There is a general saying that oil and water don't mix. Unfortunately that doesn't apply to lubrication oils. In such oils, water can exist in different states, and if this is not checked, can cause considerable damage to important assets. This article investigates the difficulties caused by water in lubrication oils and also describes the techniques, which can be used by reliability professionals to effectively determine the presence of water in oil.
Background
In industrial oils, contamination of water can pose a number of problems in machinery parts. When water is present, the lubricant’s viscosity changes considerably and chemical changes also occur, all of which lead to depletion of additives and result in the formation of varnish, sludge, and acids. An integral part of any lubricant condition monitoring program is water testing. In industrial oils having robust water separation characteristics, standard methods are not suitable to determine water contamination. In an oil sample, water can jointly exist as three phases such as free globules, emulsion mix, and dissolved, all of which make it difficult to acquire a representative sample. In such types of oils, the additive formulations are designed in such a way that water is efficiently separated above the saturation limits of 50 to 250ppm water. The water above this saturation limit will form into distinct water droplets, which if left to sit, would ultimately separate from the oil, as shown in Figure 1. Emulsified water or free water should be rigorously regulated, but dissolved water does not pose a major issue in industrial applications.
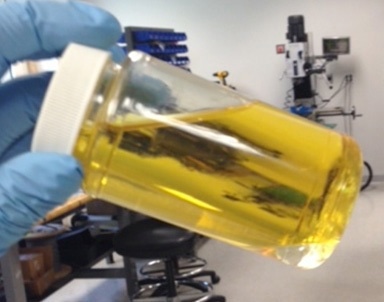
Figure 1. Sample of used Chevron GST 32, as received by the lab after shipment from a power generation plant.
What Techniques are Available?
Crackle Test
The presence of water in lubrication oils can be determined by using the easy and simple Crackle Test (Figure 2). A hot plate can be used to conduct this test, which is generally qualitative.
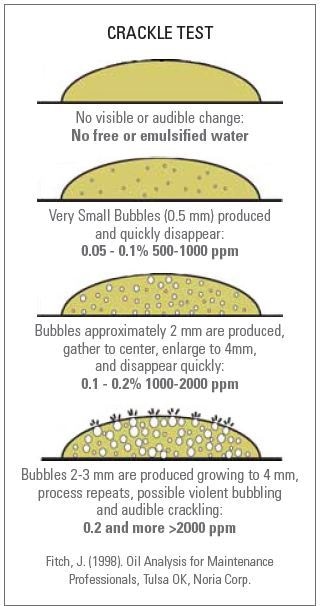
Figure 2. Crackle Test
While this test helps in determining the presence of water, it does not determine the volume of water present. Although some amount of semi- quantitative data about the quantity of water can be obtained through careful analysis of the oil on the hot plate, this mostly relies on the operator’s skill. A temperature-controlled hot plate is needed in the Crackle Test, and the temperature of this hot plate is usually set to about 160°C. The sample is dissolved by shaking vigorously, which produces a uniform water suspension in oil. As soon as the sample is prepared, the hot plate is added with an oil droplet. Crackling will not be seen if there is no trace of water in the oil. However, if liquid water is present in the oil, the heat will convert this water into vapor, producing bubbles that can be seen in the drop of oil.
The bubbles’ size approximately matches with the quantity of water present in the oil. In other words, if the bubbles are larger, the oil will be dissolved with higher amounts of water. By studying the size of the bubbles that are produced on the hot plate, quantitative conclusion can be made regarding the water concentration in the oil sample. Crackle Test is cost- effective, fast and easy, and can be performed on-site. However, it is not a quantitative method, presents safety concerns, and provides inconsistent results from operator to operator.
Calcium Hydride Test Kit
A calcium hydride test kit is another option that can be used to measure the concentrations of water in the field. In this technique, an oil of known volume is placed in a closed container that contains a calcium hydride of known amount. When this container is vigorously shaken, the water present in the oil reacts with the existing calcium hydride and creates hydrogen gas. The chemical reaction is given below:
CaH2 + 2 H2O → Ca(OH)2 + 2 H2
The solid calcium hydroxide [Ca(OH)2] precipitates out, and a manometer is used to determine the hydrogen gas (H2) and its pressure. This is a stoichiometric reaction, and hence a single mole of water in solution will create a single mole of H2. As a result, when the pressure of the gas ensuing from the reaction is measured, the amount of water present in the oil sample can be easily determined.
