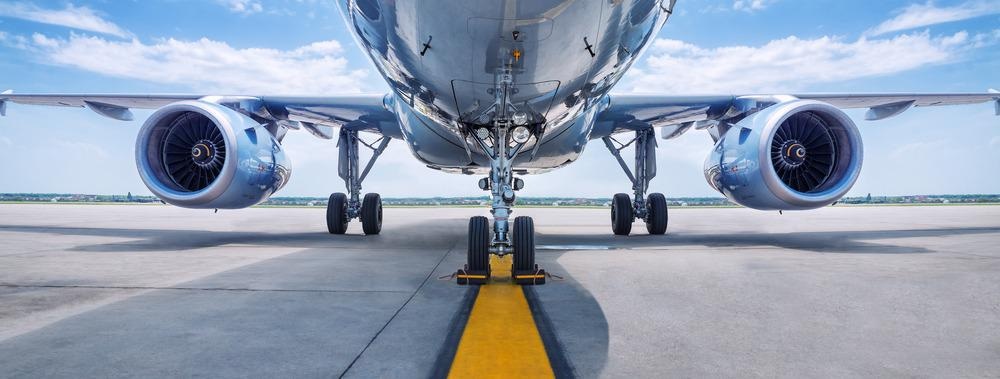
Image Credit: frank_peters/Shutterstock.com
Airplanes are governed by the rules of aerodynamics. It is the study of forces that act on objects in motion through the air and it explains how air moves around objects to produce the force of lift that allows planes to overcome the counterforce of gravity and drag - forces of resistance that act against the force of lift.
Many factors can impact the forces involved in aerodynamics. In aviation, scientists are constantly working towards engineering more efficient aircraft with improved aerodynamic performance. One area of research that has emerged as a major focus of projects attempting to improve aircraft aerodynamic performance is that of investigating and improving how aircraft materials and their properties can impact air resistance. Below, we discuss research that has highlighted the role of surface roughness on aerodynamic performance.
Research into the Roughness of Turbine Blades
Smoother materials have enhanced aerodynamic properties in comparison to those with rough surfaces. Aircraft are, therefore, designed with materials that have low levels of surface roughness. However, external factors can change the nature of a material’s surface over time. Factors such as corrosion, erosion, and deposition that occur during high pressure and high-temperature conditions can increase surface roughness. This is particularly troublesome for turbine blades.
Research has shown that planes that have been in service for considerable hours are more likely to have turbine blades with rougher surfaces. Data demonstrates that roughness increases with the aircraft’s in-service hours and this significantly impacts the turbine’s efficiency.
A 1980 study by Bammert and Sandstede found that sand grain surface roughness on aircraft turbine blades with Ks/C of a range between 10-3 and 10−2 decreases efficiency by 7-14% in comparison with smooth blades.
A study by Boynton et al. Also found that decreasing surface roughness from 10.16 μm to 0.76 μm increases fuel efficiency by 25%, which, over time, could translate into significant fuel savings.
The height and distribution of roughness on the blade are important factors that impact how blade roughness influences aircraft aerodynamics. A study by Suder et al. demonstrated that the blade leading edge and the front half of the suction surface were locations that roughness was most influential. Over 70% of the reduction in aerodynamic performance was accounted for by roughness on these areas of the blade. A further study by Kind et al. supported these findings, demonstrating that roughness on the suction surface resulted in large increases in profile loss, whereas roughness on the pressure surface caused little impact.
Research into the Roughness of Airfoil
Other research has focused on how roughness on the airfoil impacts aerodynamic performance. Airfoil is the curved surfaces of the aircraft that are designed to give the best lift to drag ratio. It is used on the wings, fins, and horizontal stabilizers.
As the roughness of the airfoil surface increases, as does the minimum drag due to the increased friction, which reduces lift. The surface roughness of the airfoil delayed the stall angle and increases lift specifically in the stall region.
Roughness located at the trailing edge of the airfoil shows the minimum drag and maximum lift in comparison with roughness found at other locations. Research has shown that a turbulent boundary layer exists on the rough surface at the point where the laminar boundary layer exists for the smooth surface at the same Reynolds number.
Research continues in both these areas, collecting data on the roughness of airfoil, turbine blades, and other aircraft components. As scientists gather more data, our understanding of how surface roughness impacts aerodynamic performance increases, and aircraft can be better designed to enhance their aerodynamic performance.
Improving Aerodynamics to Reduce Emissions
One major benefit of enhancing the aerodynamic performance of aircraft is that it reduces the amount of fuel required to power the plane. Recent years have seen a rise in awareness of the impact of the aviation industry on emissions, and, therefore, the environment. This has resulted in increasing pressure on the industry to adopt strategies to combat its use of non-renewable fuels.
Numerous strategies have emerged that have shown much potential, such as the development of eco-friendly jet fuel. Another promising strategy is that of targeting the plane’s aerodynamic performance to reduce air resistance and, with it, the amount of fuel needed to power the aircraft.
According to the Air Transportation Action Group, emissions associated with the aviation industry account for roughly 12% of all transportation-associated emissions. In 2019, this equated to 915 million tons of CO2.
By improving aircraft aerodynamics, fuel consumption could be reduced by increasing lift and reducing drag. Over time, this could lead to a significant reduction in fuel usage by the aviation industry, and, therefore, reduce the emissions related to this sector. Further research into the impact of surface roughness on aerodynamics could be key to helping the aviation industry become more environmentally friendly.
References and Further Reading
Bai, T., Liu, J., Zhang, W. and Zou, Z., 2014. Effect of surface roughness on the aerodynamic performance of turbine blade cascade. Propulsion and Power Research, 3(2), pp.82-89. https://www.sciencedirect.com/science/article/pii/S2212540X14000194
Chakroun, W., Al-Mesri, I. and Al-Fahad, S., 2004. Effect of Surface Roughness on the Aerodynamic Characteristics of a Symmetrical Airfoil. Wind Engineering, 28(5), pp.547-564. https://journals.sagepub.com/doi/abs/10.1260/0309524043028136
Lin, Z., 2013. Making aviation green. Advances in Manufacturing, 1(1), pp.42-49. https://link.springer.com/article/10.1007/s40436-013-0008-3
Wang, M., Yang, C., LI, Z., Zhao, S., Zhang, Y. and Lu, X., 2021. Effects of surface roughness on the aerodynamic performance of a high subsonic compressor airfoil at low Reynolds number. Chinese Journal of Aeronautics, 34(3), pp.71-81. https://www.sciencedirect.com/science/article/pii/S1000936120303794
Disclaimer: The views expressed here are those of the author expressed in their private capacity and do not necessarily represent the views of AZoM.com Limited T/A AZoNetwork the owner and operator of this website. This disclaimer forms part of the Terms and conditions of use of this website.