Lactose is a commonly used pharmaceutical excipient available in a variety of grades, depending on the application. For example, in Dry Powder Inhalers (DPI) lactose particles are used to carry the fine particles of the Active Pharmaceutical Ingredient (API) from the capsule, before being trapped in the throat and subsequently swallowed as the API continues to the lungs.
Here, the properties of the lactose will influence the performance of the DPI, from manufacturing processes such as filling and dosing through to drug release.
Lactose is also widely used in granulation and tableting processes, where it is often supplied in a milled form, consisting of fine particles with a rough surface texture, resulting in a high surface area and irregular morphology. These properties are typically associated with highly cohesive and compactable powders.
In both processes and many others, in order to ensure consistent process performance and product quality, it is critical that the properties of the lactose are uniform, not only throughout a given batch but also between batches.
In the study below, three milled lactose products from DFE Pharma: Pharmatose 200M EU, Pharmatose 200M NZ, and Lactochem Fine Powder (LCFP), were evaluated and compared to three competitor products all intended for tableting applications. Three batches of each lactose were tested in triplicate using the FT4 Powder Rheometer® Dynamic Flow test methodology to assess intra- and inter-batch variability. The Relative Standard Deviation (RSD) of Basic Flowability Energy (BFE) measurements was used to determine batch consistency.
Intra-Batch Repeatability
Intra-batch variability across all grades was observed to be very low, (RSD <5%).
This highlights the consistency of the various lactose grades suggesting no significant variation within the same batch, regardless of grade or supplier.
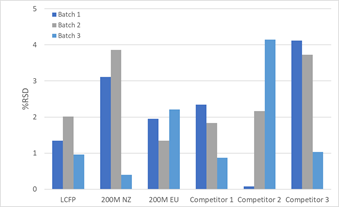
Image Credit: Freeman Technology
Batch-to-Batch Variation
Following intra-batch testing, inter-batch consistency was assessed. This is particularly important as consistency in raw materials will help achieve final product uniformity and quality, with minimal adjustment of process parameters.
DFE Pharma products generated a consistently low RSD, with a maximum of 6% observed for 200M EU. This contrasts sharply with the competitor products which generate RSD values ranging from 9 to 15%.
This highlights the consistency of the various lactose grades produced by DFE Pharma.
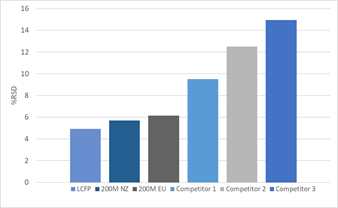
Image Credit: Freeman Technology
Conclusions
Measuring the dynamic flow properties of different lactose batches using the FT4 Powder Rheometer, enabled intra-batch consistency to be confirmed. However, when assessing three different batches of the same product, the batch-to-batch variation could be identified and quantified. LCFP was shown to be the most consistent product.
By ensuring that batches of a given raw material have consistent flow properties, the performance of a powder through a given unit operation can be maintained over time.

This information has been sourced, reviewed and adapted from materials provided by Freeman Technology.
For more information on this source, please visit Freeman Technology.