In order to perform the test, a syringe is used to take an oil sample. For any test, about 20 to 30ml of oil is required. The reaction vessel into which the oil was dispensed off features a screw cap to firmly close the reaction vessel. If the level of water is higher, the oil sample must be diluted using a diluent of known amount. The corresponding amount of diluent and oil will rely on the concentration of water present in the oil sample. At times, the test has to be repeated in order to establish the correct range of water contamination and also to choose the correct oil-to-diluent ratios. Until the vessel is closed, the calcium hydride is kept away from the diluent and oil so that all the H2 gas that is formed due to chemical reaction is confined to the sample cylinder. As soon as the sample cylinder is closed, the calcium hydride and oil are mixed and shaken vigorously to initiate the chemical reaction. After a while, the manometer fixed to the reaction vessel will read the internal pressure, and based on the relative mix of diluent and oil, the pressure reading is changed to a % water reading. In case the oil contains surplus amount of water, the vessel’s pressure can be combatively higher than the range read by the manometer. In such cases, the pressure must be released and the apparatus should be cleaned. The oil-to-diluent ratio is reduced to fall within the quantifiable range.
Calcium hydride test kits are integrated with a number of components such as manometer, pressure vessel, syringes, diluents, safety glasses, gloves, pre-measured calcium hydride packets, sealing rings, and sometimes are even integrated with a magnetic stirring plate. When these test kits are utilized properly, accuracy down to 50ppm emulsified or free water can be realized. The calcium hydride test kits are low-cost, relatively easy, portable, and offers quantitative results; however solvents and chemicals need to be used and there are also safety concerns due to the vessel under pressure. A number of runs may be needed based on the concentration of water.
Karl Fischer
Karl Fischer (KF) coulometric titration (ASTM D6304) is a well-established technique, which is used for detecting the presence of water in oil. It serves as a comparative technique for other analytical methods used for water analysis. By using KF for water determination, repeatable and precise results can be obtained when performed by a skilled operator. The water existing in any state, i.e., free, dissolved or dissolved, can be easily determined.
In applications and industries where water measurement is of major importance, KF titration provides a suitable option. These industries include food, pharmaceuticals and lubrication oils. In titration, a known concentration of solution is utilized to measure the unknown concentration of a solution. The titrant, i.e., the known solution is added through a burette to an analyte of known quantity, i.e. the unknown solution till the reaction is over. In KF titration, the volume of iodine consumed is equal to the volume of water contained in the oil sample. The oil’s water content can be precisely measured by quantifying the amount of iodine required to titrate the oil sample. Commercial Karl Fischer titrators for lab applications have been developed by Metrohm, Mettler Toledo and Sigma Aldrich (Figure 3). Due to the use of volatile chemicals and the sample preparation required, KF titration is often performed in labs and cannot be easily used at the site of the instrument being analyzed.

Figure 3. Metrohm KF titrator
Relative Humidity or Saturation Meters
Many industries use relative humidity (RH) sensors for humidity control (Figure 4). These industries include pharmaceuticals and food service. Three types of RH sensors are available, namely thermal conductivity, resistive and capacitive.
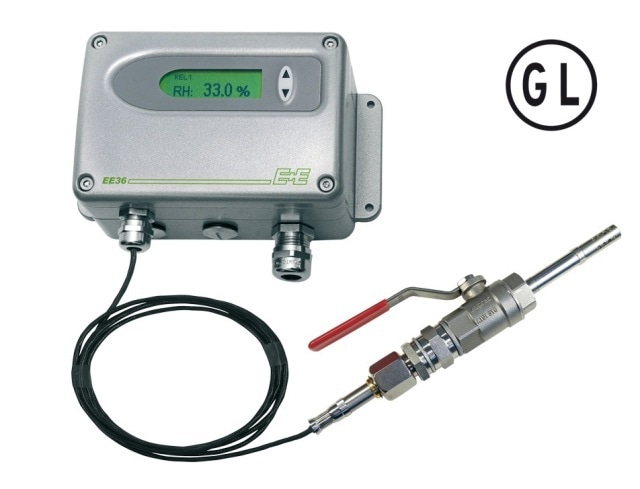
Figure 4. RH sensor from E+E Elektronik
Capacitive sensors are generally used for determining the oil’s relative humidity. The air’s relative humidity is a well-known concept, especially in warm climates during the summer months. The air’s ability to hold water vapor depends on temperature, and the same is true for oil. If the oil is warmer, its ability to hold water also increases. However, if the temperature of the oil is extremely high, for instance in internal combustion engines, the increased temperature will cause the water vapor to come out of the solution.
