Feb 25 2003
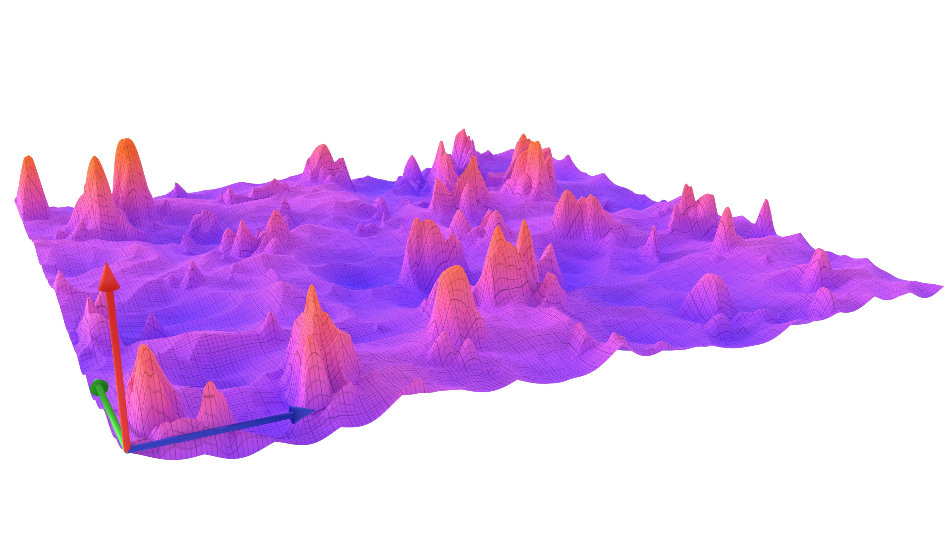
tdhster / Shuttterstock
In the metallurgy field, an ever-increasing range of steel and alloy compositions are used, apart from a large number of processing techniques. These techniques are used in material production through to product finishing.
Surface analysis plays a role in the characterization of these materials, right from their microstructure through to large-scale customer complaints.
The excellent sensitivity of techniques, like secondary ion mass spectroscopy (SIMS), can be useful in determining the material chemistry, specifically for low-level additives, contaminants, or impurities.
Benefits
- Potential detection of corrosion products prior to the appearance of visual proof
- Location of ppm or ppb levels of elements in the microstructure
- Detection of low levels of corrosion accelerators like chlorine
- Clear and accurate determination of the cause of corrosion
Case Study: Corrosion Problems on Steel Wires
The subsequent example demonstrates the use of a combination of a secondary ion mass spectroscopy (SIMS) and X-ray photoelectron spectroscopy (XPS) to completely characterize a corrosion issue on steel wires.
Moreover, localized corrosion has turned up on reels of wire, yet investigations at the manufacturing level did not show any correlation between the problem and the materials used—that is, steel, drawing lubricants, or post-drawing, lanolin protective coating.
X-Ray Photoelectron Spectroscopy Findings
XPS compositional analysis of corroded and uncorroded areas, reveals a considerably higher concentration of iron in the corroded areas, together with lower levels of sodium and calcium. Both sodium and calcium are attributed to the drawing lubricants (Na and Ca stearates).
Table 1. X-ray photoelectron spectroscopy (XPS ) surface compositions (figures in atomic %)
Analysis Area |
Carbon |
Oxygen |
Iron |
Calcium |
Chlorine |
Sodium |
Sulfur |
Corroded |
35.4 ± 1.2 |
50.8 ± 1.1 |
8.1 ± 0.4 |
3.5 ± 0.3 |
0.9 ± 0.4 |
1.3 ± 0.5 |
- |
Uncorroded |
38.9 ± 0.8 |
46.0 ± 0.7 |
4.3 ± 0.2 |
6.2 ± 0.2 |
0.5 ± 0.2 |
3.4 ± 0.4 |
0.7 ± 0.4 |
The XPS images of a corroded area clearly reveal an open iron area (rust) that covers the lower two-thirds of the wire. The corrosion areas are related to striations through the wire in the drawing direction.
The surrounding areas have high concentrations of sodium, calcium, and carbon residues from the drawing lubricants which are consistent with the compositional data. Even though the chlorine image is weak, it correlates with the iron image indicating a relationship between the two.
Secondary Ion Mass Spectroscopy (SIMS) Findings
SIMS mass spectra, depth profiles, and images displayed a consistent pattern. The organic levels within the corrosion spots are considerably low when compared to the concentrations of inorganic contamination and the corrosion products observed.
Tungsten-containing particles, as tungsten oxide, exist both in and around the corrosion spots. This is due to the break-up of the wire drawing that dies at the time of processing.
It is obvious that the corrosion occurs as a direct result of a reduced level of lubricant during wire drawing, which, in turn, leads to the break-up of the drawing dies. The roughness of the surface and the reduced level of organic material make the steel vulnerable to typical aqueous corrosion, which is potentially expedited by the presence of chlorine.