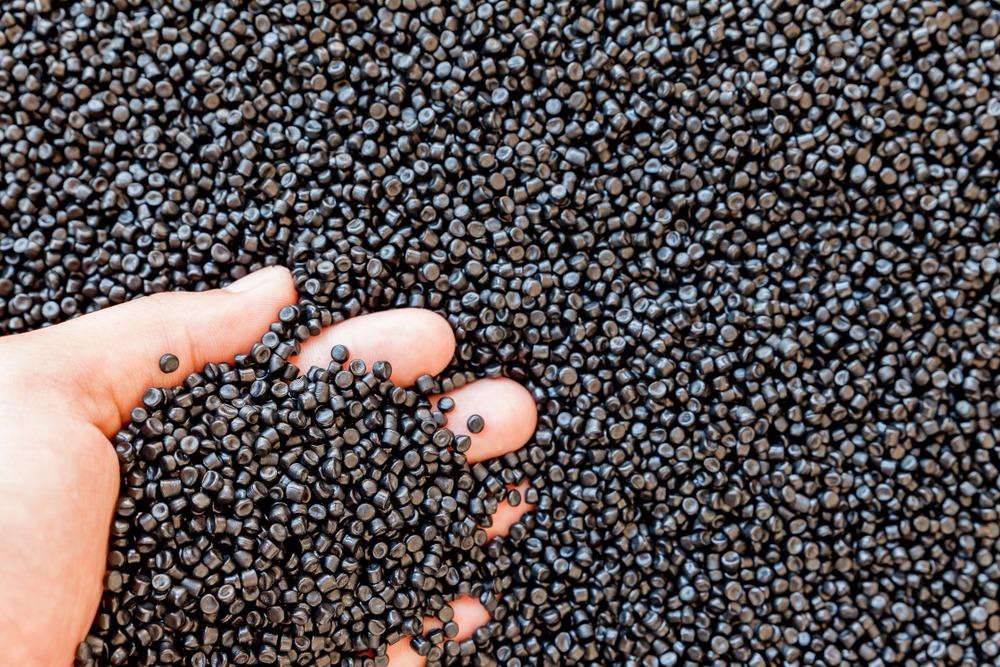
Image Credit: Kriengsak tarasri/Shutterstock.com
An innovative polymerization process developed by Polymer Mimetics, a UK specialty chemical manufacturer, enables high-performance polymer manufacturing with reduced raw materials consumption and improved yield and processing efficiency.
Polymer materials manufacturing is dominated by two synthetic processes - a chain-growth polymerization process and a step-growth polycondensation process. During the polymerization process, the material building blocks, or monomers, are attached sequentially to the active end of the growing polymer chain, while the polycondensation process combines two or more different monomers in an alternating, continuously growing structure.
Globally, these methods are used to synthesize the majority of the polymer materials used for the manufacture of commercially important plastics, fibers, resins, and rubbers.
Hyperbranched Polymers Attract Interest from Researchers
Throughout the years, the significant developments in polymer materials science and technology have resulted in the refinements of established synthetic methods and new polymerization routes, enabling the synthesis of specialty polymers with unique structures and superior properties.
The systematic development of branched polymers started with the discovery of long-chain branched polymers in the 1940s. It continued with the synthesis of the first star-shaped polymers in the 1960s, and the invention of dendrimers and hyperbranched polymers in the 1980s and 1990s.
Hyperbranched polymers are polymer chains with a densely branched three-dimensional structure and a large number of end-groups. The hyperbranched polymers form the third major class of polymer architecture, coming after the linear and cross-linked polymers.
Hyperbranched polymers have received much industrial attention due to their unique physical and chemical properties resulting from their highly branched, dense and irregular structure. This leads to excellent solubility (compared to linear polymers), low solution viscosity, and enhanced end-group functionality.
These properties ensured the commercial success of the hyperbranched polymers that have been commercialized for several applications, such as functional coatings for surface modification, additives for improving rheology, and flow in plastic processing.
Technology Development Driven by Knowledge Transfer
Scott Bader Company Ltd., a global manufacturer of adhesives, coatings, and functional polymers based in Wellingborough, UK, partnered with the University of Liverpool in the UK to create a joint venture company, called Polymer Mimetics, aiming to bring the next generation of sustainable high-performance branched polymers to the market.
