Particle size defines the performance of a wide range of different products, including metal powders, cement, cosmetics, inks, paints, foods and drinks. Therefore, measuring relevant particle size data is important in many industries, with laser diffraction being the preferred technique.
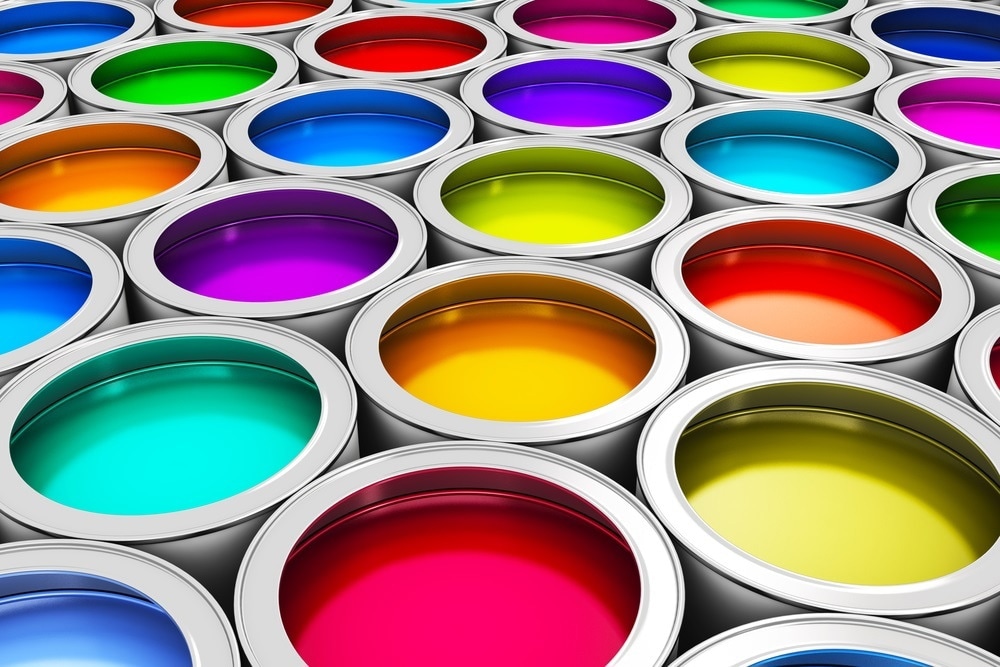
Image Credits: Scanrail1/shutterstock.com
Modern laser diffraction systems are highly automated, fast and suitable for measurement across a wide range of sizes, from 0.01 to 3500 µm. They have reduced particle sizing to a matter of sample loading and push button operation, provided that a suitable method is available.
This article offers some helpful tips on how to create a robust method that will efficiently provide reliable and reproducible data, whenever it is used. The ISO13320 (2009) [1] standard for laser diffraction puts considerable emphasis on the significance of method development, debatably ‘the last expert task’ related to laser diffraction, and there is plenty of helpful data available in the public domain. This article provides the required information on how to develop a new method, how to troubleshoot if things go wrong and on the tools that can be helpful.
Laser diffraction particle sizing must be a highly automated push button operation and must robustly provide highly reproducible data. If particle-size analyses are not meeting these required standards, then the method may be an issue. The guidance outlined in this article will help users to identify the cause of any problem and provide an appropriate remedy, but more importantly will help them develop a robust, trouble-free method from the start.
Read More
References
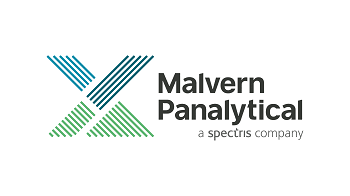
This information has been sourced, reviewed and adapted from materials provided by Malvern Panalytical.
For more information on this source, please visit Malvern Panalytical.