Oct 2 2002
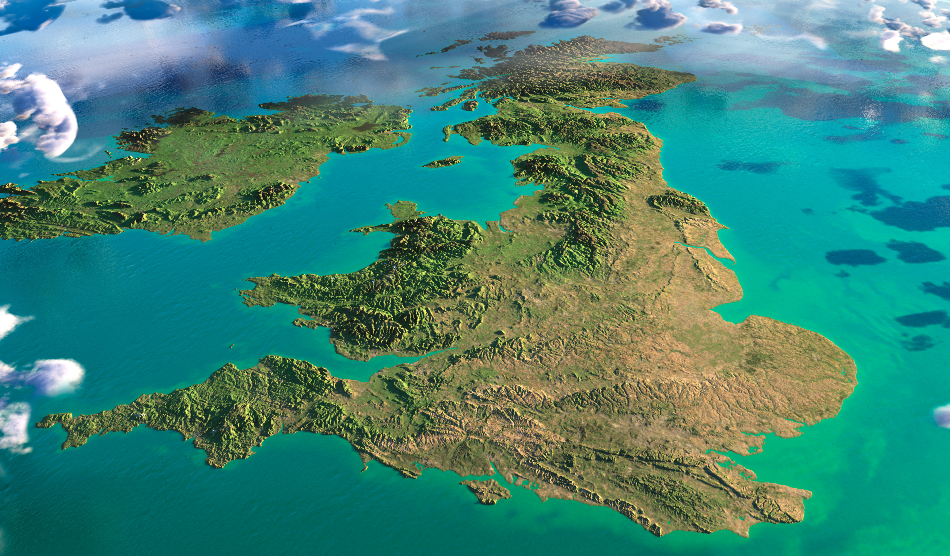
Anton Balazh / Shutterstock
Heat treatment engineers constantly complain that their customers look at heat treatment as an “add on”—an afterthought. This attitude is still prevalent although a century ago, it was the norm; heat treatment was still considered a “black art.” Methods were uncontrolled, unreliable, and inaccurate, so engineers continued to over-design by 100%, just to be sure.
Origins of Heat Treatment Companies
Manufacturers were happy to allow someone else to perform their “dirty” work. So, as early as the 1920s, professional heat treatment companies started to appear in cities like Birmingham.
Development of Heat Treatment Industries
Since a majority of these companies were small and “craft”-based rather than technologically-based, they could not perform research and development by themselves, which effectively slowed down development. World War II transformed all this, but again resources in the United Kingdom were meager, so most of the progress came from the United States. Ideas that actually originated from the United Kingdom were generally exploited in the United States before it was exported back to the former.
After the war, leading U.S. car manufacturers were setting up advanced, in-house heat treatment plants in the U.S. and in Germany, and this, compared to all other things, drove things forward, with the imposition of new standards in quality and efficiency.
The New Generation of Heat Treaters
But far from transforming the sub-contract scene, this held it back once again, since the resources to finance this new technology were not available. Only towards the end of the 1950s did things started to change, because the motor giants needed overload facilities—safety valves—and increasingly sought to outsource a number of components. So, it was no surprise that this produced a “new generation” of heat treaters.
The author’s own organization, Nemo Heat Treatment, was set up in 1959, which was later transformed into Bodycote PLC.
American Influences
Many of the plants that were set up were U.S.-built—or at least U.S.-designed, and most of the methods and standards applied were also those of the United States—a situation that stayed the same for the next two decades or so.
Geographical Influences in the Heat Treatment Industry
Unexpectedly, while new, advanced companies cropped up, and some of the more modern thinking “old guards” adopted the new ways, many of the smaller traditionalists continued to follow the former ways. There were numerous reasons for this; perhaps the geography of U.K. manufacturing was a huge influence.
Engineering—thus customers for heat treaters—can be located in all British towns. But mainstream manufacturing tended to focus on three core areas:
- Birmingham and the Midlands
- Lancashire/South Yorkshire conurbation
- Greater London
The Birmingham and Midlands Region
Metals engineering has revolved around Birmingham for over 200 years. The region is thus “dense” with customer potential, and small, low overhead, street corner job shop heat treaters flourished.
