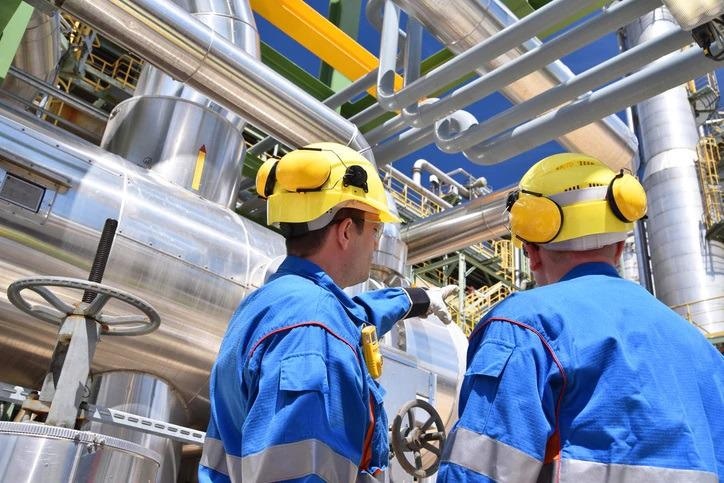
Image Credit: Thermo Fisher Scientific - Elemental Analyzers and Phase Analyzers
With the growing regulations in traceability, reliability, safety, and regulatory compliance, material verification has become a critical component to reliability and safety programs throughout the energy and manufacturing markets.
While industry material specifications are getting more and more specific, the demand for various PMI testing in the field has been increasing steadily. The portable handheld LIBS, handheld XRF, and OES analyzers are all common technologies used to perform reliable, accurate, and fast analysis.
Each of the technologies has its own distinctive advantages and enables the user to perform a quantitative and qualitative analysis of the material composition. The industry’s common term for performing any of these techniques is Positive Material Identification (PMI).
All three technologies are used in several different ways to guarantee compliance with a quality management program. A few examples include:
- Verification of incoming materials to ensure that the components or products are the right alloys
- Fabrication to ensure the welded component and their filler metals are the right alloy, meeting the specified material requirements
- Sorting and identifying mismarked or unknown materials to ensure the correct material is used for the specified process
- Retro-PMI in-process applications for the verification of materials currently in process for compliance with the required specifications
Understanding the differences and limitations in each of these techniques is vital when carrying out material analysis. The analyzer can be utilized across several industries on a wide range of components. They are constantly used in both production and asset integrity management programs in aerospace, nuclear, pharmaceutical, fabrication, power generation, and refining petrochemical.
These verification programs help to identify unknown materials, prevent loss of life or injury, improve product quality, and eliminate the expensive mix-up of rogue materials.
There are different requirements for each verification program when it comes to identifying the material for analysis. Each material or alloy will have various elemental restrictions and requirements. By understanding each technique, it helps to determine which technology is appropriate to verify the material.
X-Ray Fluorescence
X-ray Fluorescence (XRF) is the most commonly used Non-Destructive Test (NDT) method, which offers the user a portable handheld analyzer that produces accurate, fast results.
An x-ray tube is utilized within handheld XRF analyzers to emit an x-ray beam into a sample. This excites the electrons, and they are displaced from the inner shell. The vacancy from the inner shell is then replaced by an outer shell electron.
As this electron fills the inner shell vacancy, it releases energy by way of a secondary X-ray. This secondary energy release is called fluorescence. Each element that is present will emit unique energy characteristics of itself.
Measuring the unique characteristic of released energy emitted from the sample enables the determination of the elements present. This is known as qualitative analysis.
Then, the intensities of the unique energy are measured and the correction factors are applied, making it possible to measure the quantity of each element in the sample. This is known as quantitative analysis.
There are some XRF analyzers that are capable of measuring light elements in low concentrations, such as Magnesium, Aluminum, Sulfur, Phosphorus, and Silicon.
XRF has limitations to what elements can be measured. XRF cannot be used to measure elements that are lighter than Magnesium. This XRF limitation makes it incapable of grading materials such as carbon steel, low carbon stainless steels, and low alloy materials due to XRF analyzers not being able to measure carbon.
For example, XRF can be used to measure the elements necessary for the identification of 316 stainless steel but cannot measure the Carbon required to determine if that same 316 material is H or L grade. Carbon is the fundamental element needed for the verification of the different grades of stainless steels, i.e., 316H or 316L.
