The most widely used and researched method of fabricating nanofibers is electrospinning (ES), due to its high efficiency, adaptability and cost-effectiveness.
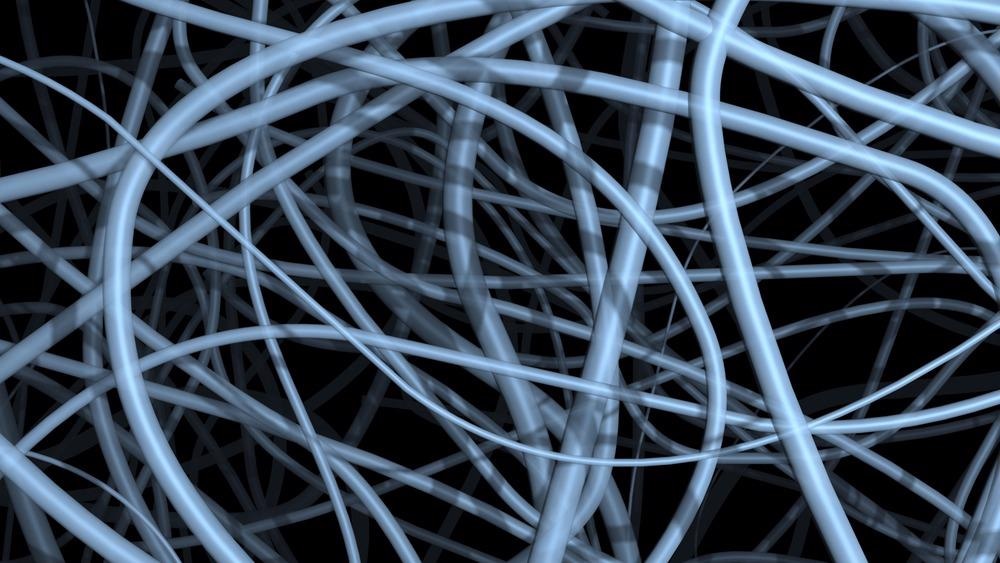
Image Credit: vrx/Shutterstock.com
Nanofibers are fibrous structures with nanoscale cross-sectional diameters (1-100nm) primarily made from polymers. Compared to conventional fibrous structures, they are lightweight with an exceptionally high surface-area-to-volume ratio. Their ability to form a highly porous and interconnected mesh has made them the focus of extensive research for a wide range of applications. Central to such research has been their method of fabrication. This includes drawing, phase separation and template synthesis.
The concept behind ES was first seen in the 17th century when William Gilbert observed the deformation and drawing of a spherical water droplet into a cone (now known as the Taylor cone) when under the influence of an electric field. This concept was developed to form the typical ES apparatus.
With sufficient voltage and thus electric field strength, the induced charges on the free surface of the Taylor cone at the tip of the needle (known as the spinneret) can overcome the surface tension. A charged jet is then initiated from the vertex of the cone and propelled towards the grounded collector, during which, rapid solvent evaporation results in the deposition of dry nanofibers and the creation of a nonwoven mat.
The morphology of the resulting nanofibers is controlled by the solution properties (viscoelasticity, surface tension, solvent volatility, conductivity), environmental conditions (humidity, temperature) and process parameters (applied voltage, needle-collector distance, flow rate).
Electrospun Nanofibers for Effective Skin Burn Treatment
Through the careful control of all these parameters, this method has found its application in various fields such as healthcare and biomedical engineering, water treatment and environmental remediation, and energy generation and storage. In the biomedical field, for example, electrospun biodegradable nanofibers can mimic the native extracellular matrix and provide suitable mechanical support, topographical guidance and biochemical instructions to surrounding cells and thus act as scaffolding material to promote tissue regeneration.
Despite the popularity and successful application of traditional ES in many fields, limitations in the method remain. These include the difficultly of creating a highly regulated structure with the desired fibre alignment and orientation, needle clogging due to solution gelation, and critically, a low process throughput (<0.1 g/h).
Various developments of the traditional method have been established in response but have thus far had only rectified such limitations individually. For example, multi-needle methods have increased throughput (<3.6 g/h) but still suffer from needle clogging and introduce significant inhomogeneity in the nanofiber mat due to interference of electric fields from the needles.
