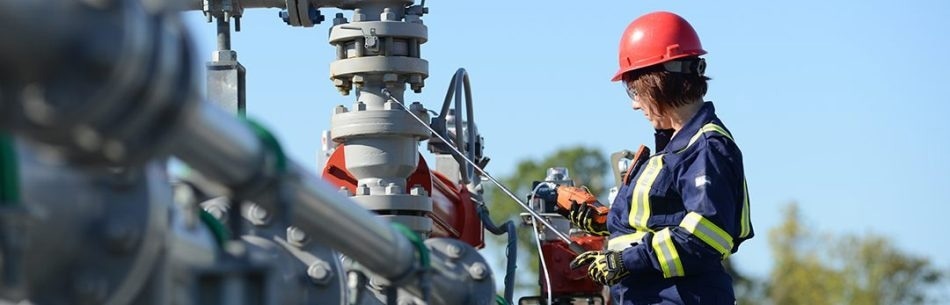
Electronic gas detectors have always been used with pumps ever since they came into industrial use. However, most workers still discuss when and how these pumps are necessary.
The common idea is that each gas monitor should have a pump, to optimize its accuracy, enhance response time and generally detect gas better. While this is not true, it is certainly established that the use of a pump will make it easier and safer to carry out some tasks.
Reasons to use a Pump with a Gas Detector
A pumped gas monitor enables air to be drawn from a location which is not known or could contain toxic or flammable gases into the user’s location to obtain results which can be studied in a safe area. Thus, the pump makes the operation safer. Again, after the sampling is complete, and it is proved that the air does not contain toxic or combustible gas, the user can safely enter the other location to work.
Another situation is when the vessel is 30 feet in length or more but not too tall, so that the working space is confined. Here a pump which has an extensible probe can be used to explore the space slowly while the probe tests the air in front, ensuring that it is safe to go further into the cavity.
On the other hand, for very tall narrow vessels which leave a space accessible only from above, a pump with long tubing will be ideal to check the completeness of emptying of the space of all hazardous gases before the worker enters.
In this way the use of a pumped gas monitor increases the safety and the convenience of the process of detection of toxic gases, while not affecting the range of gases detected or its effectiveness. This is because the detection of gases depends on the gas coming in contact with the sensors of the monitor.
Pumping does not increase the chances of this contact, by bringing more gas near the sensor, but allows remote testing of the air at a spot far away from the monitor. Thus, if two adjacent gas monitors are tested, with one having a pump and one without, but the pump is not attached to tubing, both will show the same readouts because the pump does not increase the speed of hazardous gas detection compared to the other unit.
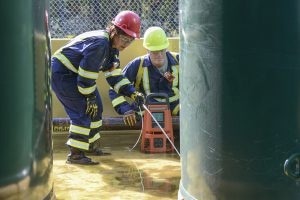
Pumped gas monitors help to keep you out of areas where potentially harmful gases may be lurking.
Reasons to not use a Pumped Monitor
Incorporating a pump on a monitor increases the size and bulk of the detector, without increasing its sensitivity of detection. This could be an issue since people typically wear the gas detector throughout working hours, making it a drag to don a larger and heavier piece of equipment for 12 hours or longer.
It would then be vital to have the smallest, lightest and most efficient detector possible, which also has a battery life to last through the whole shift. The pump also draws on the battery of the detector and thus reduces the overall run time. Thus, the pump need be employed only where its use would make a crucial difference.
Other Factors in Pump Usage
If it is determined that your gas detector requires a monitor with a pump, other components to optimize its performance and protect it from damage must be used. For instance, a probe is essential if a pumped monitor is being used to enter a cramped space, in the form of a polycarbonate probe which weighs little, or a stainless-steel probe which can be extended, or if required a high-temperature stable probe.
Tubing is necessary for vertical narrow cavities. In most cases the tubing is of urethane, which can handle most gases except for chlorine and chlorine dioxide, hydrogen chloride and volatile organic compounds (VOCs), all of which are absorbed by this material and thus are read at lower than actual levels. Teflon-lined tubing is thus the first choice when these gases are tested for.
Pumps with tubing must always be switched on for a period sufficient to travel through the full tubing, from one end to the other, and then to pass into the sensors by diffusion. This may be estimated as two seconds per foot of tubing, and two minutes for the contact with the sensor and stabilization. Thus, for a 30-foot length of tubing, readouts may be expected to take three minutes to appear for a gas sampled at the end of the tubing.
Again, if a pump is used, a dust filter is mandatory as well as a water stop at the end of the probe or tubing if used, to keep out dust and other particles which could damage the sensor, as well as preventing inadvertent drawing in of water into the pump motor in case the tubing end comes into contact with a liquid.
Pumped gas monitors reduce the likelihood of harm in a variety of applications, whether in a water treatment plant where they are used to confirm the absence of gases in a tank before it is subjected to maintenance, or in a refinery situation where it is required to look for leakage among valves and pipelines in inaccessible locations.
Monitors without a pump are better when personal gas detectors are in use and there is no need to sample gases from remote locations.
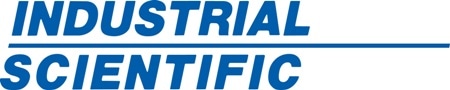
This information has been sourced, reviewed and adapted from materials provided by Industrial Scientific.
For more information on this source, please visit Industrial Scientific.