Concrete is a valuable construction material, but like everything, it does not last forever. Cracks in bridges, roads, and other structures are dangerous, but replacing them outright is not an option due to high costs, environmental impact, and lengthy process. Instead, these structures must be repaired and reinforced.
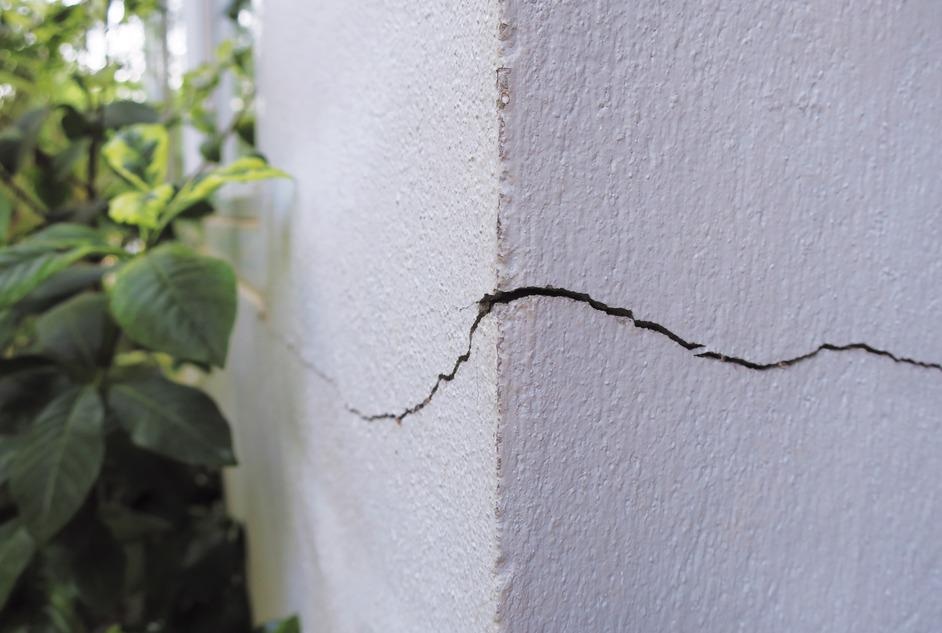
Image Credit: TA BLUE Capture/Shutterstock.com
Utilizing metal was once an option. However, its susceptibility to damage through rusting and exposure to external elements has limited its use. For decades, concrete structures have been reinforced with carbon-fiber-reinforced polymers (CFRP), a material laced carbon fibers to impart extra strength.
Expanding on previous work, researchers from Empa, the Swiss Federal Laboratories for Materials Science and Technology, have developed a new method using a CFRP variant to reinforce structures further.
Covering the Cracks
Concrete is the most commonly used artificial material on Earth; it is a composite material consisting of Portland cement, water, and an aggregate, such as sand, gravel, or rock. When mixed, it becomes a workable paste that hardens as it dries. It is cheap, long-lasting, and requires little maintenance, but it has a low strength-to-weight ratio, and over time, cracks can appear.
Carbon-fiber-reinforced polymers (CFRP) have been used for a long time to restore supporting structures that are struggling to carry their load. Bridges built between the mid-1960s to 1980s, for example, were designed with significantly less traffic in mind compared with today.
Flat lamellas that have been bonded to the underside of structures can counteract the increasing load. A lamella is a structural element that combines in a two-way spanning grid system; such a pattern allows for a large and complex structure from short, geometrically simple components. These grids make it possible to repair, rather than replace, structures.
Improving the Method
EBROG is a method first used to refurbish a bridge in Küssnacht in 2018. Narrow grooves are milled longitudinally on a concrete girder, for instance, before reinforcements – the lamellae - are externally glued to the area. The channels serve to increase the surface area for force transmission and penetrate deeper into the concrete.
Empa researchers are developing this method by testing prestressed CFRP laminate lamella, which actively reinforces concrete beams. Under tensile stress, they are bonded with epoxy resin. Once the bond has hardened, the ends, which are under enormous tensile forces, are relaxed.
To stop the ends from tearing off, they must be securely fastened, typically with aluminum plates glued and secured with dowels. The Empa team has replaced this with a U-shaped CFRP stirrup, which allows for a more precisely defined transmission of forces. As it is metal-free, it is not susceptible to the elements.
A solution made of a single material is always better than two that behave differently, especially for the anchoring, we performed a lot of tests in the lab.
Christoph Czaderski, Study Lead, Engineering Structures Lab, Empa
The team profited from the experience of the Isfahan University of Technology in Iran, where Czaderski acknowledges a lot of basic research occurred. Postdoctoral fellow, Niloufar Moshiri, came to Empa with the idea of combining the EBROG process with prestressing, he explains.
Bringing the Technology to Market
Laboratory testing suggests the potential is huge. Prestressing and the CFRP stirrups increased the load-bearing capacity of a concrete slab by 77% compared with classic reinforcement methods. There was still a difference of 34% even without prestressing. However, further testing is required; large-scale assessments will be performed on concrete slabs spanning 6 m to see precisely how the method will perform in an actual restoration project before the technology can be bought to market.
Industry partner, S&P Clever Reinforcement Company, is already working on the practical aspects, developing an industrial process for creating the U-shaped stirrups, which were previously formed by hand from carbon profiles. The equipment used to prestress the lamellas will also have to be redesigned.
The technology could be applied to any structure that requires repairing, from bridges to residential renovations, saving costs and cutting carbon dioxide emissions caused by other processes. It is also easier, faster, and reasonably priced for building owners.
I absolutely see a market for this, and with prestressing, you're only really exploiting the full potential of the material.
Martin Hüppi, Project Leader, S&P Clever Reinforcement Company
References and Further Reading
Empa. (2021) Prestressed plasters for old buildings. [online] Available at: https://www.empa.ch/web/s604/eq72-bruecken [Accessed 23rd August 2021].
Xylotek - Advanced timber structures. (2021) Lamella Structures - Xylotek - Advanced timber structures. [online] Available at: https://www.xylotek.co.uk/lamella-structures/ [Accessed 23rd August 2021].
Designingbuildings.co.uk. (2021) Concrete. [online] Available at: https://www.designingbuildings.co.uk/wiki/Concrete [Accessed 23rd August 2021].
Disclaimer: The views expressed here are those of the author expressed in their private capacity and do not necessarily represent the views of AZoM.com Limited T/A AZoNetwork the owner and operator of this website. This disclaimer forms part of the Terms and conditions of use of this website.