Optical Emission Spectroscopy
Optical Emission Spectroscopy (OES) is an optical method that can be used to detect nearly any type of elements, including carbon and light elements in a range of different matrixes, including nickel, stainless steel, and carbon steel, etcetera.
OES is a technique used to grade material by measuring the element carbon to identify alloys such as high carbon or low carbon stainless steels, low alloys such as 86xx series, 41xx series, and 10xx series carbon steels.
Whilst OES is thought of as a portable technique, it would be better to classify it as a transportable technique. Depending on the manufacturer, OES instruments vary in size and weight but can weigh over 45-60 lbs and require an argon tank that, depending on its size, can weigh around 20 lbs.
Usually, the instrument and its argon tank are made more mobile by transporting them on a cart. Due to the size and weight of this field mobile OES, using it in elevated work areas could entail mechanical assistance to help to lift the OES instrument higher.
When carrying out an analysis with OES, each sample for analysis needs sample preparation, utilizing a grinder in which a zirconium aluminum oxide sanding disc prepares the surface. In any OES analysis, sample preparation is a crucial step because a sample that is not properly prepared will produce inaccurate and undesirable results.
Atoms are also excited in the OES technique, but the excitation energy comes from a spark formed between the instrument electrode and the sample. Unlike XRF, where an x-ray tube is utilized in order to irradiate the sample, OES uses energy from a spark that causes light emittance from the electrons in the sample, which is then converted into a spectral pattern.
Unique color of optical light is produced from each element. The OES analyzer can produce quantitative and qualitative analysis of the material composition by measuring the peak intensity in this optical light of the spectrum.
Although OES is considered to be a nondestructive testing method, the sample has to be prepared with a mechanical sanding device, and the spark leaves a small burn on the sample surface that must be removed post-analysis.
Laser-Induced Breakdown Spectroscopy
Laser-Induced Breakdown Spectroscopy (LIBS) has been used for several years and is a technique primarily used in laboratory equipment.
Recent advances in technology have meant that the technique has been developed into a portable handheld analyzer enabling the measurement of carbon in the field for the grading of materials and material identification.
As with OES, argon is still needed to analyze carbon in a LIBS handheld analyzer. Instead of an external argon tank, hose connection, and regulator to the OES unit, the LIBS analyzer utilizes a consumable argon cartridge that is incorporated within the instrument. The instrument weighs less than 6.5lbs even with the analyzer’s battery.
Sample preparation is still necessary for analysis, but the handheld size of the instrument, the sanding discs, and the grinder can all fit into a small case, allowing transportation to pipeline ditches, elevated working platforms, and hard to access areas with minimal effort, allowing the user true field portability in a handheld carbon analyzer.
In the analysis of the sample, proper sample preparation is a crucial step. Weak sample preparation will produce undesirable results. With appropriate sample preparations, the user can accomplish reliable, accurate, and fast results.
The LIBS analyzer can be utilized for the measurement of light elements in low concentrations, for example, aluminum, silicon, and carbon. The LIBS analyzer enables the user to easily grade H and L grade stainless steels, low alloys, and carbon steels.
The instrument can also achieve residual element (RE) or carbon equivalent (CE) calculations programmed by the user in an intuitive and easy-to-use interface.
The LIBS technique uses a pulsated laser to ablate the sample surface and create a plasma. The electrons from the cooling plasma are excited as the plasma cools down, resulting in the plasma emitting light.
Each of the periodic table’s elements produces a unique LIBS spectral peak. Using a detector to measure the unique characteristics of light emitted makes it possible to identify the presence of distinct elements in the sample.
The chemical composition can be quickly determined and quantified in weighted percent concentrations (%), or parts per million (PPM), by measuring the peaks of light and their intensities within the sample.
Conclusion
There are many viable and accurate technologies for performing chemical analysis in the field. LIBS, OES, and XRF technologies give the user a portable option to grade or verify material.
Understanding the limitations and differences of each of these technologies will aid the user in selecting the instrument that meets the specified requisites of the material that is being analyzed.
Acknowledgments
Produced from materials originally authored by James Terrell from Thermo Fisher Scientific.
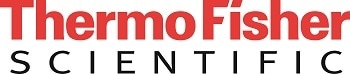
This information has been sourced, reviewed and adapted from materials provided by Thermo Fisher Scientific – Handheld Elemental & Radiation Detection.
For more information on this source, please visit Thermo Fisher Scientific – Handheld Elemental & Radiation Detection