In this interview, Jamie Clayton, Operations Director at Freeman Technology, talks to AZoMaterials about the importance of powder testing for additive manufacturing.
What is the importance of powder testing for additive manufacturing (AM)?
The ability to relevantly test AM powder feedstocks directly supports key industry challenges such as effective supply chain management, process optimisation, new feedstock development, and powder recycling/re-use. What we mean by relevant testing is generating results that correlate with in-process performance and/or print quality reliably and sensitively. Test results that enable the prediction of powder performance for a specific application. The alternative is excessive dependence on print trials, a ‘print and see’ approach. But this is time-consuming, expensive, and, for new materials often not feasible.
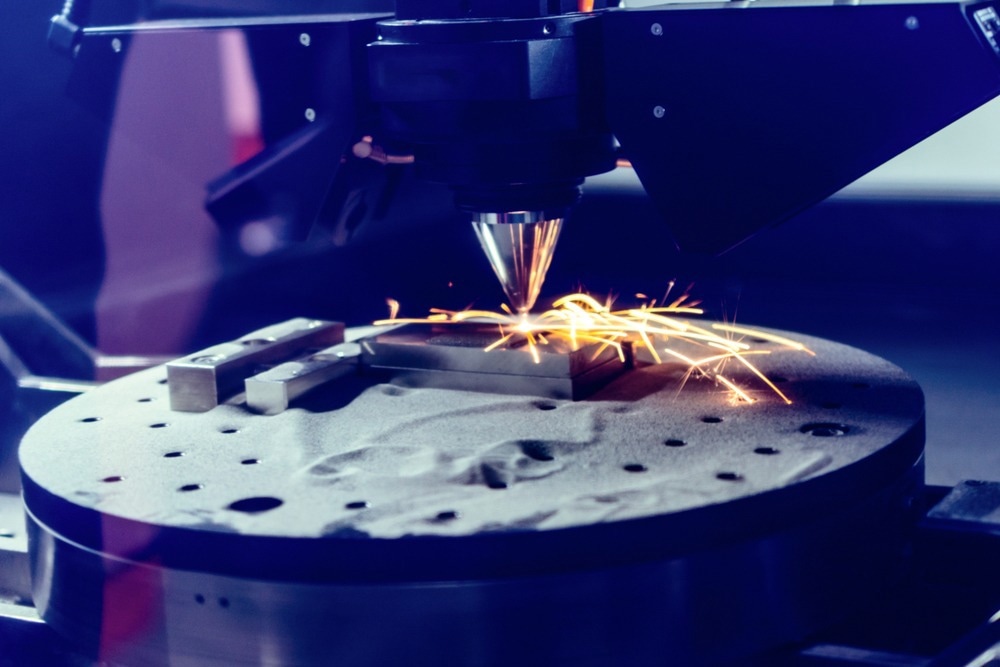
Image Credit: ShutterStock/Nordroden
Because of the industrial significance of powder-based AM processes such as binder jetting and powder bed fusion, AM processors have long recognised this need for effective powder characterisation. Pioneers have invested heavily in developing appropriate specifications, following a trajectory that mirrors progress in other powder processing industries. The earliest specifications centered solely on particle properties, but bulk powder properties were added soon after.
Particle properties such as size and morphology are relevant and easy to measure but in isolation, they are rarely sufficient to differentiate fresh AM feedstocks and/or the impact of recycling. AM processes are exacting in terms of flowability, spreadability, packing behaviour, response to heat, and of course, chemistry. Leaving chemistry aside these behaviours can be related to particle size and morphology, a classic example being that larger, more spherical powders tend to flow more easily than finer, irregular analogues but not to the extent that we can predict bulk powder behaviours from assessing particle properties. Measurement is the pragmatic alternative. With appropriate powder testing, we can relevantly quantify defining bulk powder behaviours and use them to help predict both printability and print quality.
Are we able to predict printability from powder properties? And if so, how?
Printability is a crucial first hurdle for any fresh or recycled AM powder. By printability, we mean ease of processing. We’re looking to answer the question - can I print with this, at an acceptable rate, and without frequent printer blockages?
