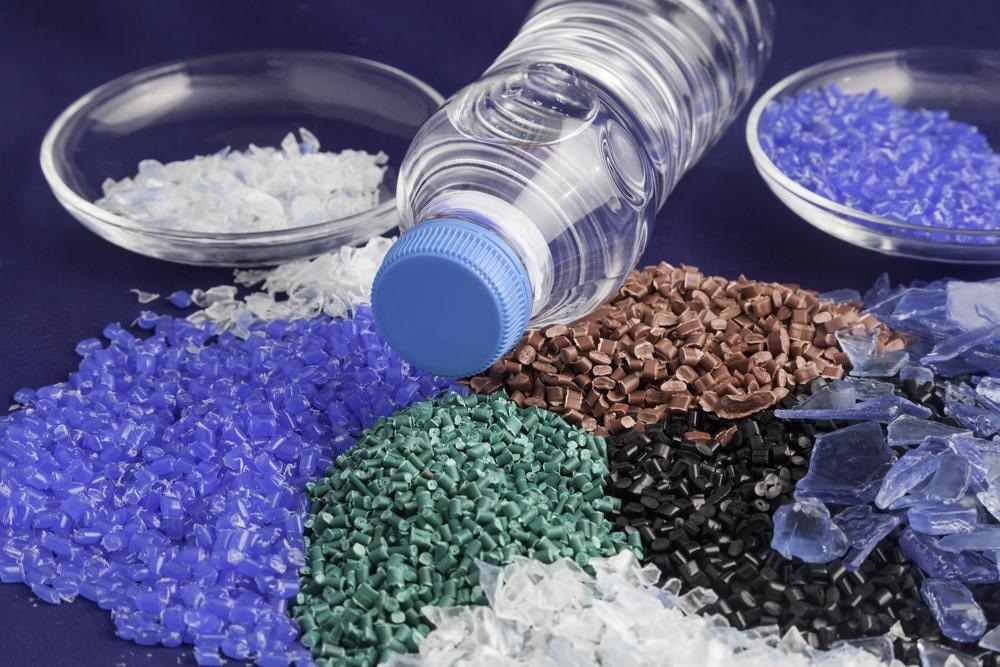
Image Credit: Aykut Erdogdu/Shutterstock.com
Redirecting plastic lifecycles from linear to circular economic models is one of the grand challenges in modern material science. Responding to that challenge, researchers from the University of Groningen in the Netherlands and the East China University of Science and Technology (ECUST) in Shanghai created a recyclable polymer that can be easily disassembled into its constituent monomers. These molecular building blocks can be repeatedly reassembled into new plastic materials without loss of performance or quality.
Most of the traditional petrochemical-derived polymer materials rely on the formation of macromolecular networks, held together by high-strength covalent bonds, to achieve their exceptional mechanical properties and durability throughout the material's life span. However, breaking those bonds cost-effectively is very challenging, making the majority of the modern polymers challenging to repair and, when reaching end-of-life, exceptionally difficult to reuse or recycle.
How to Make Fully-Recyclable Plastics?
In contrast to synthetic polymer materials, biological systems take a much different approach to ensure stable, long-term performance coupled with ease of recycling. Bone tissue, for example, undergoes constant remodeling – sequential resorption of bone tissue and deposition of new bone to meet changing mechanical needs and repair microdamage in the bone matrix. Through these cycles, bone tissue heals in response to damage and also recycles end-of-life material.
More renewable resources are being used in the production of polymers. Monomers such as carbon dioxide, vegetable oils, and other biologically derived carbohydrates can be used as feedstocks to manufacture a variety of sustainable materials and products, including elastomers, engineering plastics, and resins.
At the same time, unsustainable practices for plastic disposal continue to deplete the world's finite natural resources and damage the environment.
Designing a polymer capable of undergoing an indefinite number of degradation (depolymerization) and formation (polymerization) cycles, similar to the bone remodeling process, would allow the feeding of valuable resources back into the economy in a high-value form rather than down-cycling them as fuel for power generation. Therefore, the chemical recycling process by depolymerization and re-polymerization reduces the demand for finite raw materials and minimizes plastics' negative impact on the environment.
This seemingly ideal strategy has motivated researchers at the Feringa Nobel Prize Scientist Joint Research Center (a joint research institute between the University of Groningen and ECUST), led by Professors Ben Feringa, Da-Hui Qu, and He Tian, to explore a mild process (conducted at ambient conditions) for reversible polymerization-depolymerization of fully recyclable polymers.
