This article discusses the role of rapid thermal processing (RTP) in the semiconductor manufacturing process.
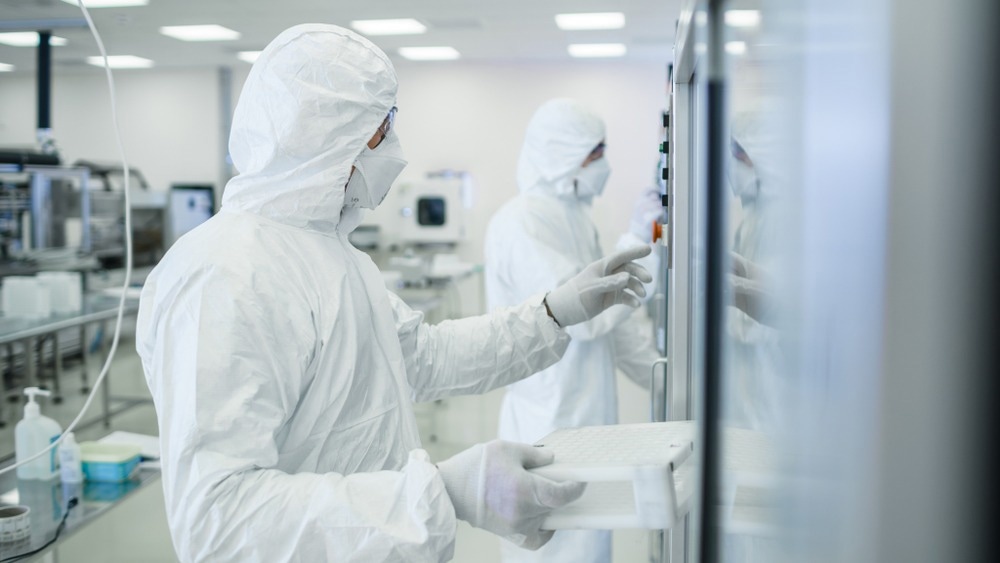
Image Credit: Gorodenkoff/Shutterstock.com
What is RTP?
RTP is a semiconductor manufacturing technique in which silicon wafers are heated at temperatures above 1000 oC using lasers or high-intensity lamps for a few seconds. During the cooling of the wafers, the wafer temperatures are reduced in a gradual manner to prevent wafer breakage and dislocations due to thermal shock.
RTP is more efficient than conventional furnace annealing as it produces superior silicides and oxides and reduces the thermal budget/integral of temperature and time. Other advantages of RTP include lower manufacturing cost, ease of process development, high throughput, and process uniformity.
An RTP system is typically used to process silicon wafers to fabricate semiconductors for high-speed computing applications and computing devices. Single wafer processing produces the best uniformity, specifically for large wafer sizes.
RTP systems perform thermal-related fabrication steps, such as chemical vapor deposition, thin dielectric film formation, and annealing. Annealing is used to add impurities to the semiconductor through thermally-activated diffusion.
Importance of Effective RTP Systems in Semiconductor Manufacturing
Near-uniform temperature distribution must be maintained over the wafer during both transient and steady-state situations of the annealing process to obtain uniform resistivity and conductivity throughout the wafer. Moreover, the uniform temperature distribution must be achieved for different operating conditions, including different gases, pressures, and processing temperatures.
An RTP system must be able to change the spatial energy flux distribution radiating to the wafer to maintain temperature uniformity in different processing conditions as the necessities for wafer temperature uniformity vary as a function of operating conditions.
An RTP system with several concentric circular rings of lamps that are controlled independently, such as the Stanford rapid thermal multiprocessor (RTM), can be used to meet this requirement.
In the Stanford RTM, an automatic control strategy is used to control the power to each of the three lamp zones to achieve uniform temperature over the wafer at both transient and steady-state conditions. The control strategy uses a multi-point sensor reading to provide temperature distribution measurement in real-time.
In a paper published in SPIE Proceedings of Rapid Thermal and Integrated Processing, researchers derived a first-principles low-order model of RTP of semiconductor wafers and experimentally verified the model at one torr pressure and a range of operating temperatures from 400 oC to 900 oC in an inert nitrogen environment.
Researchers also developed an automatic multivariable controller for multi-point sensor and multi-zone lamp RTP systems and applied it to the RTM. In the real-time multivariable controller, a feedforward mechanism was used to predict the temperature transients and a feedback mechanism was utilized to correct the errors in the prediction.
Ease of implementation and identification of predictive applications in temperature control and signal processing in real-time was the major advantage of the low-order model over the detailed model. The nonlinear effects of temperature were demonstrated to validate the model.
The controller was applied successfully to achieve a ramp from 20 oC to 900 oC at 45 oC/second with less than 15 oC nonuniformity during the ramp and less than 1 oC average nonuniformity during the hold at 900 oC for five min.
Controller performance was satisfactory in presence of several challenges, including system nonlinearities, sensor noise, saturating actuators, slow disturbances, and substantial time delays. Thus, the findings demonstrated that the automatic multivariable controller can help in achieving wafer temperature uniformity over different processing conditions in an RTP system.
