Polymers are defined as materials consisting of macromolecules that are made up of small, regularly repeating smaller subunits. The coextrusion process is a manufacturing process that uses different layers of polymers to produce finished products with improved properties.
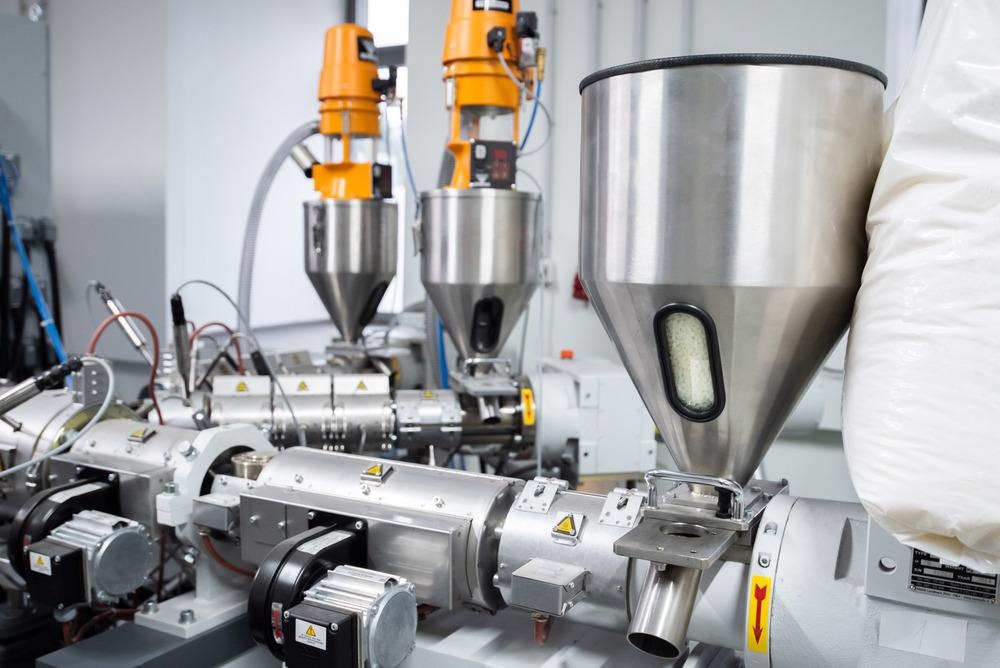
Image Credit: Forance/Shutterstock.com
The coextrusion process involves the simultaneous flow of different polymers with different characteristics within the same equipment to produce a multilayer product. The aim is to combine the properties of the constituent polymers in a single product while maintaining good adhesion between the layers. It is also possible to use a recycled polymer between two layers of the same virgin polymer to reduce the product price.
In recent years, the coextrusion process has seen rapid growth in the field of packaging. The main reason for development is the ability of the technology to produce products with multiple layers of polymers. In some cases, the number of layers of polymers may increase up to 10, which results in an improvement in product utility.
These coextruded polymers pose environmental problems due to the difficulty of separating the constituent polymers at the recycling stage. Yet, the process is widely used for packaging because it is impossible to develop the properties produced by polymer coextrusion using a single polymer material. The recycling of coextruded polymers is also a complicated process due to changes in the properties of polymers during the various recycling process.
Polymer Coextrusion Dies
Tri-layer film blowing die is used to coextrude three types of polymers. The die can also be used with a higher number of polymers, depending upon the industrial requirements. During its use, multilayer flow occurs at the terminal area of the lips of the die at a very short distance. The main disadvantage of this die is that it is very complex and expensive, but the advantage is that it can be optimized for various types of polymers. Additionally, it provides a good distribution of polymer layers at different thicknesses.
The conventional flat die preceded by a feed-block is commonly used for the polymer coextrusion process in the industry. During the coextrusion process with the conventional flat die, polymers are brought in contact before entering the die, making the process less complicated. It usually consists of a zone with various lamellas whose geometry can be changed based on the engineering requirements. The main advantage of this die is that it is less costly and provides higher flexibility, but the major limitation is that process control using this die is difficult.
The die used for cable or tube coating polymer coextrusion is called a coat hanger die. During the coextrusion process using this die, the polymer materials wound around the die mandrel in which the inner tube layer is flowing, which produces accurate cables and tubes. It must be noted that it is essential to control the distribution of the polymer during the extrusion process to provide uniform thickness to the finished product.
Defects During Polymer Coextrusion
Defect development is one of the critical issues encountered during the coextrusion process. Three common defects developed during the process are adhesion defect, interfacial instabilities, and progressive encapsulation.
During coextrusion, glue is added between the two incompatible polymers for adhesion. Due to conditions such as extrusion speed, temperature, and pressure, adhesion may fail at certain places, causing adhesion defects. Additionally, it is also caused due to selection of inappropriate process parameters for the coextrusion process.
Interfacial instabilities can occur at the interface between two adjacent layers of polymers. These flaws are especially noticeable when producing coextruded films with very thin tie-layers between the main polymer streams. The defect may result in decreased adhesion and poor mechanical properties. Additionally, in certain cases, defects also result in localized stress development, which causes failure during application.
Recent Studies
In a recent paper published in the journal Polymers, researchers reviewed various types of interfacial phenomena during the polymer coextrusion process. According to the authors, interfacial diffusion, interfacial reaction, interfacial instability, and interfacial confinements are critical for producing high-quality polymer products through the coextrusion process.
In another study published in the journal Polymers, researchers studied layer adhesion during the polymer coextrusion process by changing the operating temperature and the flow rate. The study helped to find the parameters due to which the layer adhesion is negatively affected and the limits under which the layer adhesion is optimum. It must be noted that the study was performed only for specific types of polymers and under laboratory conditions.
More from AZoM: What is Cryo-Electron Microscopy?
References and Further Reading
Agassant, J.-F.; Demay, Y. Investigation of the Polymer Coextrusion Process: A Review. Polymers 2022, 14, 1309. https://www.mdpi.com/2073-4360/14/7/1309
Lu, B.; Zhang, H.; Maazouz, A.; Lamnawar, K. Interfacial Phenomena in Multi-Micro-/Nanolayered Polymer Coextrusion: A Review of Fundamental and Engineering Aspects. Polymers 2021, 13, 417. https://www.mdpi.com/2073-4360/13/3/417
Rathner, R.; Leimhofer, C.; Roland, W.; Hammer, A.; Löw-Baselli, B.; Steinbichler, G.; Hild, S. Improving Layer Adhesion of Co-Extruded Polymer Sheets by Inducing Interfacial Flow Instabilities. Polymers 2022, 14, 587. https://www.mdpi.com/2073-4360/14/3/587
Disclaimer: The views expressed here are those of the author expressed in their private capacity and do not necessarily represent the views of AZoM.com Limited T/A AZoNetwork the owner and operator of this website. This disclaimer forms part of the Terms and conditions of use of this website.