When you hear the term ‘research and development,’ it most likely invokes images of test labs, research papers and patents as well as feelings of innovation and analysis. R&D does play a critical part as an investment in technology and future capabilities, which is transformed into new products, processes, and services, providing companies the ability to remain competitive and create value for their customers not only for immediate use but for long term sustainability. The current research environment is fast-paced with the shelf-life of innovations decreasing as a result of competition from China, academic research and startups. According to the PriceWaterhouseCoopers firm, companies such as Amazon, Alphabet, Inc. and Volkswagen spent the most on innovation and improvements in the R&D tune of over $15 billion in 2018. Pharmaceuticals, semiconductor and software/technology companies generally tend to spend the most on R&D due to the extreme growth and need of their consumers.
Why such a great investment?
One of R&D’s major roles is to assist management in tackling uncertainty through the power of knowledge, which is why research departments rely on tools and processes that provide the most precise and accurate input. This is where numerical simulation takes center stage especially for design engineering and manufacturing companies such as Omniseal Solutions.
Design work for any complex system usually involves computation with complex geometries and challenging material/interaction behaviors. Because analytical calculations are usually only possible for simple geometries and simple system behaviors, it then becomes essential to apply numerical modeling and simulation for applications where quantitative assessment is required. Finite Element Method or FEM is a method that helps determine calculations on real component geometries. In addition to FEM for geometric resolution, accurate constitutive models for materials and interactions are essential to accurately simulate real-world systems. The usefulness of the FE was first recognized at the start of the 1940s by Richard Courant, a German-American mathematician, who was able to apply it to a range of problems; however, it was not until several decades passed before the approach was applied generally in fields outside of structural mechanics. Moreover, until the very last couple of decades, the modeling of complex material behaviors initiated for rubbers since the 1940s did not gain significant development into simulation software due to difficult nonlinearity and computation resource requirements. Recent development of robust solvers on software platforms and availability of computation resources helped bring FEM and advanced material modeling together to make numerical simulation what it is today and have an impact in R&D.