Needleless electrospinning (NLES) utilizes external forces (through magnetic fields, ultrasound or high-pressure gas flow) to prompt spike formations directly on the free surface of the polymer solution, which in turn initiates the ES process when under an electric field. This drastically increases throughput and negates needle clogging but requires a large voltage and results in inconsistent nanofiber morphology due to the multivariate nature of the process and unpredictable location of the spikes and thus Taylor cones.
Earlier this year, Xiong et al. (2021) proposed a variant of the ES method that combines the high throughput of NLES with the greater fibre control of the traditional method. By using a metal bowl-shaped base with a mushroom-shaped PTFE cover, an axisymmetric electric field is formed about the centre of the spinneret with peak intensity localized along the rim of the bowl.
Electrospinning of Polyvinylpyrrolidone (PVP) | Electrospun Nanofibers
Video Credit: Spruce Science/Youtube.com
This results in the equidistant formation of Taylor cones along the rim and thus the predictability of multi-needle ES jets without the electric field interference. Furthermore, concentrating the electric field in the desired location facilitates a lower applied voltage than the equivalent NLES apparatus whilst maintaining the characteristic high throughput (13.7 g/h).
The method appears similarly promising on analysis of the nanofibers themselves; the coefficient of variation of fibre diameters was seen to be consistently low (~10%) throughout the range of average fibre diameters achieved (125-250nm). This is significantly lower than that commonly seen for conventional NLES methods (>20%) and represents a far superior and consistent material quality.
The practical implications of this novel method are most notable in applications requiring high-throughput and high-quality nanofiber fabrication, which currently reside in the healthcare and biomedical field. Partheniadis et al. (2020) specifically highlighted the previous incompatibility of these two fabrication characteristics as preventing the widespread commercialization of nanofibers in this field.
The method may also introduce nanofibers into developing new fields, such as providing an edible matrix scaffold for cultured meat to bind to and give added flavour and texture, an application previously precluded due to nanofiber fabrication scaling issues.
However, limitations of the method remain; despite the high homogeneity of the nanofiber structure, fibre alignment and orientation remain relatively uncontrollable characteristics. Furthermore, evaporation of the highly volatile solvents from the free surface alters the concentration of the polymer solution during fabrication and could potentially result in a decreasing process accuracy and reproducibility.
Future research directions for this method will address such limitations and will likely be undertaken with a greater urgency due to the commercial realisation displayed by the study by Xiong et al. (2021).
References and Further Reading:
Niu, H., Zhou, H. and Wang, H., 2019. Electrospinning: an advanced nanofiber production technology. Bristol: IOP Publishing, pp.1-44.
Zhang, C., Li, Y., Wang, P. and Zhang, H., 2020. Electrospinning of nanofibers: Potentials and perspectives for active food packaging. Comprehensive Reviews in Food Science and Food Safety, 19(2), pp.479-502. https://ift.onlinelibrary.wiley.com/doi/full/10.1111/1541-4337.12536
Xue, J., Wu, T., Dai, Y. and Xia, Y., 2019. Electrospinning and Electrospun Nanofibers: Methods, Materials, and Applications. Chemical Reviews, 119(8), pp.5298-5415. https://pubs.acs.org/doi/abs/10.1021/acs.chemrev.8b00593
Xiong, J., Liu, Y., Li, A., Wei, L., Wang, L., Qin, X. and Yu, J., 2021. Mass production of high-quality nanofibers via constructing pre-Taylor cones with high curvature on needleless electrospinning. Materials & Design, 197, p.109247. https://www.sciencedirect.com/science/article/pii/S0264127520307826
Partheniadis, I., Nikolakakis, I., Laidmäe, I. and Heinämäki, J., 2020. A Mini-Review: Needleless Electrospinning of Nanofibers for Pharmaceutical and Biomedical Applications. Processes, 8(6), p.673. https://www.mdpi.com/2227-9717/8/6/673
Watson, E., 2021. Cell-cultured meat gamechanger? Matrix Meats to showcase nanofiber scaffolding in 'solid meat product' this year. [online] foodnavigator-usa.com. Available at: <https://www.foodnavigator-usa.com/Article/2020/08/10/Cell-cultured-meat-gamechanger-Matrix-Meats-to-showcase-nanofiber-scaffolding-in-solid-meat-product-this-year> [Accessed 7 November 2021].
Disclaimer: The views expressed here are those of the author expressed in their private capacity and do not necessarily represent the views of AZoM.com Limited T/A AZoNetwork the owner and operator of this website. This disclaimer forms part of the Terms and conditions of use of this website.