Even though many industrial plastics are recyclable, a significant proportion of the plastic waste is not recycled because of the energy demand and cost associated with the process. Chemically recyclable polymers may hold the answer to the environmental issues caused by end-of-life plastic waste. Recently, researchers from the University of Akron in the US, led by Dr. Junpeng Wang, developed a polymer that can be depolymerized into its constituent monomers for further recycling and circular reuse. The research was published in the journal Nature Chemistry.
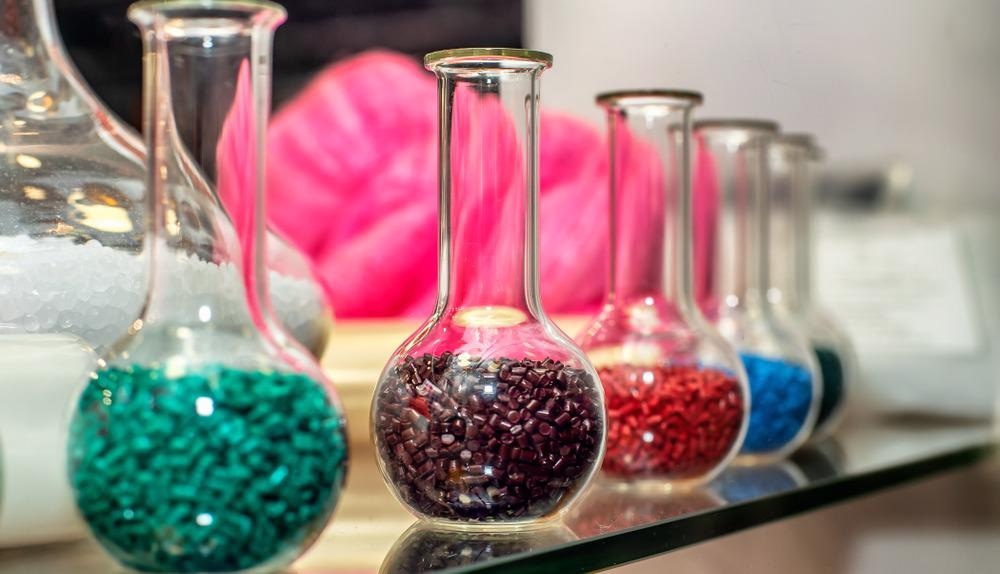
Image Credit: IU Liquid and water photo/Shutterstock.com
The Issue with Waste Polymers
Synthetic polymers play an essential role in modern life and industrial development. Modern polymers boast extensive versatility and superior mechanical properties while offering excellent stability and processability compared to traditional materials such as metal, minerals, and wood.
These properties underpin the dominant place that polymers take in the modern economy. However, due to their long-term durability, waste polymer materials accumulate in the environment and cause serious concerns for a wide range of habitats and ecosystems.
Around 90% of today’s polymers are derived from finite petrochemical feedstocks through unsustainable raw material extraction and manufacturing processes, causing further environmental degradation.
Efforts to address these issues include the development of bio- and photo-degradable polymers and mechanical recycling. Typically, biodegradable plastics, such as those used in food packaging, lack the mechanical strength required for demanding industrial applications.
Photo-degradable plastics show some promise for ultraviolet (UV) photodegradation, but the low reactivity of their hydrocarbon backbone chains significantly limits the rate of degradation.
Mechanical recycling, on the other hand, often results in a substantial loss of quality and mechanical strength, rendering the recycled material unsuitable for high-performance applications.
Ideal Process for the Recycling and Reuse of Post-Consumer Materials
A promising approach that can enable the circular reuse of polymers is the development of chemically recyclable polymers that can be depolymerized at the end of their life, and reusing the constituent monomers in high-value materials with properties equivalent to the original material. Such circular use of plastic materials would preserve finite natural resources and help to resolve end-of-life issues for many industrial products.
A couple of challenges need addressing to establish an effective circular plastics economy based on chemically recyclable polymers. First comes the development of a cost-effective depolymerization process with high selectivity that can convert post-consumer material into the starting material (the concept is known as chemical recycling to monomer or CRM). Then, the properties of the depolymerizable polymers need to match or exceed the properties of the current industrial plastics.