Where are simulation processes used?
Specialized robust solvers on software platforms are growing in popularity nowadays and help to realize numerical simulations in technical fields such as solid mechanics, fluid mechanics and chemistry for a variety of industries that require precise data in challenging applications, which include aerospace, automotive, marine, oil and gas and life sciences. Simulations help engineers to understand component and system behaviors, compute interested design quantities and design components for complex applications in extreme conditions. These conditions could range from very low temperatures (e.g., cryogenic) found in space, very high temperatures in commercial airplane engines and oil and gas subsea drilling equipment, and very high pressure in oil and gas, industrial and UHPLC systems.
Omniseal Solutions has conducted simulations for a number of projects:
- Space applications (Fig. 1) – control valves, feedlines and manholes
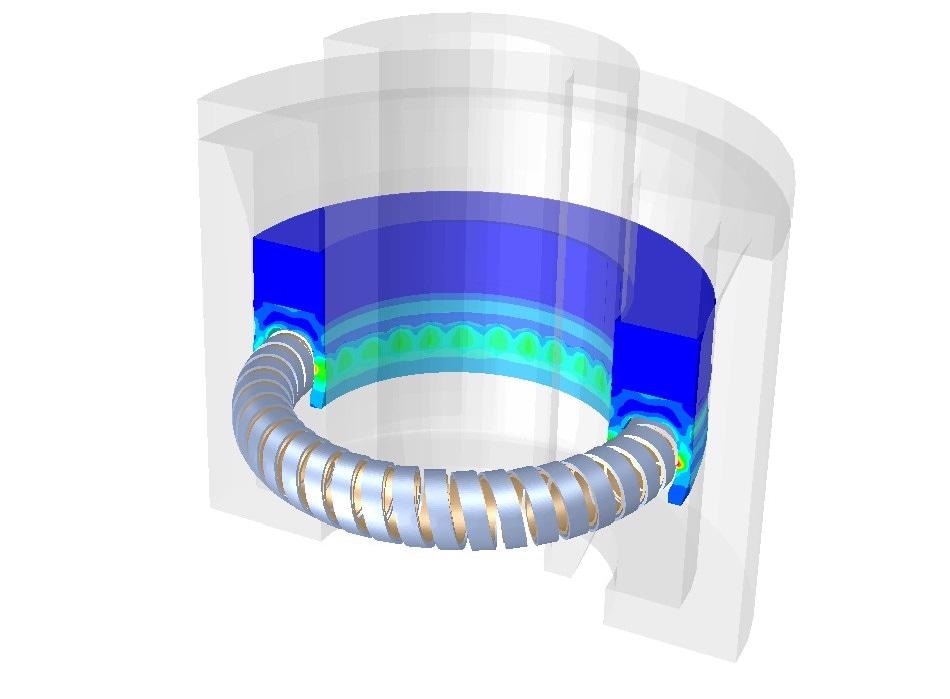
Fig. 1. Rod Seal
- Aerospace applications (Fig. 2) – jet engines and gearboxes
Fig. 2. Omniseal® RACO® Spring
- Oil and gas applications (Fig. 3) – butterfly valves, ball valves, couplers and loading arms
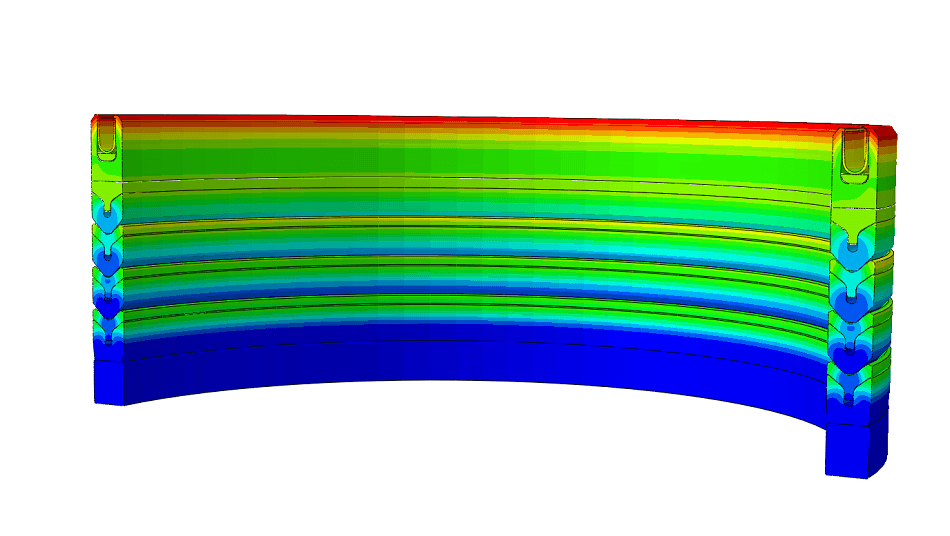
Fig. 3. HPHT Seal
- Life sciences applications (Fig. 4) – UHPLC pump seals and components for respiratory equipment
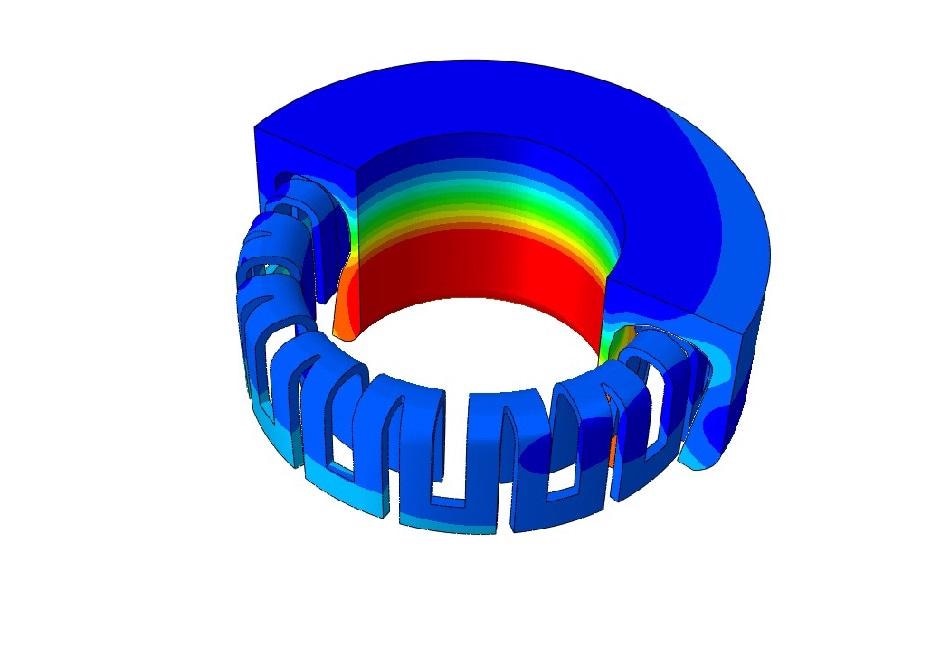
Fig. 4. High Pressure Seal
- Industrial applications (Fig. 5) – swivel joints and compressors
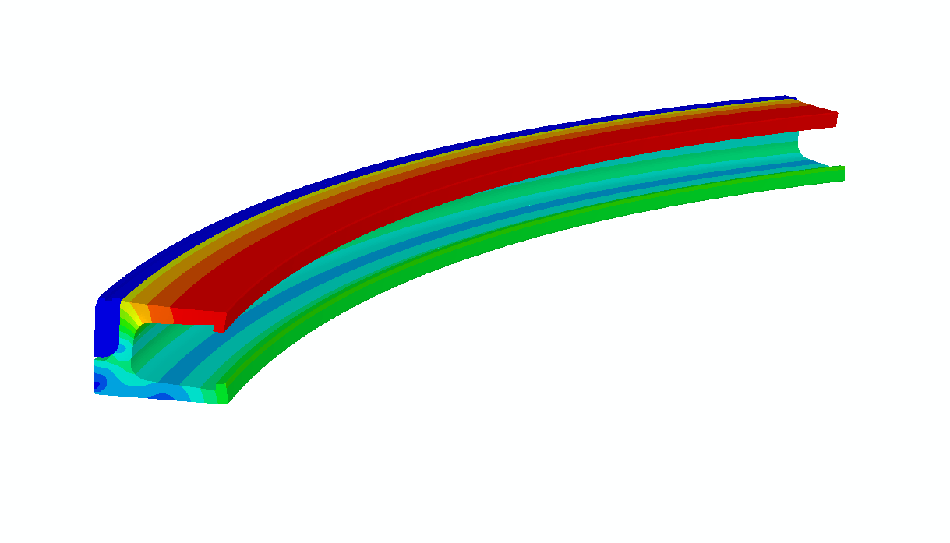
Fig. 5. Swivel Seal
- Automotive applications (Fig. 6) – piston seal rings and transmission bearings
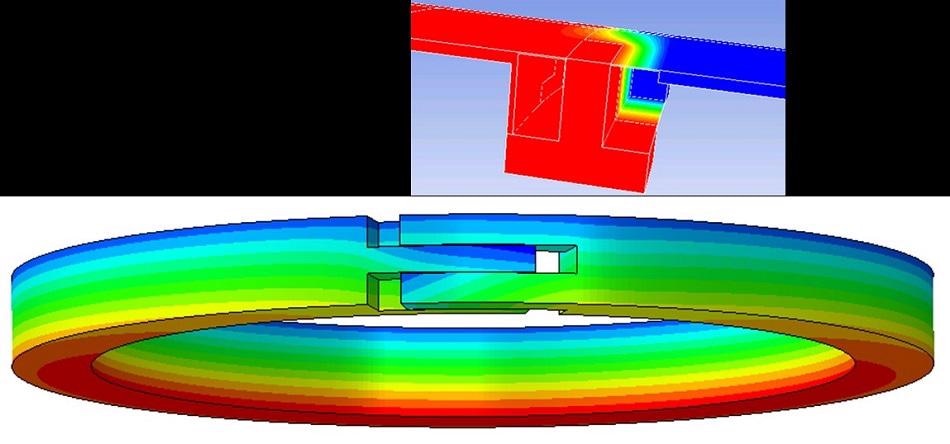
Fig. 6. Leakage through Seal Ring Joint
How are simulation processes used to benefit companies and their customers?
In the case of Omniseal Solutions, these simulations help in four critical ways.
- Customer confidence in products: Accurate simulations reduce repeated testing, which saves the customer cost and decreases time to market.