In another study published in the Mathematics-in-Industry Case Studies Journal, researchers derived a model of radiative heat transfer that occurs in an axially symmetric RTP chamber using the theory of shape factors and used the model to predict the influence of chamber materials and geometry on the silicon wafer temperature uniformity.
A series of numerical experiments were performed to predict the effects of the reflectivity and size of the showerhead, chamber height, and guard ring on the temperature uniformity over the wafer.
The results displayed an improvement in the wafer temperature uniformity when the radius of the showerhead was the same or larger than that of the outer radius of the guard ring. However, the chamber size must be less than 300 mm in diameter to ensure that the showerhead radius is below the chamber radius.
Similarly, the temperature uniformity over the wafer increased with the increasing radius of the guard ring, indicating the effectiveness of the larger rings in achieving uniform temperature. However, the guard rings must be less than 2.5 cm in width for practical purposes as larger rings require more power to remain hot, making the process expensive.
Lower reflectivity led to a more uniform temperature over the wafer. However, some reflectivity was useful to minimize the amount of power required from the lamp to attain peak temperatures. The best temperature uniformity was achieved in the smallest chamber height.
Optimal control of rapid thermal annealing (RTA) is used to fabricate ultra-shallow junctions required in microelectronic devices. In a study published in the Journal of Process Control, researchers designed a spike anneal program that can optimize the junction depth by constraining the sheet resistance.
The study demonstrated that the optimal RTA program can minimize the transient enhanced diffusion (TED) while achieving the desired sheet resistance consisting of fast linear cooling and heating profiles.
The model-based optimal control directly computed the maximum annealing temperature and avoided the commonly used heuristics and trial-and-error approach, which reduced the cost to identify the optimal annealing program and the number of experimentations.
Observations from the worst-case analysis on the optimal junction depth indicated the need to improve the existing RTA controllers and metrology to minimize the control implementation inaccuracies.
Limitations of RTP
Nonthermal-equilibrium conditions in RTP make modeling and predicting difficult, while the absolute temperatures remain unknown. Moreover, uniform heating is extremely critical in RTP compared to traditional furnace processing due to the high ramp rates that lead to stress.
Recent Studies Involving RTP
In a study published in the journal Advanced Functional Materials, researchers demonstrated a new method to fabricate kusachiite (CuBi2O4) photoelectrodes with enhanced photo-electrochemical stability and charge separation.
Dibismuth trioxide (Bi2O3) and copper oxide (CuO) layers were sequentially deposited on fluorine-doped tin oxide (FTO) substrates using pulsed laser deposition (PLD), followed by RTP for 10 min at 650 oC to obtain highly crystalline, phase-pure CuBi2O4 films.
The combined PLD and RTP approach enabled excellent Bi:Cu stoichiometry control, resulting in the synthesis of CuBi2O4 photoelectrodes with superior electronic properties compared to the photoelectrodes obtained through spray pyrolysis.
The synthesized uncoated CuBi2O4 photoelectrodes displayed only a 26% reduction in photocurrent after five h, which represented the highest stability of this material reported until now. The findings demonstrated that the RTP/PLD fabrication approach offered new possibilities to fabricate highly-crystalline complex metal oxide photoelectrodes with good electronic properties at higher temperatures.
To summarize, RTP has become indispensable in semiconductor manufacturing as it satisfies both production and device requirements, and the technique will contribute to future advances in microelectronic technologies.
More from AZoM: What is Glow Discharge Optical Emission Spectrometry
References and Further Reading
Saraswat, K., Kailath, T., Franklin, G., Boyd, S., Balemi, S., Hoffmann, G., Gyugyi, P., Norman, S., Park, P., Cho, Y., Schaper, C. (1991). Modeling and Control of Rapid Thermal Processing. SPIE Proceedings of Rapid Thermal and Integrated Processing. DOI: 10.1117/12.56658. https://www.researchgate.net/publication/234065612_Modeling_and_Control_of_Rapid_Thermal_Processing
Wacher, A., Seymour, B. R. (2011). A Radiation Model of a Rapid Thermal Processing System. Mathematics in Industry Case Studies Journal, 3, 1-18. http://www.fields.utoronto.ca/journalarchive/mics/35-32.pdf
Gunawan, R., Jung, M.Y.L., Seebauer, E. G., Braatz, R. D. (2004) Optimal control of rapid thermal annealing in a semiconductor process. Journal of Process Control, 14, 4, 423-430. https://doi.org/10.1016/j.jprocont.2003.07.005
Rapid Thermal Processing. [Online]. https://alan.ece.gatech.edu/ECE6450/Lectures/ECE6450L6-Rapid%20Thermal%20Processing.pdf (Accessed on 26 June 2022)
Gottesman, R., Song, A., Levine, I., Krause, M., Islam, A. T. M. N., Abou-Ras, D., Dittrich, T., van de Krol, R., Chemseddine, A. (2020). Pure CuBi2O4 Photoelectrodes with Increased Stability by Rapid Thermal Processing of Bi2O3/CuO Grown by Pulsed Laser Deposition. Advanced Functional Materials. https://doi.org/10.1002/adfm.201910832
Disclaimer: The views expressed here are those of the author expressed in their private capacity and do not necessarily represent the views of AZoM.com Limited T/A AZoNetwork the owner and operator of this website. This disclaimer forms part of the Terms and conditions of use of this website.