In the early 1960s, the place had over 40 such shops, with many of them catering to the tooling sector which, in turn, expanded around Birmingham’s famed “metal bashing” industry (stamping, pressing, etc.). To be reasonable, a number of these small shops were doing well and offered quality service, which possibly discouraged the formation of “new generation” facilities in the vicinity.
It is worth stating that the West Midlands did have several large heat treaters even before the war, because of the forgings and fasteners (nuts and bolts) industry, which also developed here. In this aspect, it was exclusive in the United Kingdom. Many of these large contract shops were the so-called “rough” heat treaters—very large scale hardening, tempering, and annealing, in open, non-protective furnaces. One or two big plants like this are still operating, but the market is weakening and is projected to decline continuously.
The Lancashire/Yorkshire Region
More than anything else, it was the decline of the textile industry which brought a change in the large-scale engineering manufacture in Yorkshire and Lancashire. The region not only produced wool and cotton but also built the machinery to do it. It thus had a wealth of skill and know-how which was in danger of being lost as the curtains closed on leading textile manufacturers—strangely enough, this too happened in the early 1960s.
These resources drew aerospace, tool and mold making, specialist components producers, and specialist machinery developers to the region, which, of course, consecutively produced plenty of demanding heat treatment.
It is perhaps no coincidence, therefore, that debatably the world’s most fruitful heat treatment group began near Manchester—an area that lacked multitudes of established, small job shops to be found in Birmingham. Heat treatment in Manchester remained under the control of a small group of significant, go-ahead companies.
Similar to the case of the West Midlands, this region did have one exception—Sheffield. Conventionally, the home of steelmaking and cutting tools, this area had some large “rough” heat treaters, as well as several small job shops, focused on HSS cutting tools. Some of these are still in existence, but most of their local market has vanished. Their specialist services have allowed them to draw in work from a large area to survive.
The London Region
Lastly, the South East region—perhaps a central engineering area, just because it is so big! It is not recognized for any specialist product but has plenty of small/medium engineering and tooling manufacturers. Consequently, just like the West Midlands, the South East region also has myriads of small, localized job shops. Partly due to its diversity, but probably because all motorways lead to London, only a few major new facilities emerged in this area.
Although, as already stated, General Engineering has spread across the United Kingdom, there is rarely sufficient heat treatment to draw major job shops to set up in other areas. In the last few years, comparatively cheap transport has changed the whole scene, so “area” has become a lot less important.
The Current Situation
These developments pointed towards the present situation. Although localization was no longer essential, as one heat treatment center can now cater to a very wide area, historic ties and practices still prevail. There are still about 15 small, local job shops in the West Midlands, a few have not changed much since the 1960s.
Others, however, have expanded, improved, or become specialists in one or more methods. Customer demand for ISO 9000 has had much impact on this, and several originally in this “local” category currently work plasma nitriding, pressure quench vacuum furnaces, etc., to a high standard.
Traditional Heat Treaters
Some of the older large scale “rough” heat treaters have endured, and most of those that have are now members of larger groups, offering just one part of a total service to the correspondingly small group of producers of fasteners and forgings, etc. that prevail.
The New Breed of Heat Treaters
With regard to the new breed of heat treaters, established in the 1950s and 1960s, most have either become major, wide-ranging contractors, delivering almost all known types of heat treatment, or they have become one-track specialists providing, for example, fluidized bed heat treatment or induction heat treatment.
Categories of Heat Treaters
The initial category has grown large—Bodycote, for instance, currently has plants in every region across the United Kingdom. No other group has expanded on such a scale, with the number two—TTI Group, formerly Senior Heat Treatment Group—being considerably smaller, with eight locations in the United Kingdom. The next tier, which includes the author’s organization, the Wallwork Group, is about half the size of TTI Group.
All these groups have developed, majorly by acquisition, although a few have opened some specialist new plants; for example, the author’s group has opened an advanced surface engineering center for ion implantation, PVD coating, etc. Bodycote has invested in parallel ventures and has also set up a few highly automated bulk heat treatment facilities. It has also opened contract facilities within leading customer companies, such as Rolls Royce plc.