- Design improvements and knowledge base: Accurate simulations help their engineers design more effectively with computations and decrease trial-and-error thus iteration cycle. Their engineers are also able to better understand system behaviors in order to provide expertise when communicating with customers, displaying their technical leadership in this field.
- Informed decision-making: Accurate simulations decrease trial-and-error practices therefore product/material development can be interpreted in a more reliable manner to enable faster selection and direction.
- Safety: Accurate simulations provide a way to understand safe opportunities and alternatives by closely looking at how certain challenging conditions can affect performance of their seal or polymer part in core systems.
What type of simulation tools are used?
In the past, companies relied on trial-and-error methods, simplified analytical calculation, or qualitative/comparative finite element analysis of simple systems with simple material and interaction properties. However, there are now better ways to implement accurate computations for unprecedented large complex systems using several simulation platforms today.
Omniseal Solutions uses Simulia and COMSOL to handle complex geometries (2D and 3D) and interactions (contact, transport of chemicals, reaction, friction, wear, adhesion, etc.). Advanced material constitutive models are also developed and used to simulate viscoelastic, plastic, creep, relaxation and large deformation behaviors which are typical in polymer sealing applications. Omniseal Solutions also conducts many mechanical tests (compression, tension, creep, relaxation in a large range of temperature for polymer materials) to extract material parameters for accurate quantification. The types of simulation that they work with are solid mechanics including buckling and modal analysis, fluid mechanics, heat transfer and combinations (or multi-physics).
Through R&D, companies can grow by designing new products and improving their existing ones to support customers. Numerical simulation is just one tool in R&D’s range of resources, which Omniseal Solutions has invested in along with increasing laboratory space and skilled research and design engineering team members. If you would like to find out about simulation or their other resources, please contact [email protected] or visit https://www.omniseal-solutions.com/.
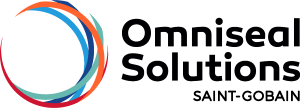
This information has been sourced, reviewed and adapted from materials provided by Omniseal Solutions.
For more information on this source, please visit Omniseal Solutions.