Optical light microscopy is often used to study the quality of inductively hardened zones. In order to optically measure inductively hardened zones, four parameters are determined for each of the four curing zones of every component and then two parameters are added that identify the grinding position. In comparison with conventional light microscopy, the digital microscope Smartzoom 5 provides additional benefits for these recurring investigations.
Advantages of the ZEISS Smartzoom 5
The integration of the template function which allows same-object recognition while recording macros results in a considerable reduction in time. Also, the micrographs and analyses are consistent and are almost operator-independent.
Performing quality control of components involves time consuming, light microscopic routine examinations of the components for which staff with microscopic expertise are needed to obtain high-quality results.
However, while using the digital microscope Smartzoom 5, the workflow of these routine studies is considerably improved and employees who do not have microscopy expertise can also perform the analysis once a short introduction process has been completed.
Using the inductively hardened rotor shaft example, the article highlights the benefits of Smartzoom 5 for repeated light microscopic investigations. Besides generating macros or jobs, supervisors also define the required steps of analysis and the microscope settings, such as magnification, objective and mode of illumination.
Using stored jobs, it is possible for operators to control hardening zones in a specific and effective manner without the risk of neglecting one of the measured data pieces required to define these zones. The output data is repeatable and the quality is consistent.
Generating the Job
A job is created by the supervisor to control the inductively hardened rotor shaft zones, making the repeated investigation more time efficient. Also, the output data is not affected by the operator.
It is possible to measure the geometric parameters of two components embedded in one polished section, in one run. The first examination is performed by the supervisor and the job is recorded automatically in the background. An overview image of the sample map is created with the built-in overview camera (Figure 1a).
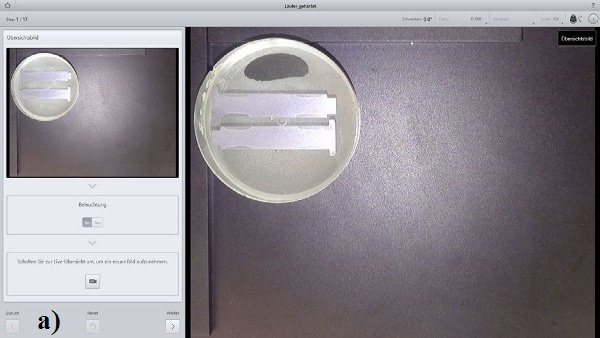
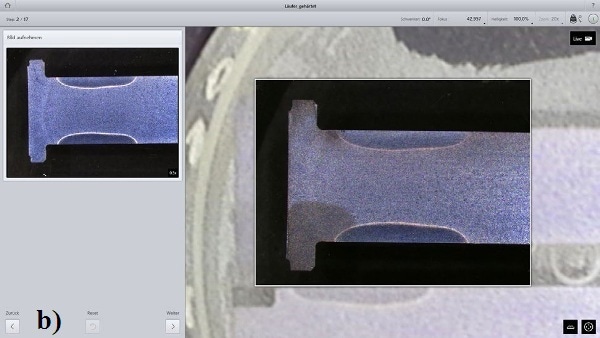
Figure 1. a) Positioning of the sample, generating the overview (map). b) Approaching the position, taking the micrograph followed by object recognition for facilitated measurement.
The first position to be studied is selected by clicking the desired position on the map, the microscope table moves towards that position (Figure 1b). The template is generated using the repetitive object tool by first marking the inductively hardened zone (Figure 2a). Using the measurement tool, distance lines for determining the hardening parameters are annotated (Figure 2b).
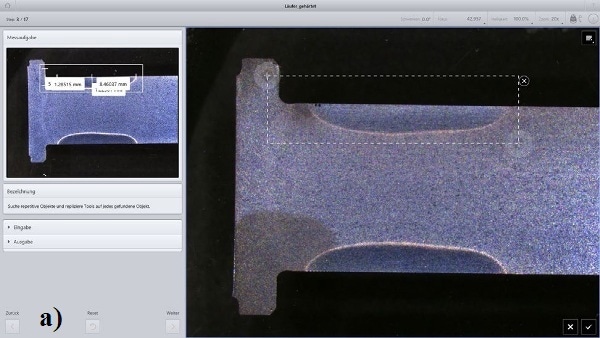
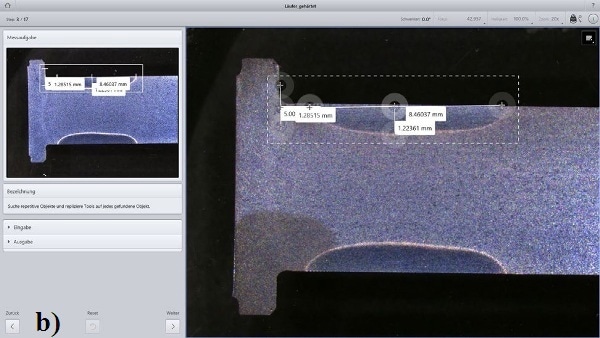
Figure 2. a) Definition of the repetitive object; b) Inserting the measurement tools, the distance lines have to be manually adapted.