For some, this issue is synonymous with just one powder behaviour – spreadability. In both binder jetting and powder bed fusion, the spreading of powders to uniform layers just tens of microns thick is a critical step. A focus on spreadability is therefore warranted. However, in these processes, powders must also dispense freely from feed hoppers, prior to spreading, and pack efficiently and rapidly into uniform layers, to realise high throughput printing. Focusing on spreadability to the exclusion of all other properties is therefore inadvisable.
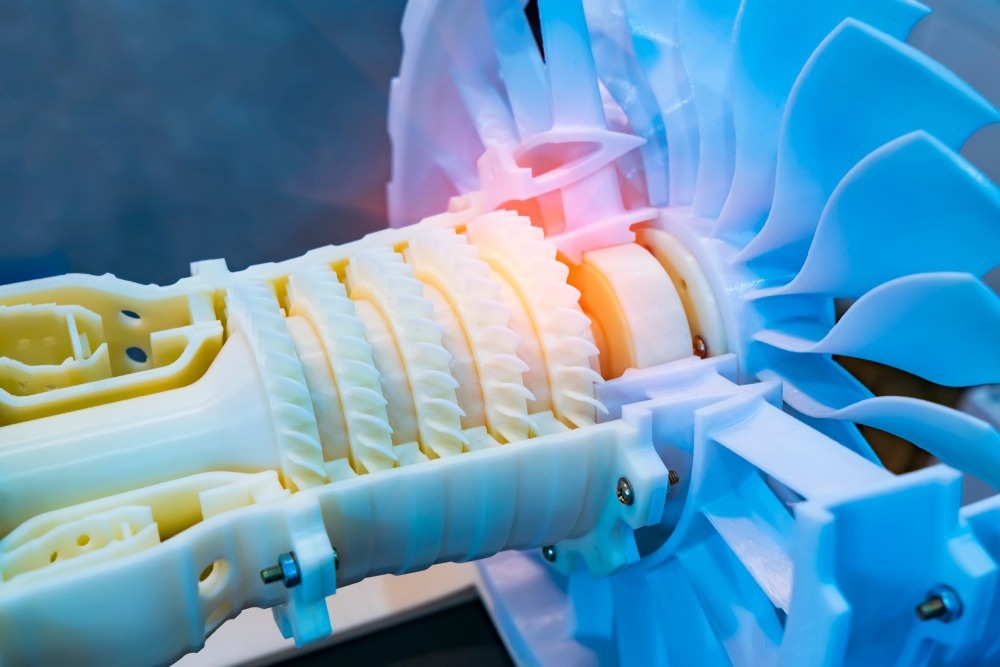
Image Credit: ShutterStock/asharkyu
There is also a tendency to use the terms flowability and spreadability interchangeably. There are many ways of measuring flowability, and spreadability and flowability are related, but they are different behaviours, a free-flowing powder will not necessarily spread easily under forcing conditions, as maybe applied by a recoater. Critically assessing claims of relevance when assessing alternative measures of powder flowability is crucial.
Against this backdrop, I’d highlight promising work on the use of AM Suitability (AMS) to predict printability.
Researchers at the Ecole de Technologie Superieure1 compared the performance of three commercial supplies of Ti-6Al-4V in a laser powder bed fusion printer. These supplies were carefully selected to enable independent investigation of the impact of particle size and shape. Bulk powder measurements were then carried out using the FT4 Powder Rheometer® to gain a more relevant understanding of the impact of size and shape, and to see whether the print performance could be predicted. Seven bulk powder properties were identified as relevant: Basic Flowability Energy (BFE), Specific Energy, and Aerated Energy, which are all dynamic powder properties, Compressibility, Permeability, bulk density, and Cohesion, a shear property. Normalised values of all these parameters were combined into an AMS factor which was then used to rank the performance of the three powders. Print trials confirmed the validity of this ranking with lower AMS values securely associated with powders with better processability. More specifically with powders with lower AMS values, it was possible to print with deeper layers, increasing potential throughput.
This approach of using an AMS factor was subsequently adopted by researchers from Oerlikon to assess the processability of blends for in situ alloying in a laser powder bed fusion process2. This group also concluded that an AMS factor could provide ‘a reliable indicator of processability’ adding weight to the concept of combining multiple relevant properties for robust assessment. There is close parity between these studies with respect to the parameters selected to define an AMS factor though the exact parameters vary. A key point to note though is that dynamic, shear, and bulk properties were included in each case, highlighting the potential value of the FT4 Powder Rheometer which combines all the required capabilities.