While humidity sensors are capable of determining the dissolved water in oil, they cannot determine the volume of emulsified or free oil, which limits their application to a large extent. However, by tracking the oil’s RH, critical data can be acquired. In capacitive RH sensors, a couple of conductive electrodes are included that have a non-conductive layer of polymer or metal oxide between them. The layer’s capacitance varies with respect to the water content and promotes a change in voltage between both conductive electrodes.
Defined by low temperature coefficient, capacitive RH sensor can operate at high temperatures of up to 200°C, have reasonable resistance to chemical vapors, and can fully recover from condensation. In the dielectric constant of the capacitive RH sensor, the incremental change is proportional to the environment’s relative humidity. These sensors exhibit a good response time and offer quick and precise readings. A standard ambiguity of these sensors is ±2% RH between 5% and 95% RH with two-point calibration. The distance of the sensing element limits the capacitive sensors, and this sensing element can be placed away from the signal conditioning circuitry, owing to the cable’s capacitive effect with regard to the slight capacitance changes in the sensor. Less than 10ft is deemed to be the practical limit.
Infrared
Infrared (IR) spectroscopy is a promising technique that is extensively used for determining water contamination. It allows an acceptable chemical-free measurement. Generally, spectroscopy refers to the study between the interaction of matter and radiated energy.

Figure 5. Schematic of typical spectrometer
In a spectrometer, a number of components are included such as a detector, a radiative source, and a PC or other converter of the detector signal to obtain useful data (Figure 5). In this technique, the sample that needs to be analyzed is positioned between the detector and the radiative source. In IR absorption spectroscopy, the incident light beam is allowed to travel via a sample and the detector is used to collect the transmitted light and the same is reported as a spectrum of the absorbed or transmitted light as a function of the wavelength λ of the incident beam. The IR light absorbed by pure water can be identified by a peak in the IR spectrum at about 3400cm-1. Upon dissolving water in oil, IR is absorbed by a water molecule, though the peak would have moved a bit because of the varied environment around the water molecule. As per the ASTM standard practice E2412, water is determined by matching the peak in the IR spectrum at about 3350cm-1 to the water concentration, as shown in Figure 6. This technique can be used in certain applications, such as in motor oils in which additives are used to dissolve water. IR analysis is a fast, simple and reliable technique. Even novice users can obtain the results easily.

Figure 6. Measurement for water in ASTM E2412.
When oil contains water in emulsified or free-state, the light travelling through the oil sample gets dispersed, which considerably impacts the measurement. In the case of industrial lubricants, large amounts of water are present either as free water or emulsion water because the oil contains demulsibility additives. The droplets of water suspended in oil do not absorb light, but instead scatters it. Hence, a water absorption peak at approximately 3400cm-1 cannot be associated with the water absorption peak that is well over the limit of saturation. Water stabilization is a successful technique that can be used to overcome the scattering of light. Under this technique, the sample is pretreated with a surfactant or other similar additives, through which water can be dissolved in the oil. This way, the standard water peak can be easily identified through IR spectroscopy. While a skilled operator will be able to perform the water stabilization technique, chemicals have to be accurately added into the oil sample before analysis. However, such chemicals cannot be accessed easily in the field. Hence, based on this reason, water stabilization technique does not prove suitable for end users in the field or for condition monitoring laboratories, where FTIR is used as a screening tool.
