In spray coating applications, a fine powder, typically a polymer, is drawn from a storage device, fluidized, and then ejected through a charged nozzle onto a substrate.
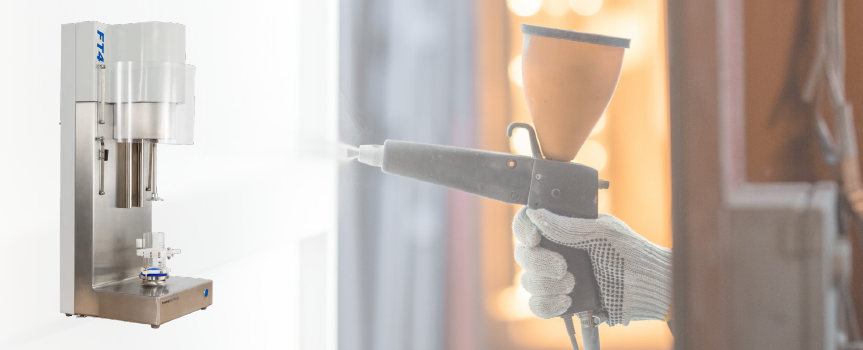
Image Credit: Freeman Technology
The powder must fluidize effectively and consistently, avoiding agglomerate formation that might clog the nozzle or impact the charging of individual particles. This ensures good adhesion and prevents agglomerates on the substrate.
Maintaining a smooth flow from the storage device is also essential because erratic flow into the fluidization chamber leads to poorly fluidized bulk material.
Identifying and quantifying powder properties that correlate with efficient process performance allows for optimizing new formulations without the high cost of running samples through the process for suitability assessment. This approach saves time, reduces raw material wastage, and minimizes rejected product output.
Variations in Process Performance and Product Quality
Three polymer powder samples were employed in a corona charging system's spray coating application.
Sample A exhibited adequate flow through the nozzle and good substrate adhesion, while Sample B displayed acceptable behavior. However, Sample C performed poorly, leading to nozzle blockages and poor adhesion to the substrate during transportation to the kiln.
Particle size analysis revealed that all three powders had the same D50 and size distribution. To assess the differences between these samples, we analyzed them using an FT4 Powder Rheometer®.
This analysis identified consistent variations in multiple tests, explaining the differences in performance and enabling us to screen future batches before introducing them.
Test Results
Sample A displayed the highest Basic Flowability Energy (BFE) and Specific Energy (SE) among the three samples, indicating strong cohesion and particle interlocking.
In contrast, Sample C exhibited the lowest BFE and SE, suggesting that a certain level of particle cohesion is necessary to create a uniform coating on the substrate, which Sample C lacks.
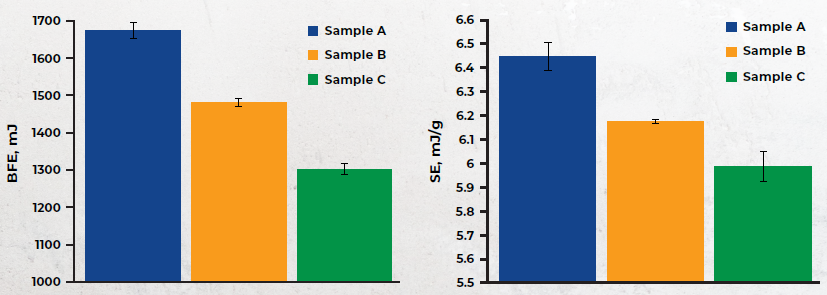
Image Credit: Freeman Technology
Bulk Testing: Compressibility
Sample C displayed the highest level of compressibility among the samples, indicating a stronger tendency to compact under forced flow conditions, such as when transferring the powder from the storage vessel to the fluidization chamber.
This increased inclination to compact can lead to agglomerates forming, hindering the nozzle's spraying and charging operations.
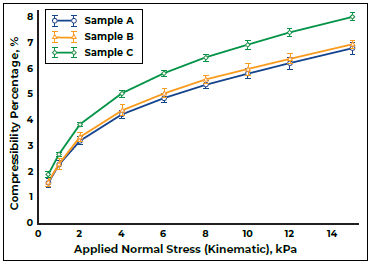
Image Credit: Freeman Technology
Bulk Testing: Permeability
Sample A exhibited the lowest Pressure Drop across the Powder Bed, signifying its superior permeability. This implies that it will flow more freely during conveyance and, once fluidized, will likely move more easily within an airstream.
Sample C demonstrated the lowest permeability, resulting in the highest Pressure Drop across the Powder Bed. This is likely to cause erratic, pulsatile flow into the fluidization chamber and unstable flow of the fluidized mass.
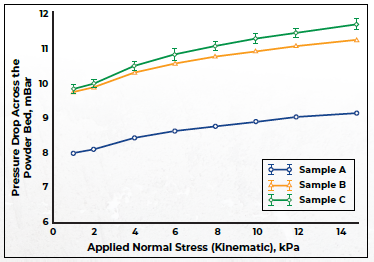
Image Credit: Freeman Technology
Shear Cell Testing
During Shear Cell testing, no differentiation was observed, as the measured Shear Stress values for the three samples were nearly identical, with an RSD of 2.5%.
This lack of correlation with the process performance indicates that the highly consolidated, low-flow environment of the Shear Cell test does not reflect behavior in the dynamic, aerated environment of a fluidization operation.
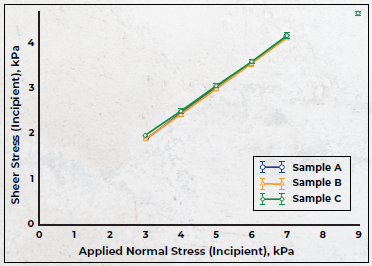
Image Credit: Freeman Technology
Conclusion
The FT4's multivariate approach has identified clear and consistent distinctions among the three powder samples concerning their Dynamic and Bulk properties, which align well with the in-process performance.
The results also underscore that relying solely on Shear Cell testing is not a dependable representation of powder behavior in this process, primarily due to the varying stress and flow conditions.
Sample A, with its higher BFE, SE, and Permeability, as well as lower Compressibility compared to the other samples, suggests that a certain level of cohesion is necessary for forming a uniform coating, but it may pose issues related to agglomeration and irregular flow within the process.
Sample C, which has the lowest BFE and Permeability and the highest Compressibility, is highly susceptible to compaction during its journey to the fluidization chamber. This compaction leads to the formation of agglomerates that can clog the nozzle and result in inconsistent charging.
The flowability of the powder is not an inherent material trait but concerns the powder's ability to flow as desired in a specific piece of equipment. Successful processing relies on a good match between the powder and the process. It is common for the same powder to perform well in one process but poorly in another.
This requires various characterization methods to comprehensively understand powder behavior across different operations.
Instead of relying on a single number characterization, the FT4 employs a multivariate approach to simulate a range of unit operations. This enables a direct examination of how a powder responds to different processes and environmental conditions.

This information has been sourced, reviewed and adapted from materials provided by Freeman Technology.
For more information on this source, please visit Freeman Technology.