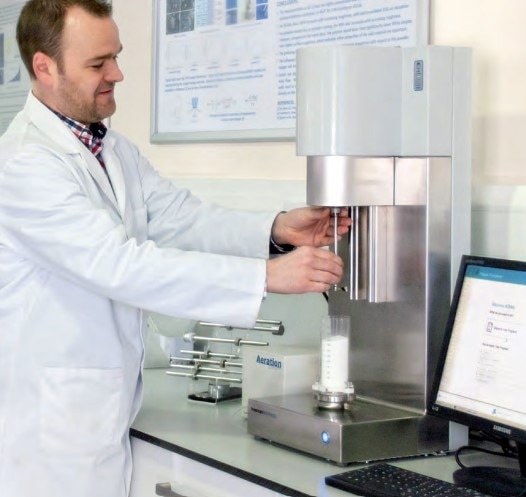
FT4 Powder Rheometer
Image Credit: Freeman Technology
In summary, I would suggest that we can predict printability with a reasonable degree of success providing that we use an appropriate collection of properties that capture all relevant behaviours. Combining dynamic, bulk, and shear properties has proven successful in this regard though there remains room to refine the approach for different applications and processes, potentially via the unequal weighting of different parameters.
Are we able to predict print quality from powder properties? Can you point to good examples of success?
Beyond the question of whether it will be possible to print with a specific powder lies the bigger issue of how to control print quality, and how to manipulate the properties of the printed component. We’re moving towards being able to predict print quality but it’s harder than predicting printability and multi-faceted powder testing is certainly required.
In powder AM uniform layer deposition is the foundation of good print quality, creating a direct link between processability and print quality. However, there is also potential for bulk powder properties to influence the processes that follow deposition. For example, sintering and melting behaviour is influenced by heat transfer through the bed while with binder jetting there is the analogous issue of binder penetration. Typically, the goal is to produce components with a desirable mechanical property portfolio - often including high strength - to exacting tolerances. Relating these goals back to earlier discussions of relevant powder properties highlights the importance of particle packing behaviour as quantified by bulk parameters such as density, permeability, and compressibility. Efficient packing minimises air pockets in the bed, and by extension, the risk of fusion defects in the finished product but at the same time improves heat transfer efficiency, potentially making it harder to apply heat with precision to achieve good dimensional accuracy.
Though this additional layer of complexity makes predicting print quality difficult, there is growing evidence of success.
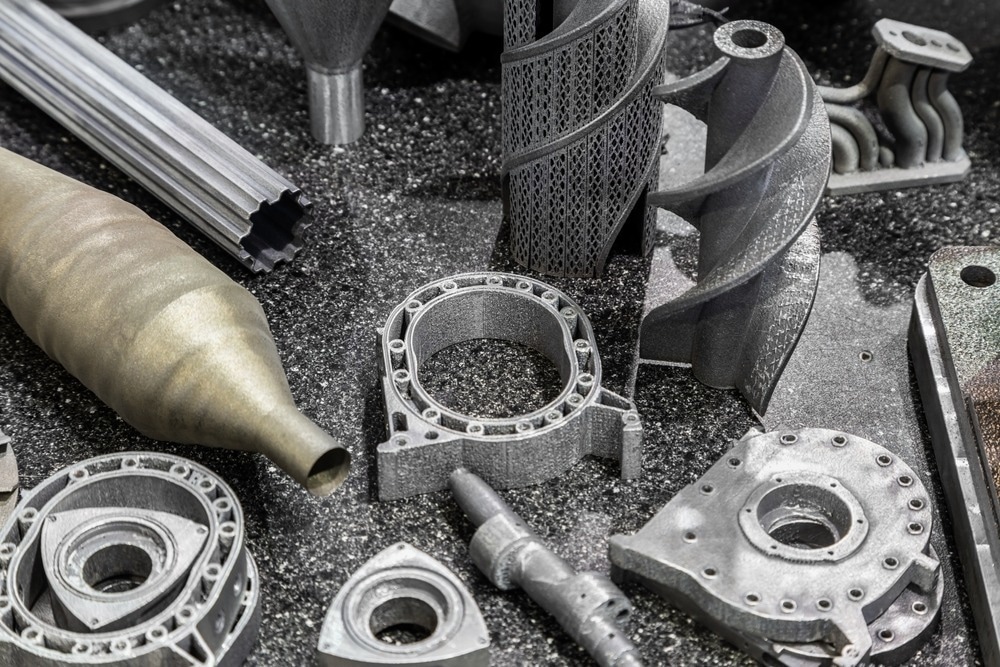
Image Credit: ShutterStock/OlegDoroshin
For example, lower AMS factors have been securely linked with superior print properties as well as printability underlining the merits of this approach1. Multi-faceted testing is also used to establish a specification for Inconel powders for laser metal deposition applications in the aerospace industry3. Here, a recommendation was to add the dynamic flow property BFE to an existing specification based on particle size and Hall Flow Index to support the robust selection of powder feedstocks capable of delivering the required print quality. Switching to polymers, specifically polyamide, a study by researchers at DeMontfort University4 showed a strong correlation between BFE and mechanical properties such as tensile strength and surface hardness in a selective laser sintering trial. At the same time, an inverse relationship between dimensional accuracy/consistency and particle packing metrics highlights the need to evaluate and optimise multiple powder properties to achieve print quality targets.
