In the field of manufacturing and industry, having a reliable energy source to generate power and perform functions can make or break a business. Therefore, compressor air systems are a crucial part of and mandatory for both small-scale and large-scale businesses. If they are not working properly, an estimated 30 % to 50 % of the energy used in a compressed air system could be wasted during operation, which proves just how important these are.
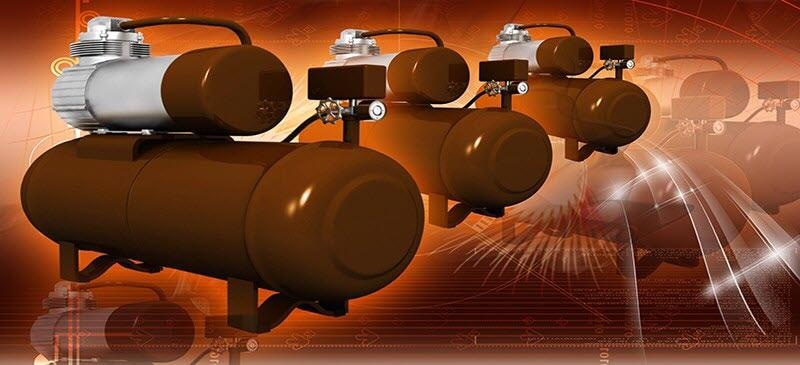
There are several challenges that businesses face – they not only have to self-regulate their production, but also consider outside regulations, such as the rigid standards imposed by government bodies and industry groups that require the air compressor systems of today to meet top energy and performance targets. Consequently, manufacturers are driven to gain a competitive edge through cost-effectiveness, safety and reliability, design efficiency, and storage.
Those strategic goals can be achieved by using precise fit seals or polymer components. Due to the working conditions, compressors cause some of the toughest challenges in the industry. Compressors are used in industrial manufacturing, oil refineries, petrochemical processing, chemical processing, food and beverage, textile, mining, environmental, and life sciences markets.
The abovementioned applications involve toxic, combustible, or caustic environments as well as high pressure; therefore, they need to have reliable parts, such as seals or bearings to help with leakage and other issues. There are different types of compressors - vane, scroll, centrifugal, reciprocating, and screw.
Rotary-screw compressors leverage pneumatics and rotors to compress gas with the help of screw actions. They often take the place of piston compressors, particularly when high volumes of compressed air pressure is required, for instance in industrial applications. These are also less noisy, less expensive and easier to operate and maintain.
Rotary-screw compressors have improved rotor profiles with reduced internal leakage, and that allows them to offer better efficiency and reliability. They can also offer economies of scale over other options, particularly as horsepower (HP) levels increase.
While a 250 HP compound compressor is a large piece of equipment often needing its own foundation, a 250 HP rotary-screw compressor is usually considered “compact” and can be moved with a forklift and rest on the shop floor. Rotary-screw air compressors can handle low and high-pressure appliances ranging between 7 to over 100 bar, respectively.
The majority of the global market is held by these compressors. In 2017 the worth of the market was valued at $ 36.6 billion and it is expected for it to reach $ 45.7 billion by the year 2023. Rotary-screw compressors occupy the majority of the market share as of 2017, and according to Prescient & Strategic (P&S) Intelligence, they would continue to increase their share by 2023.
Markets and Markets also agrees that the rotary-screw segment of the compressor rental market is expected to grow to the highest CAGR between 2016 to 2026. For the most part, the demand for screw compressors, and therefore, the expected increase, are driven by the industrialization in the emerging economies, and the growing need for efficient tools and machinery in them, examples of this are observed in Asia-Pacific and China.
Apart from that, screw compressors also have other applications, such as in the oil and gas, automotive, and life sciences industries. Oil-free screw compressors are often used in the latter to avoid possible contamination from oil-related machines.
Oil-free screw compressors are also used in the food and beverage industry, mostly to maintain air quality standards, where avoiding contamination from external particles in compressed air is mandatory.