Versatile Building Blocks from Nature
Instead of inventing plastics that never breakdown, the international research team created an intrinsically recyclable and self-healable polymer using lipoic acid as a feedstock. Lipoic acid (also known as thioctic acid) is a naturally occurring organosulfur compound that plants and animals synthesize, including humans, and acts as an essential coenzyme for aerobic metabolism.
Lipoic acid features a five-membered ring structure that contains two thiol (sulfur) groups. When the thiol groups are oxidized, they form a unique covalent disulfide (sulfur-sulfur) bond, which can be quickly and repeatedly formed and cleaved under mild reaction conditions.
Hierarchical Self-Assembly of Macromolecular Networks
Upon reduction, the disulfide bond breaks and the sulfur atoms can react with those of another molecule (or monomer), leading to the so-called ring-opening polymerization process.
The lipoic acid molecules also contain carboxyl groups that interact through non-covalent hydrogen bonding. Furthermore, the carboxyl groups readily react with metal ions. Thus, metal ions, such as iron(III), can act as crosslinkers between the poly(disulfide) chains, which results in elastic polymer material.
When polymerized under very mild conditions (at a temperature of 70 °C), lipoic acid forms a polymer network with three different types of chemical bonds: dynamic covalent disulfide bonds, non-covalent hydrogen bonds, and iron(III)-carboxylate coordination bonds.
Consequently, the result is a polymer with remarkable mechanical properties, such as exceptional stretchability and mechanical strength.
Rapid and Seamless Self-Healing
The reversible nature of the dynamic chemical bonds within the lipoic acid macromolecular network contributes to the polymer's extremely rapid self-healing behavior at room temperature. The novel polymer's stress-strain tests revealed that the material recovered approximately 80% of its original elastic modulus within one minute and fully recovered its mechanical properties after five minutes of self-healing.
Fully Reversible Polymerization Permits Feedstock Recovery
Most importantly, the reversible polymerization process allows complete depolymerization of the lipoic acid polymer into monomers. The process takes place in dilute alkaline aqueous solutions, such as sodium hydroxide solution. The monomers can be precipitated by neutralizing the solution (by adding acid). The quality of the recovered monomers is identical to that of the virgin feedstock material.
At present, the solvent-free mild reversible polymerization-depolymerization process enables the recovery of 87% of the monomers. The recovered lipoic acid can be reused multiple times without loss of quality of the final product. The joint research team from China and the Netherlands continues perfecting the process with the aim of 100% monomer recovery.
Sustainable Polymers with Tunable Properties
In the future, the scientists envisage that they can create novel reconfigurable polymers with tunable mechanical properties, including self-healing elastomers and mechanically robust plastics that can be fully depolymerized at the end of their life.
These fully recyclable materials could substitute many non-recyclable plastics in use today and offer prospects for sustainable plastics lifecycles.
References and Further Reading
University of Groningen (2021) Molecule from nature provides fully recyclable polymers. [Online] https://www.eurekalert.org Available at: https://www.eurekalert.org/pub_releases/2021-02/uog-mfn020421.php (Accessed on 18 March 2021).
Q. Zhang, et al., (2021) Dual closed-loop chemical recycling of synthetic polymers by intrinsically reconfigurable poly(disulfides). Matter. Available at: https://doi.org/10.1016/j.matt.2021.01.014
Y. Deng, et al., (2020) Toughening a Self-Healable Supramolecular Polymer by Ionic Cluster-Enhanced Iron-Carboxylate Complexes. Angew. Chem. Int. Ed., 59, 5278. Available at: https://doi.org/10.1002/ange.201913893
Q. Zhang, et al., (2018) Exploring a naturally tailored small molecule for stretchable, self-healing, and adhesive supramolecular polymers. Science Advances, 4, eaat8192. Available at: https://www.science.org/doi/10.1126/sciadv.aat8192
Y. Zhu, et al., (2016) Sustainable polymers from renewable resources. Nature, 540, 354–362. Available at: https://doi.org/10.1038/nature21001
Disclaimer: The views expressed here are those of the author expressed in their private capacity and do not necessarily represent the views of AZoM.com Limited T/A AZoNetwork the owner and operator of this website. This disclaimer forms part of the Terms and conditions of use of this website.