Is the industry maximising its use of powder testing yet?
The industry as a whole is probably not yet extracting as much value from powder testing as it might but there is certainly an appetite to change and some really good practice to point to by those leading the way.
For example, ExOne, a global leader in binder jetting has had robust metal powder specifications for printability in place for several years now. They’ve used the FT4 Powder Rheometer to develop specifications that include dynamic (Stability Index and Flow Rate Index), shear (Cohesion and Wall Friction Angle), and bulk powder properties (Permeability and Compressibility). Using them the company can assess printability prior to a trial, for an alternative feedstock, a customer material, or a feedstock in development. This accelerates progress and is particularly helpful when a material is in short supply.
We’ve also recently heard from experts at Evonik who similarly use the FT4 to characterise polymeric powders being optimised for 3D printing. They cite savings of around two months of printer time in the development of a new polymer powder due to the ability to narrow down a field of as many as 500 formulations on the basis of powder testing. This is a significant saving, not only with respect to time but also from the viewpoint of reducing waste, an increasingly important goal.
Companies such as these that invest in establishing robust specifications have a real advantage when it comes to speed of feedstock and process optimisation for a specific application, and also when establishing reliable supply chains. The ability to differentiate alternative supplies sensitively and relevantly is crucial when it comes to identifying the most cost-effective option.
Any tips or predictions for powder testing within AM?
Going forward it seems likely that powder testing in AM will become more standardised. I’m convinced that multi-faceted testing and specification are here to stay because of the success already demonstrated and because it seems intuitively sensible. Capturing the sophisticated behaviour we expect of powders for AM with just one or two metrics, or indeed with low sensitivity metrics is not realistic. My view is that techniques and properties will gradually earn a place in specifications on the basis of consensus and weight of evidence of success. Our understanding of key behaviours such as spreadability has improved considerably over recent years but it may be that, ultimately, we have dedicated tools for the industry for very specific behaviours such as this. The value of more secure prediction would certainly warrant it as the industry continues to grow.