A homogenizer provides another option where water is mechanically integrated as distinct droplets of water suspended in the oil. When a CAT 120X homogenizer was used to homogenize samples and the same is kept at room temperature for 1min, it resulted in excellent correlation to KF coulometric titration. The extent of elastic light scattering induced by a water-in-oil mixture relies on the water concentration and is also affected by the way the water is dissolved in the oil, which is the size and number of distinct water droplets present in the oil, as shown in Figure 7.
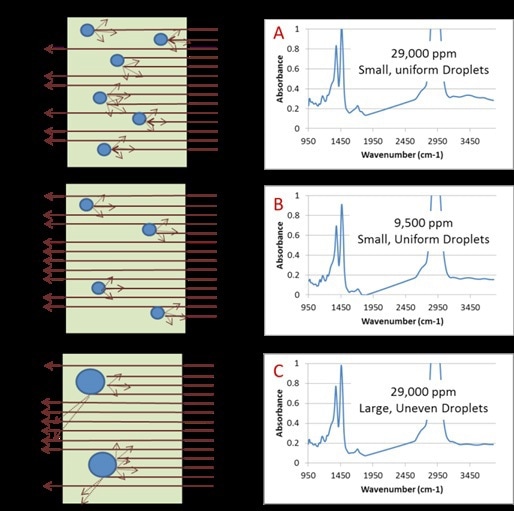
Figure 7. Graphical representation of light scattering in used turbine oil due to varied water droplets. Spectrum A is a used turbine oil with 29,000ppm water contamination immediately analyzed after homogenization. Spectrum B is a used turbine oil with 9,500ppm water contamination immediately analyzed after homogenization. Spectrum C is the same sample as in A (29,000ppm) but has been allowed to sit for 45 minutes after homogenization. The change in concentration and water droplet size is apparent in the degree of baseline lift.
The CAT 120X homogenizer helps in producing a repeatable and uniform distribution of water droplets in the oil. Following this, the extent of light scattering can be reliably determined using an IR spectrometer.
Rugged and portable, the FluidScan oil analyzer is used for determining the chemistry and the condition of oils. The homogenization method was used to prepare oil samples having different concentrations of water and then determined on the FluidScan oil analyzer. The results, thus obtained, were compared against those acquired through the KF coulometric titration (Figure 8). Excellent correlation was seen between the FluidScan readings and the titration technique.
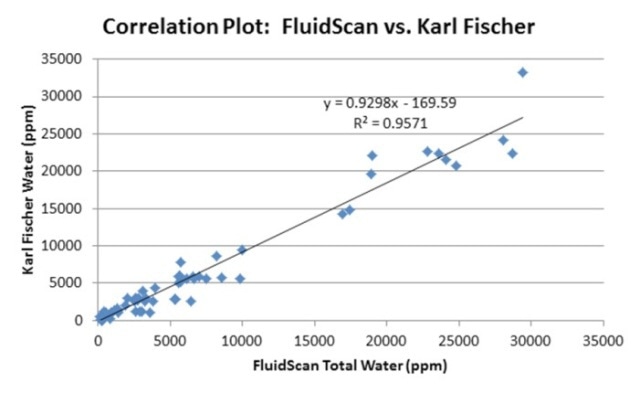
Figure 8. Correlation of FluidScan IR readings to Karl Fischer.
When analyzing water contamination in turbine oils, the FluidScan serves as a powerful and reliable technique and provides instant alerts when there is severe contamination of water. Sampling plays a key role in this variation, and the homogenizer forms a central component of the technique. When measuring water on the FluidScan oil analyzer, hand-shaking does not provide a suitable option for acquiring a uniform sample and consistent results. For best results, a homogenizer that is commercially available on the market can be used to realize fast and on-site analysis or sample preparation before analysis. Results correlating within 20% to KF can be obtained using best practice sampling methods.
Conclusion
Reliability professionals can use a number of techniques to determine the presence of water in lubrication oils. These techniques depend on a number of factors, such as personnel training, budget, the data precision needed, etc. In order to prevent equipment failure and the resultant downtime, instrument should be tracked continuously for water contamination.
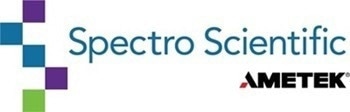
This information has been sourced, reviewed and adapted from materials provided by AMETEK Spectro Scientific.
For more information on this source, please visit AMETEK Spectro Scientific.