Sep 1 2016
Photonic integrated circuits (PICs) are considered a key enabling technology in a range of application fields, from telecommunications to biosensing and quantum optics.
Silicon photonics is a fast maturing field, enabled by manufacturing compatible with existing electronics paradigms and in line with the low-loss fiber spectral window in the wavelength range of 1.55 µm.
The strong confinement of light to submicron waveguide cross-sections can be achieved with this material platform because of the large difference in refractive index between silicon and its adjacent silica cladding layers.
This index difference forms the basis of the design of ultra-compact waveguide bends with radii of a few micrometers, enabling the dense integration of various functional components on chips with mm2 chip footprints.
Fiber Alignment to a Silicon PIC
These compact planar optical devices can be characterized in laboratories by coupling light obtained from off-chip sources to measurement equipment with the help of standard optical fiber technology.
As the cross-sectional area of the waveguide is very small, aligning both input and output fibers to the PIC with the help of a top, visible microscope image as a positional guide is a challenging task.
Here, the alignment of both input and output is performed using the power coupled from the output fiber. This process can be a time-intensive task considering the 3-axis translation stage control on both fibers and the inadequate knowledge about the loss of the on-chip PIC.
A SWIR camera can be used to speed up this alignment process. The Xenics XS-1.7-320 InGaAs camera is employed in the experiments.
It is possible to image the output facet of the PIC chip onto the camera when the light is coupled through an objective. The ability to image the full facet enables rapid assessment of the alignment of the input fiber to the waveguide.
Clear interference fringes can be observed when the fiber is above the chip level. A denser scattering pattern is visible when the fiber is injected into the substrate (Figures 1 to 3). The alignment of the fiber to the waveguide allows observing a clear output mode with high local intensity.
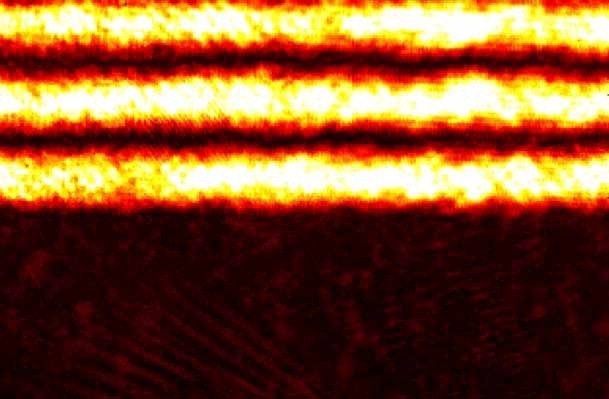
Figure 1. Fiber aligned above chip surface
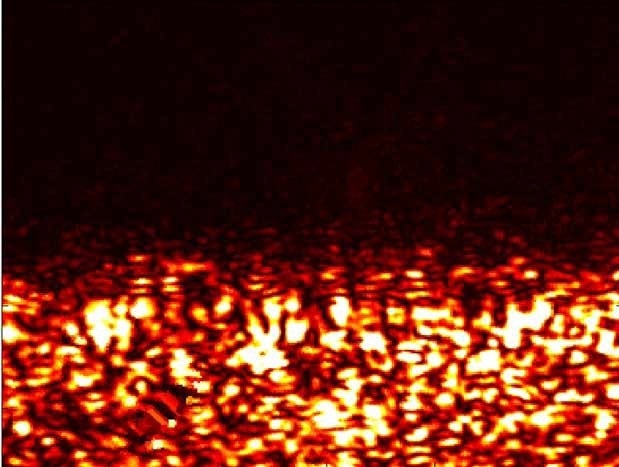
Figure 2. Fiber aligned with substrate
Since the light injected into the PIC is typically in the order of a few hundred microwatts, a highly sensitive camera is required to visualize the misaligned scattered field images with orders of magnitude lower power/unit area.
After aligning the input fiber, it is possible to use the second fiber to replace the output imaging lens, where only the output alignment stage has the degrees of freedom as the input is now clearly defined.
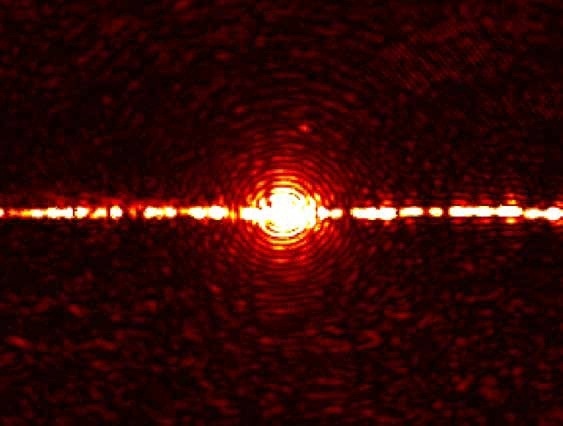
Figure 3. Fiber aligned with the guiding layer
Imaging of Vertically Emitted Beams
The PIC surface often needs to be visualized to determine local scatters within the waveguide, or deliberately emitted vertical beams, for example, on-chip generation of orbital angular momentum (OAM) carrying beams.
The low weight and volume of the Xenics XS camera makes it more suitable for this application (Table 1).
Table 1. Specifications of the Xenics XS cameras
Camera Specifications |
XS Base |
XS Analog |
XS Trigger |
Array type |
InGaAs PIN photodiode array with CMOS ROIC (CTIA topology) |
Resolution |
320 x 256 |
Pixel size |
30 µm x 30 µm |
Spectral band |
0.9 to 1.7 µm
Optional 0.4 to 1.7 µm (VisNIR) |
Frame rate (full frame) |
60 Hz |
60 Hz |
100 Hz |
Digital interface |
USB 2.0 |
Dimensions |
50 W x 50 H x 50 L mm3 |
Again, a highly sensitive SWIR camera is required to capture the images because the power levels of vertical scattering from PICs can reach extremely low values (<µW). Images captured for a range of vertically emitting silicon ring devices are shown in Figure 4.

Figure 4. Near-field images of silicon microring emitters with varying diameter, D. (False color)
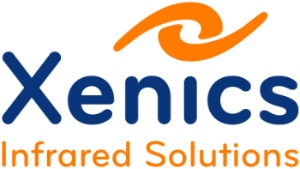
This information has been sourced, reviewed and adapted from materials provided by Xenics.
For more information on this source, please visit Xenics.