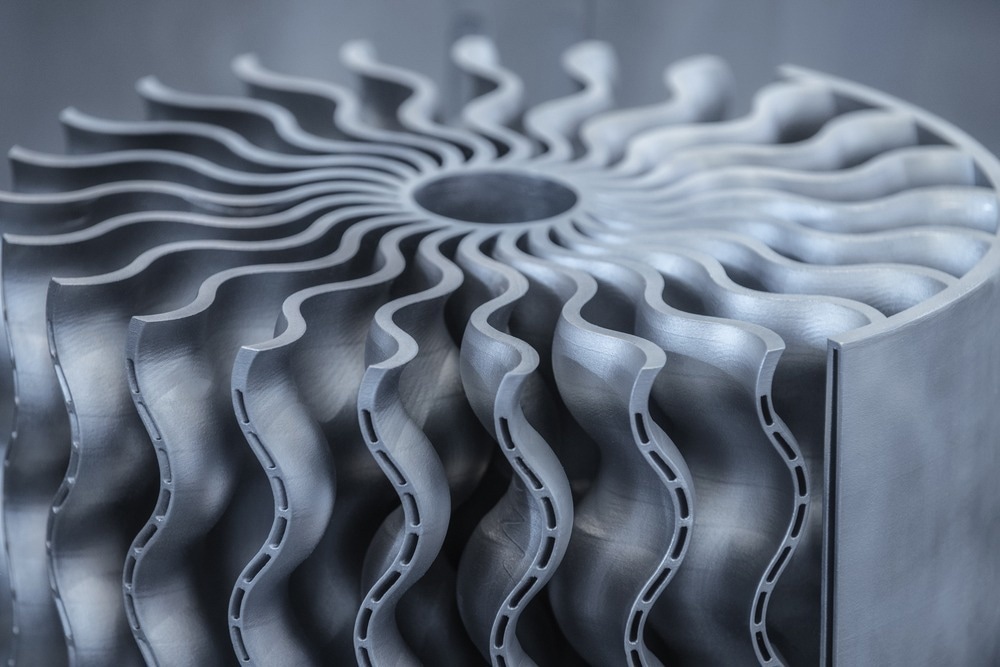
Image Credit: ShutterStock/Sergii Chernov
I’d advise anyone working in AM looking to instigate powder testing to look for clear proof that a method measures properties that correlate with performance metrics. For me the best studies are those where the influence of powder properties tracks right through to parameters of real, economic importance – the ability to detect a powder that will block the printer, before it goes in, to increase throughput by working with thicker layers, to reduce the surface roughness of a finished component or to increase its tensile strength. In contrast, simplistic trials suggesting correlations between, for example, a flowability metric and an ill-defined measure of ‘spreadability’ are still too common and substantially less compelling.
And finally, I’d say, don’t underestimate the value of relevant powder testing. The ability to choose a feedstock quickly and reliably, or to optimise a recycling strategy, without endless print trials, can deliver substantial economic gain and significantly improve competitiveness in this fascinating, still evolving industry.
Further reading
- Download Powder Flow testing for Additive Manufacturing for a deep dive into this topic including plenty of case study data or for more information on AMS factors read our app note.
- A write-up of a round table discussion with experts from Evonik on the topic of powder testing is available here.
About Jamie Clayton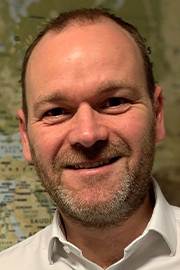
Jamie Clayton is Operations Director at powder characterisation company Freeman Technology, based at the company’s headquarters in Tewkesbury, UK. He graduated from the University of Sheffield with a degree in Control Engineering and is responsible for the overall management of company activities, including the R&D, production, sales, and customer support teams.
During his time with the company, Jamie has worked as a mentor with several academic groups and is an active member of ASTM F42. Jamie is also a regular contributor to conferences and workshops on the topic of powder rheology and works closely with clients on the application of the company’s technology.
About Freeman Technology
Freeman Technology specialises in systems for measuring the flow properties of powders and has over 15 years’ experience in powder flow and powder characterisation. Expert teams provide comprehensive support alongside the company’s range of products.
Systems are installed around the world across a diverse range of industries. They deliver data that maximise process and product understanding, accelerating R&D and formulation towards successful commercialisation, and supporting the long-term optimisation of powder processes.
Freeman Technology, a Micromeritics company, is headquartered in Gloucestershire, UK, with operations and distribution partners in key global territories.
In 2007 the company received the Queen’s Award for Enterprise in Innovation and in 2012 the Queen’s Award for Enterprise in International Trade. www.freemantech.co.uk
References
- S.E. Brika et al ‘Influence of particle morphology and size distribution on the powder flowability and laser powder bed fusion manufacturability of Ti-6Al-4V alloy. Additive Manufacturing 31 (2020) 100929
- M.S. Knieps et al ‘In situ alloying in powder bed fusion: The role of powder morphology’ Mat Sci and Eng A, 807 (2021) 140849
- L. Markusson ‘Powder Characterization for Additive Manufacturing Processes’ Degree Project. Published 2017. Available to view at: https://www.diva-portal.org/smash/get/diva2:1084670/FULLTEXT01.pdf
- R. Baserinia et al ‘Correlating polyamide powder flowability to mechanical properties of fabricated parts’ Powder Technology 398 (2022) 117147
Disclaimer: The views expressed here are those of the interviewee and do not necessarily represent the views of AZoM.com Limited (T/A) AZoNetwork, the owner and operator of this website. This disclaimer forms part of the Terms and Conditions of use of this website.