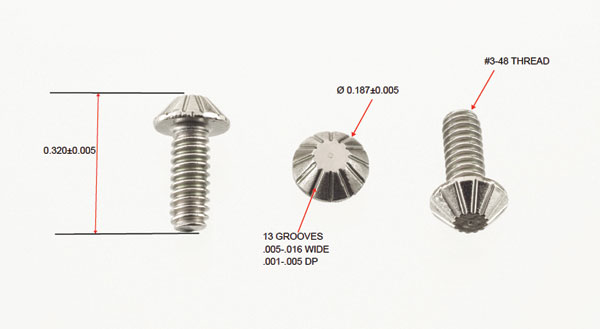
Image Credit: Sussex Wire
Collaborations between Sussex Wire and a Fortune 500 global pharmaceutical services leader has led to the design and production of a replacement stainless steel insert screw. It meets these aims:
- Improvements in adjustment control
- Mitigation of contamination
- Increases in the geometry and tolerance of component parts
- Supply is more than 100,000,000 pieces per year
A net shape micro screw was designed by Sussex Wire. It produced no scrap materials, and during the process, machine automation and sensor controls were developed to guarantee six sigma yield while removing expensive inspection by the customer. Sussex Wire’s trademarked manufacturing cell control system removed the pre-existing condition of malformed and contaminated parts getting to the customers of the company.
Usage
Custom rubber over mold stainless steel precision drug delivery control insert screw
Material
302HQ Stainless Steel
Production Process
- Cold Heading
- Upsetting
- Micro Threading
- Proprietary Thread and Concentricity Detection System
Globally, Sussex Wire is a pioneer in collaborative design, development, production and control of miniature and micro-miniature metal components. This is aimed at customers looking for an optimal solution for yield, strength, assembly and cost through the application of cold forming technologies.
Over the world, mechanical design and assembly firms depend on Sussex Wire for their most innovative near-net-shape part requirements to remove material scrap, enhance mechanical strength and decrease expensive secondary operations.
Vertically integrated LEAN practices in design, production, order and global inventory management are employed by Sussex Wire. This includes stock custom miniature and micro components for JIT delivery to customers internationally in the Medical, Aerospace, Automotive, Energy, Consumer Electronics, Appliance, Defense and Semiconductor markets.
The engineering team at Sussex Wire applies advanced development, materials characterization, tooling and production knowledge to develop cost-efficient manufacture routines for every customer's needs.
By utilizing finite element analysis, quick-turn prototyping, CAD/CAM, soft tooling and in-house tool-making, Sussex has the knowledge and skills to move any business project into production quickly.
Benefits
- 100% net shape, so there is no scrap material left over
- Six Sigma in process control
- Work hardening improves the durability of components and the product life cycle
- Custom contamination-free manufacturing cell
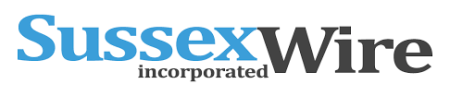
This information has been sourced, reviewed and adapted from materials provided by Sussex Wire Inc.
For more information on this source, please visit Sussex Wire Inc.