Sponsored by QATMApr 22 2020
Compared to classic testing applications, hardness testing in powder metallurgy needs completely different procedures and parameters. Samples must be prepared well to permit the hardness test and powder must be embedded in resin, for example, with a hot mounting press. The materialographic specimen must then be polished to get a clean surface for hardness testing.
Test Procedure and Test Methods
Non-ferrous material is usually tested using Vickers or Brinell test methods (depending on the workpiece and application) using test forces between 2.5 and 1000 kg.
The requirements for testing of powder materials are extremely different: a small particle size (<0,1 mm particle size) requires small indent diagonals and very low test forces which are only possible with Vickers test methods.
For the aluminum powder in this example, we expect an estimated hardness between 25 and 35 HV which means results of test forces over 15 g (HV0.015) may already correspond to Vickers DIN EN ISO and ASTM standards (standard requirement: Vickers indent diagonal >20 µm). The testing is also possible on smaller particles (but not according to standard) if the hardness tester can perform even lower test forces.
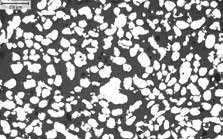
Figure 1. Embedded Aluminum powder / polished surface / 4x microscope lens. Powder particles polished down to half of the particle size or big particles are suited best for hardness testing with meaningful results.
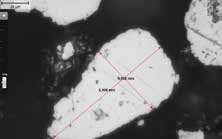
Figure 2. Size of an aluminum powder particle measured in hardness testing software (40x lens).
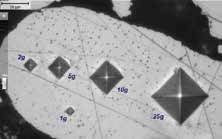
Figure 3. Comparison of Vickers indent sizes: HV0.001, HV0.002, HV0.005, HV0.01 and HV0.025 – Test forces between 1 g and 25 g.
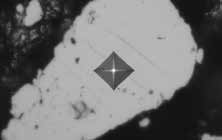
Figure 4. Hardness result: 30.3 HV0.005 tested in the middle of the cross-section of the aluminum particle.
QATM – Hardness Testing
QATM is focused on the development and manufacturing of innovative high-end products for hardness testing. Further to the large scope of versatile standard machines, QATM is also specialized in the planning and realization of customer-specific solutions.
- Rockwell Hardness Testers
- Fully Automatic Hardness Testing Plants
- Micro Hardness Testers
- Clamping Fixtures
- Universal Hardness Testers
- Customized Hardness Testers
Requirements for Hardness Testers in Powder Metallurgy
- Optical measurement system with high contrast at large magnification
- Simple operation
- Low Vickers test forces
- High accuracy in slide and turret movement
- Structured result management and reporting
Conclusion
A powerful Vickers microhardness tester such as the Qness Q10/30/60 is required for determining the quality of powder materials. Either the basic semi-automatic “M” version or the professional fully automated “A” or “A+” models are the perfect choices for powder material applications, depending on the number of tested samples.
The hardness testers are even able to utilize the integrated automatic image evaluation next to automatic brightness and focus adjustment, depending on the test force and surface preparation. Reporting tools and export functions enable the creation of test protocols or data export to data management systems.
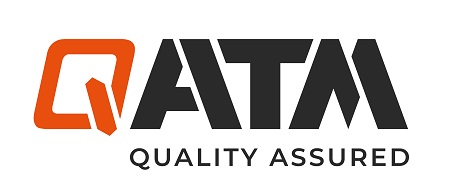
This information has been sourced, reviewed and adapted from materials provided by QATM GmbH.
For more information on this source, please visit QATM GmbH.