Up to 30% of the industrial jobs could not be done without high-density, high-pressure air pumped by rotary-screw compressors, and their malfunction could result in extra cost in time and money. Analysts estimate that between 5% and 20% of the productivity of factories is lost to downtime, with an estimated cost of unplanned downtime of $ 50 billion each year for industrial manufacturers.
How do sealing solutions like Omniseal® polymer rotary lip seals work in rotary-screw compressor systems to help to ensure reliability and performance?
The Strength of Rotary Lip Seals
Omniseal® rotary lip seals are made from several types of PTFE, and they were presented to the market in the early 70s. They were created in order to bridge the gap between conventional elastomer lip seals and mechanical face seals to significantly contribute to the improvement of performance.
They can also function in extreme temperatures, aggressive media, with high-surface speeds, under high pressure, and do not require lubrication. Therefore, they are used in pumps, gearboxes, motors and mixers, in addition to compressors.
Omniseal Solutions developed their own Omniseal® metal-cased lip seals to function properly in industrial applications, for example, oil-free and lubricated compressors. The seal retains the oil inside the airend, but also keeps dust, air and dirt from sucking in along the rotating shaft when the machine is off load. Rubber lip seals did not prove to be effective as they were not able to withstand high pressures and this can lead to a leak.
One might wonder how strong the rotary screw technology is, and it may also come as a surprise to say that this technology is also being used in supercharges, and can contribute to the increasing of pressure and density of fuel in high-performance automotive internal combustion engines, which ultimately helps them work harder.
Supercharging adds about 46% more horsepower and over 30% more torque to engines, and Omniseal Solutions also provides rotary lip seals for this application.
Omniseal® lip seals address high speeds - shaft speed of 4,000 – 14,000 RPM and surface velocity of 525 – 7,000 feet/minute; as well as temperatures of up to 350 °F / 177 °C. They address vacuum pressures of 25 PSI (1.7 BAR), require limited lubrication, and offer an extended seal life.
Why Reliable Sealing Solutions Should be Used in Screw Compressors
As discussed, rotary screw air compressors are used in a variety of businesses around the world and are very versatile. With this global need, there are many benefits that this machine’s technology and the critical seals inside them provide. Following are four aspects of rotary lip seals to bear in mind:
- Cost-effectiveness: Rotary screw compressors are designed to be able to operate for long periods of time. When using reliable sealing parts that do not fail, the overall cost of production decreases in most manufacturing and industrial applications. Omniseal® lip seals have proven to exceed the seal life in screw compressors. As a consequence, the warranty claims for manufacturers are greatly reduced. They also offer tight leakage control, with vacuum pressure up to 400 PSI (27 BAR), and can be run with a wide range of lubricants.
- Safety and stability: Rotary screw air compressors contribute to the function of a variety of machines and systems, which operate in extreme temperatures or conditions. A crucial requirement is for them to be able to handle furnace-like heat, extreme cold and high pressure. The life of the Omniseal® rotary lip seals exceeds 15,000 hours, these can handle a variety of temperature ranges - from 65 °F to 450 °F (-53 °C to 232 °C), function well under high pressure of more than 500 PSI (34 BAR) and withstand high speeds in excess of 7,000 ft./min (35 m/s). They also meet strict EPA leakage requirements, providing tight leakage control.
- Design efficiency: Rotary screw compressors are adjustable by design. Therefore, they are one of the most efficient and diverse power sources for industrial applications. The same is valid for Omniseal® rotary lip seals. These can be custom-designed to be compatible with a wide range of oils, refrigerants and abrasive media.
- Storage: Accessing and storing rotary screw compressors can be difficult; the same can be said for the internal parts. Omniseal® rotary lip seals are easily installed as they accommodate a small space within the system.

This information has been sourced, reviewed and adapted from materials provided by Omniseal Solutions.
For more information on this source, please visit Omniseal Solutions.