Based in the Liverpool Science Park, Polymer Mimetics is an example of the academia-to-industry translation of novel synthetic chemistry technologies. The proximity of the company's high specification lab facilities to the University of Liverpool would allow its research team to carry out fundamental research in close collaboration with their colleagues from academia.
Specialized Equipment for Superior Polymer Production
A key factor enabling the Polymer Mimetics team to develop next-generation polymers, which are both sustainable and degradable, and with a wide range of functionalities, is the company's dedicated laboratory equipment supplied by Asynt, a UK-based leading manufacturer and supplier of equipment and consumables for biology and chemistry research laboratories.
Asynt supplied a wide range of equipment, including DrySyn Vortex overhead stirrer platform, that enables Polymer Mimetics scientists to develop the next generation of polymers by conducting multiple reactions in parallel under well-controlled conditions. This increases the number of candidate polymer compounds that can be synthesized and tested, improving work efficiency and processing costs. Once the initial results are evaluated, the production can be scaled up under the same reaction conditions.
Asynt's proprietary DrySyn heating blocks, temperature control systems, and CondenSyn air-cooled condensers for reflux reactions have eliminated the oil baths and heating mantles, and minimized water usage, improving the environmental footprint of the polymer manufacturing process.
Innovative Blend of Polymerization Strategies
Polymer Mimetics' superior polymer production platform combines the benefits of the conventional step-growth and chain-growth polymerization strategies to manufacture next-generation polymers. The company's telomerization-based process exploits the polymer synthesis methods developed by Prof. Steve Rannard and his group at the Department of Chemistry, University of Liverpool.
Telomerization reactions, in contrast to polymerization reactions, lead to oligomers with very low molecular weights. The products are regarded as intermediates between organic monomeric and macromolecular compounds.
Building Blocks for the High-Performance Polymers of the Future
Prof. Rannard's innovative method allows the use of standard commercially available monomers, including sustainably sourced feedstock, as building blocks and does not require expensive catalyst materials. This rapid and highly scalable approach can be extended to the production of high-performance polymers with near-limitless structural and functional diversity.
The opportunity to engineer branched molecular architectures with precisely controlled properties, functionality, and built-in degradability opens up vast possibilities for industrial applications.
Next-Generation Polymers for Industrial Applications
To fully exploit the opportunity, Scott Bader Company has acquired an exclusive global license to all background patents and know-how that underpins the new polymer synthesis technology and forms the basis of Polymer Mimetics.
The company expects that its new technology would enable the manufacturing of numerous new materials with a wide range of industrial applications, such as coatings, adhesives, lubricants, personal care products, and degradable high-performance polymers produced from sustainable feedstocks.
At the same time, this commitment aligns very well with Scott Bader Company's long-term goals for reduced environmental footprint and sustainability of its products.
References and Further Reading
S. R. Cassin, et al. (2020) Hyperbranched polymers with step-growth chemistries from transfer-dominated branching radical telomerisation (TBRT) of divinyl monomers. Polym. Chem., 11, 7637-7649. Available at: https://doi.org/10.1039/D0PY01309A
B. I. Voit and A. Lederer, (2009) Hyperbranched and Highly Branched Polymer Architectures—Synthetic Strategies and Major Characterization Aspects. Chem. Rev. 109, 5924–5973. Available at: https://doi.org/10.1021/cr900068q
The University of Liverpool (2020) University and Scott Bader Company Ltd announce joint venture to develop a novel polymer chemistry platform. [Online] https://news.liverpool.ac.uk/ Available at: https://news.liverpool.ac.uk/2020/06/30/university-and-scott-bader-company-ltd-announce-joint-venture-to-develop-novel-polymer-chemistry-platform (Accessed on 20 January 2021).
BP&R (2020) Asynt and Polymer Mimetics speed up development of high performance polymers. [Online] https://www.britishplastics.co.uk Available at: https://www.britishplastics.co.uk/materials/asynt-and-polymer-mimetics-speed-up-development-of-high-perf (Accessed on 20 January 2021).
LaboratoryTalk (2020) Speeding Up the Development of Novel, High Performance Polymers. [Online] www.laboratorytalk.com Available at: https://laboratorytalk.com/article/2031066/speeding-up-the-development-of-novel-high-performance-polymers (Accessed on 20 January 2021).
Disclaimer: The views expressed here are those of the author expressed in their private capacity and do not necessarily represent the views of AZoM.com Limited T/A AZoNetwork the owner and operator of this website. This disclaimer forms part of the Terms and conditions of use of this website.