Dr. Junpeng Wang, an associate professor at the School of Polymer Science and Polymer Engineering, together with his colleagues at the University of Akron in the USA, believe that they might have answers to the scientific challenges associated with CRM.
Dr. Wang's team has successfully designed monomer and polymer structures that exhibit high (de)polymerization activity and can deliver properties and performance comparable to existing industrial standards.
Ring-Strain Shifts the Equilibrium
The researchers used a specially designed monomer consisting of cyclooctene (8-membered unsaturated cyclic alkene) with a four-membered cyclobutane ring fused to the eight-member ring.
Once dissolved in a suitable organic solvent, the monomers were subjected to a ring-opening metathesis polymerization (ROMP) reaction in presence of a ruthenium catalyst.
ROMP is a chain-growth polymerization process where cyclic alkenes are converted into polymers. The driving force of the reaction is the relief of the ring strain in the cyclic alkenes. The term ring-strain relates to the energy difference between the cyclic form of the monomer and the polymerized form, which determines whether the reaction is reversible.
Dr. Wang’s team discovered this particular monomer through computational studies during the COVID-19 pandemic when experimental work in the lab was suspended. Instead, the chemists concentrated on computer modeling of the ring strain in a series of cyclooctenes until they discovered that the cyclobutane-fused cyclooctene compound had a surprisingly low ring strain. The discovery meant that both forms, cyclic and polymer, should have comparable energies, and the polymerization reaction should become reversible.
The experimental data showed that cyclooctene-derived monomer can polymerize at room temperature with a yield of 67%. Then, when the reaction was reversed at 50 °C, nearly 90% of the polymerized monomer was recovered by using the same ruthenium catalyst, and without generating or consuming additional materials.
As Dr. Wang explains, the reaction is controlled by the monomer's concentration - at higher concentration polymer forms - while lower concentration shifts the reaction equilibrium towards monomers.
Matching the Properties of Commercial Plastics
The resulting polymer demonstrated excellent thermal stability with a thermal decomposition temperature up to 370 °C (well above the polymer's glass transition temperature). Therefore, the novel polymer can safely be processed into products by conventional high-temperature injection molding without noticeable degradation. Importantly, the recyclable polymer can only depolymerize in the presence of a catalyst. Otherwise, it is highly stable and can withstand heat, corrosion, and mechanical stress.
The compound Dr. Wang's team synthesized is also highly tunable. The properties of the polymer can be adjusted by replacing the functional side chains on the polymer backbone. An imide-functionalized derivative of the polymer showed mechanical properties comparable to those of polystyrene (one of the most widely used plastics). The researchers believe that other derivatives could find multiple uses as infinitely recyclable plastics or rubbers.
The innovative approach taken by Dr. Wang and co-workers can provide a roadmap for the further development of a sustainable and circular polymer economy.
References and Further Reading
D. Sathe, et al. (2021) Olefin metathesis-based chemically recyclable polymers enabled by fused-ring monomers. Nat. Chem. 13, 743–750. Available at: https://doi.org/10.1038/s41557-021-00748-5
Y. Getzler (2021) Low strain, more gain. Nat. Chem. 13, 719–721. https://doi.org/10.1038/s41557-021-00759-2
L. K. Boerner (2021) Chemists make a recyclable polymer with the help of ring strain. [Online] https://cen.acs.org/ Available at: https://cen.acs.org/materials/polymers/Chemists-make-recyclable-polymer-help/99/web/2021/07 (Accessed on 10 August 2021).
K. Welter (2021) Clever ring-strain engineering creates infinitely recyclable polymer – but are they ready to compete with commercial plastics? [Online] www.chemistryworld.com Available at: https://www.chemistryworld.com/news/clever-ring-strain-engineering-creates-infinitely-recyclable-polymer-but-are-they-ready-to-compete-with-commercial-plastics/4013957.article (Accessed on 10 August 2021).
Disclaimer: The views expressed here are those of the author expressed in their private capacity and do not necessarily represent the views of AZoM.com Limited T/A AZoNetwork the owner and operator of this website. This disclaimer forms part of the Terms and conditions of use of this website.