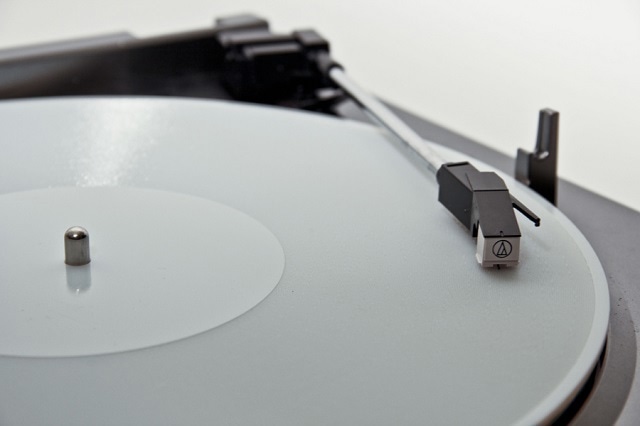
Image Credit: Amanda Ghassaei
With record sales at their highest level in the UK in the last 15 years, vinyl is currently experiencing a resurgence in popularity in an age in which many industry experts believed physical music to be superfluous to its digital cousin. Amanda Ghassaei from the tutorial website Instructables has used 3D printing techniques to create records which can be played on conventional turntables, paving the way for anyone to print their own music at home.
Good Vibrations
Record players work by placing a needle, (or ‘stylus’), on the surface of a record whilst the record is moved at a constant rotational speed - commonly 33⅓ or 45 RPM. The stylus moves along a spiral groove, which has been cut into the surface of the record, and vibrates when it hits tiny bumps in the groove. The vibrations of the stylus are processed into audio signals which are then converted by speakers into sound.
Sound It Out
The oldest commercial ancestor to the modern day vinyl is a lateral-cut disc record, known as the graphophone record. This record was first created and popularised by the German-born American inventor Emile Berliner in the 1880s. Over the last 130 years the audio quality of subsequent record designs have improved dramatically, yet the way in which they are manufactured has remained almost the same.
Traditionally, records have been manufactured by engraving grooves into a flat disc of Polyvinyl Chloride (PVC), commonly known as vinyl. This process works by firstly creating a ‘stamper’, which is a negative version of the record made out of metal. This stamper is then placed on top of a blank piece of vinyl in a hydraulic press. The impression of the master recording is pushed into the vinyl by the press before it is later stiffened by cold water into the finished record.
Print It Yourself
In 2012, Amanda Ghassaei, a developer at Instructables interested in exploring the limits of 3D printing technology, created an algorithm to convert digital audio files into three dimensional geometrical data. 3D printing is an ‘additive’ manufacturing process which allows objects to be built up a layer at a time from a variety of materials. By using her algorithm and a 3D printer, Amanda was able to produce prototype 33⅓ RPM 12” records which could be played on conventional turntables.
3d printed record
Amanda’s algorithm works by using raw audio data to set the depth of the groove of the record. The shape of the audio waveform is described by a set of numbers which are then used to determine the depth of the spiral groove. This allows the stylus to move vertically along the groove in the same path as the audio waveform in order to replicate the original audio signal.
Next, a 3D model is created from the groove depth and some general parameters of records such as their diameter, thickness and groove width. The 3D model consists of a set of ‘triangular faces’ arranged in 3D space to create a continuous mesh which describes the shape of the record and the spiral groove.
Finally, the 3D model is exported into STL format, which can be understood by all 3D printers. Amanda used an Objet Connex500 resin 3D printer, to a precision of 600dpi with 16 micron z-axis resolution, in order to create the records.
The grooves on Amanda’s records were ten times wider and ten times deeper than commercially available records, due to the current limitations on how intricate a 3D printed design can be. As a result, the audio quality of the printed records was fairly low, with a sampling rate of 11 kHz -a quarter of the quality of an mp3 audio file. However, the audio which is produced is still easy to recognise.
joy division - disorder
In late 2013, Bloc Party’s Kele Okereke and vocalist Bobbie Gordon used Amanda’s algorithm to produce a charity single called ‘Down Boy’, which is the world’s first commercially released 3D printed record.
Laser Cut Records
Amanda has followed up her work on 3D printed records by utilising a laser cutter to fabricate records by a ‘subtractive’ technique. Using an Epilog 120 Watt Legend EXT laser to a theoretical precision of 1200dpi, she was able to successfully ‘cut’ records out of various materials such as wood, acrylic and paper.
Although the finished laser cut records had sampling rates around 4.5 kHz, which is a lower quality than their 3D printed counterparts, the sound produced was still easily recognisable. The main difference between the laser cut records Amanda produced and the 3D printed records is the axis on which the grooves are cut.
Laser Cut Record
As the power of the laser cannot be controlled whilst it is cutting a vector path on the record, the surface of the material is cut laterally. This means that the stylus will only vibrate parallel to the platter of a turntable. The 3D printed records Amanda created are ‘cut’ vertically, resulting in the stylus vibrating perpendicular to the platter.
Revolutionising The Music Industry
Critics of these innovative techniques for producing records may dismiss their worth due to the current low quality of sound they output. However, it is worth remembering that the first songs which could be played online were comparable in terms of their sound quality, yet streaming services such as Spotify are now going from strength to strength.
With 3D printers forecast to rapidly come down in price in the coming years, the concept of anyone printing vinyl records could become a real possibility. This could allow artists to record, print and distribute physical copies of their own music without the need for a record company to be involved at any stage of the process, thus revolutionising the music industry.
References and Further Reading