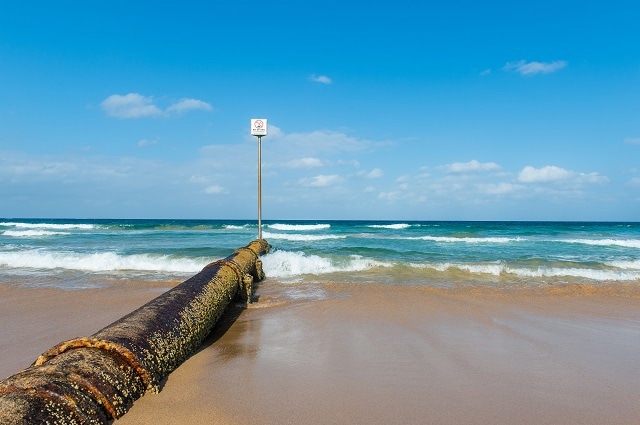
Storm-water Pipe Manly, Sydney, Australia
Image credit: Siwawut / Shutterstock.com
One of the first major subsea pipelines was built between Great Britain’s Isle of Wight and the coast of France during World War II and since then, their use has expanded exponentially.
Today, undersea pipes are mostly used to move oil and gas. Companies mine both from the ocean floor and the pipes are used to bring these fossil fuels ashore. After oil or gas has been refined, different pipelines are used to move oil, or the liquefied natural gas, to fuel tankers.
One of the most impressive examples of a subsea pipeline is the Langeled Pipeline, which connects the North Sea oil fields near Norway to processing plants in the United Kingdom, stretching nearly 750 miles between the two countries. The pipeline passes over rough underwater terrain and at its deepest point, it sits underneath nearly 3000 feet of water with a pressure of over 1500 pounds per square inch.
Installation of Subsea Pipes
The $3.3 billion Langeled Pipeline was laid with the help of two floating "pipe factories," or ships where the pipes were welded together before being placed on the bottom of the North Sea.
However, before that or any other undersea pipeline can be laid, the seabed must be carefully surveyed for any sunken ships, sensitive reefs or other objects which may be along the route. If an obstacle is along the route, it is either moved or bypassed. Surveyors also determine if any sections of pipe should be backfilled or buried.

Laying of Gaslines with a Specialized Vessel
Image credit: Martynova Anna / Shutterstock.com
Tow-in Installation
In this technique, sections of pipeline are attached to buoys and a tugboat drags the entire setup out to sea. Once the boat arrives at its destination, the buoys are either removed or flooded and the pipe is allowed to sink to the seabed.
This technique is called surface tow and there are three variations to it: mid-depth tow, off-bottom tow and bottom tow. Mid-depth tow involves using the speed of the tugboat to keep the dragging pipe sections from banging along the ocean floor.
Off-bottom tow uses chains to weigh the buoyed pipes down into the water. After the tugboat arrives at its destination, the buoys are removed. Bottom-tow involves dragging sections of pipe along the seafloor and is only used for shallow installations.
S-lay Installation
After the survey is complete, a small convoy of ships is sent out to lay pipe. Small barges supply floating “pipe factories” with sections of pipe while a lead ship watches the seabed. Pipes from the barges are unloaded into storage sites on the decks of the pipe factory ships. The factory ships typically have enough pipe segments for 12 hours of work.
Aboard the pipe factories, segments of pipe are welded together and each joint is then checked for defects using ultrasound. Next, all the joints receive an anticorrosion coating. A custom-built conveyor then moves the welded pipes toward a special boom called a ‘stinger’ that juts into the water at an angle. Pipes are then gradually lowered onto the seabed over the stinger.
J-Lay Installation
J-Lay installation is similar to S-Lay. However, instead of letting the pipes pass over the stinger, which makes an ‘S’-shape, J-Lay involves angling the pipe being welded off the deck of the factory ship and letting it ease into the water at a more vertical angle – forming a ‘J’-shape.
Lifting the pipe at an angle reduces the stress on the pipeline during the manufacturing process. This method also allows for work at depths deeper than can be achieved with the S-Lay process.
Attaching the Pipeline
The entire process of laying a subsea gas pipeline generally begins not on the shore, but in the sea. Gas pipelines incorporate quite a large number of sections all constructed at different times from several vessels, and then they are all linked to each other later. Gas pipelines must be able to endure pressures in various sections and because of this, pipes with several thicknesses are used.
Upon the completion of the initial subsea portion of the line, pipes are pulled up shore with a special winch placed on solid ground. The pipeline is then linked with its land-based section.
Pipe builders must also conduct hydro-testing of the pipeline. To do this, the pipeline is loaded with water under mandatory strain and left for a while to detect possible defects. The condition of gas pipelines are meticulously monitored after commissioning as well. Special electronics for in-pipe inspection are also used to monitor pipelines.
Corrosion
Marine-grade stainless steel, or 316 stainless steel, is one of the most popular alloys for subsea pipes and it has been known to corrode at the bottom of the ocean. There are two kinds of corrosion seen in subsea piping: pitting and crevice. Pitting is easily recognizable and can be caused by any number of factors. Crevice corrosion is much harder to identify however.
Pitting
Pitting corrosion begins when the chromium-rich film on 316 breaks down in a high-chloride environment. The greater the chloride quantity and the higher the temperature, the higher chance the film will break down.
Once the film is permeated, an electrochemical cell is set up. Iron goes into solution in the more anodic base of the pit, it then spreads in the direction of the top and oxidizes to produce iron oxide. The concentration of the iron-chloride solution rises as the pit deepens, which results in an accelerated rate of pitting, perforation of tubing walls and leakages. Pitting can go deep into the tubing walls, developing into a situation where tubing could be compromised.
Crevices
Crevices can be found between piping and pipe supports, between neighboring pipes and below deposits that may build up on pipe surfaces. Fairly tight crevices are the ones that pose the greatest danger to subsea pipe integrity. Standard corrosion of piping in a tight crevice leads to the oxygen concentration in the fluid that was in the crevice to decrease. A reduced oxygen concentration in crevice fluid increases the chance for breakdown of the surface film, and therefore the initiation of pitting.
Dealing with Corrosion
Some companies find that replacing 316 stainless steel tubes with a different stainless steel alloy reduces the amount of corrosion. Another possibility is to jacket the subsea piping with a material that resists corrosion, such as thermoplastic polyurethane.
For more from Brett, follow him on Twitter - @ParkstBrett
References
Disclaimer: The views expressed here are those of the author expressed in their private capacity and do not necessarily represent the views of AZoM.com Limited T/A AZoNetwork the owner and operator of this website. This disclaimer forms part of the Terms and conditions of use of this website.