Geographical Influences
As the geographical location is not important anymore, this has caused a few of these “major” heat treaters to set up their high-tech facilities in rural areas, clearly making recruitment a little stress-free. This was also because development grants are mostly available in such “underdeveloped” areas, and generally, transport is not very imperative at this end of the market.
The conventional centers still have the vast majority of significant customers, so a majority of the new, smaller specialist or single-track companies have established themselves in these areas. Not only is there a large customer base available, but such leading centers are also competitively connected to most of the United Kingdom via the motorway network at present.
Trends in Heat Treating
Processes
Largely, traditional methods— including atmosphere treatments established in the 1960s such as carbonitriding—still prevail. Sealed quenches are, perhaps, still the most prevalent type of plant, and at the smaller end, there are a number of salt baths that are still in operation. Evidently, the use of vacuum methods has grown quickly over recent years, with 10 bar pressure quenching and interrupted quenching now generally available.
Specialist methods such as fluidized beds have been slow to catch on, although this is perhaps changing in reaction to environmental pressure. Bodycote is currently running some of the major units on nitrocarburizing.
Customers
Hence, in many ways,—although there have been important improvements in a number of areas—the industry does not look very different from what it was in the 1970s. What is changing—quite radically—is the customer base.
U.K. manufacturing has plunged from 45% of GNP in the 1960s to lower than 20% at present. This fall may still continue, as e-commerce offers big companies an easy route to source parts from low-cost economies.
Perhaps the same woes are being voiced in Australia but according to the author, the United Kingdom is suffering unreasonably, partly because of not being fully inside the European Monetary System, and partly because of the conservative nature of the conventional companies.
The Industry
From this, one must deduce that capacity has not vanished, either by some companies moving into other processes or by plants being closed. Both are beginning to take place. There is, of course, a third option—only open to the really prosperous—to shift into other geographical areas. Bodycote and, to some extent, TTI are already following this with some success.
At the other end of the spectrum, some of the very small job shops may survive well, since there will always be a small hiring market, and some shops actually have very low overheads.
Based on this, the author concludes that the most susceptible sector is the small-to-medium companies that have invested, but which suffer from a lack of resources to implement more radical changes. These are the ones that are already being overtaken by the big players or are possibly going to close down. For example, several such companies are now going for up for sale.
Summary of the British Heat Treating Situation
Before closing with a quick glimpse of mainland Europe, it might be useful, to sum up, the current scenario as a set of conclusions:
- Heat treatment is contracting with it—companies are being acquired, closed, or put up for sale.
- U.K. manufacturing is under huge pressure and is contracting.
- The leading players are acquisitive, are diversifying, and are expanding beyond the United Kingdom.
- The most susceptible sector contains well established, but under-resourced small-to-medium companies.
- Smaller players with resources are inclined to move into specialist or even new technologies.
The author has added that U.K. innovation has not declined and therefore go-ahead smaller players will survive. However, there is still a noticeable reluctance to invest in these novel ideas, so this may not offer an overall solution.
The European Market for Heat Treaters
Lastly, coming back to mainland Europe, the author believes that the situation is slightly easier, except maybe in Germany. Countries such as Spain, Italy, and currently Poland, have become leading component suppliers to some of the big players, but in the author’s opinion, have a minimal number of heat treaters.
Italy has gained a good reputation for treating large dies in a vacuum. France may be the most willing to try out new technology and has a broad sub-contract base. Many of these plants have top class plasma facilities, and many are using vacuum carburizing on a substantial scale.
Germany—more or less as conservative as the United Kingdom—also has issues, which stem mostly from re-unification. With regard to technology, it lags behind France but still has a few job shops to compete against “downtown” Birmingham. On the other hand, it has some big automated facilities and some well-resourced vacuum job shops.
It might sound traditional, but having been educated along the U.S. lines, Germany is also interested in investing in the new, well-established concepts. Hence, the country is also a “force to be reckoned with.”