Subsequent to manually approaching the next position with suitable magnification, similar hardening zones that should be measured are automatically recognized. It is important, however, to adjust the grabbing points of the distance lines to the measured region.
When the automatic object recognition fails, it is possible to manually select the object and also the starting points of the distance lines for measuring the hardening parameters (Figure 3b).
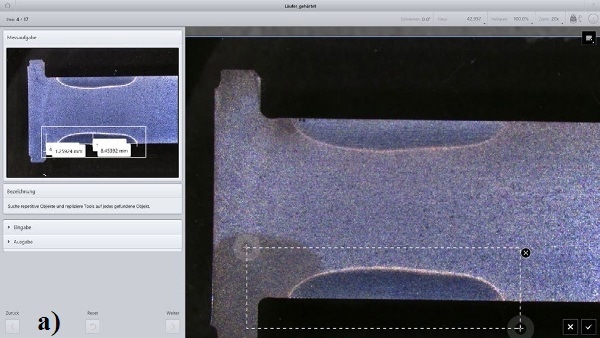
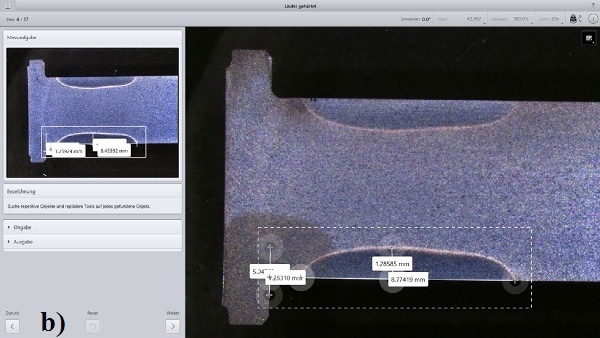
Figure 3. a) The Object position can be manually selected if object recognition fails; b) Adapting the starting points of the distance lines for measuring the hardening parameters.
The next step involves the measurement of the specification dimension of the grinding position (Figure 4a). The remaining three grinding positions are approached manually and object recognition takes place automatically (Figure 4b).
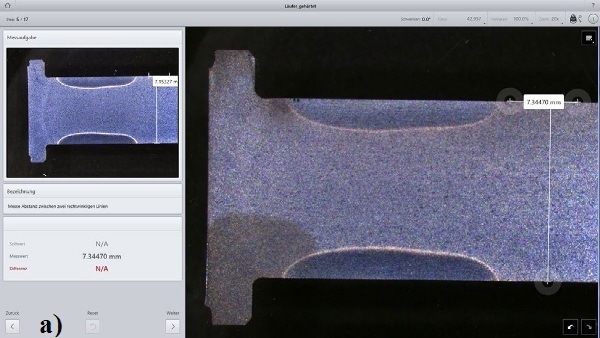
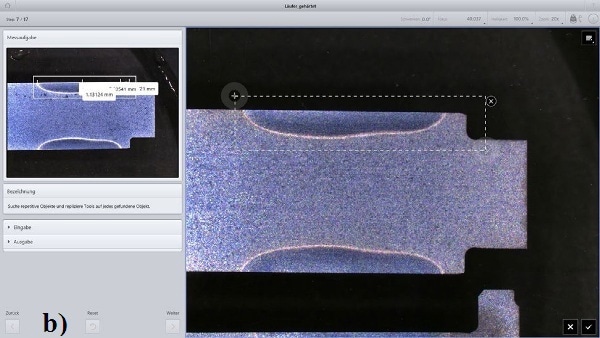
Figure 4. a) Measuring the specification dimension of the grinding position; b) Second position, successful object recognition.
Operating the Job
The measurement wizard guides the operator in a steps through the examination. The sample must first be arranged as shown in the map (Figure 1a). As a result, the microscope table approaches the positions that need to be checked. The operator is asked in each case to capture the micrograph with supervisor-defined settings (Figure 1b).
Object recognition is automatically carried out with annotated distance lines. The operator must control both, and in case of failures, correct them. Once the job is complete, the specific report, including the measurement results and the micrograph, is automatically generated and can be saved for future reference.
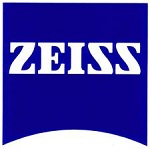
This information has been sourced, reviewed and adapted from materials provided by Carl Zeiss Microscopy GmbH.
For more information on this source, please visit Carl Zeiss Microscopy GmbH.