One of the fundamental properties for optimizing battery cell performance is battery electrode porosity or void fraction. It is also important for evaluating the quality of cells. Understanding porosity in Li-ion battery electrodes is a vital part of cell design because it identifies what amount of electrolyte is required as well as the final electrode thickness, which has a bearing on energy and power densities.
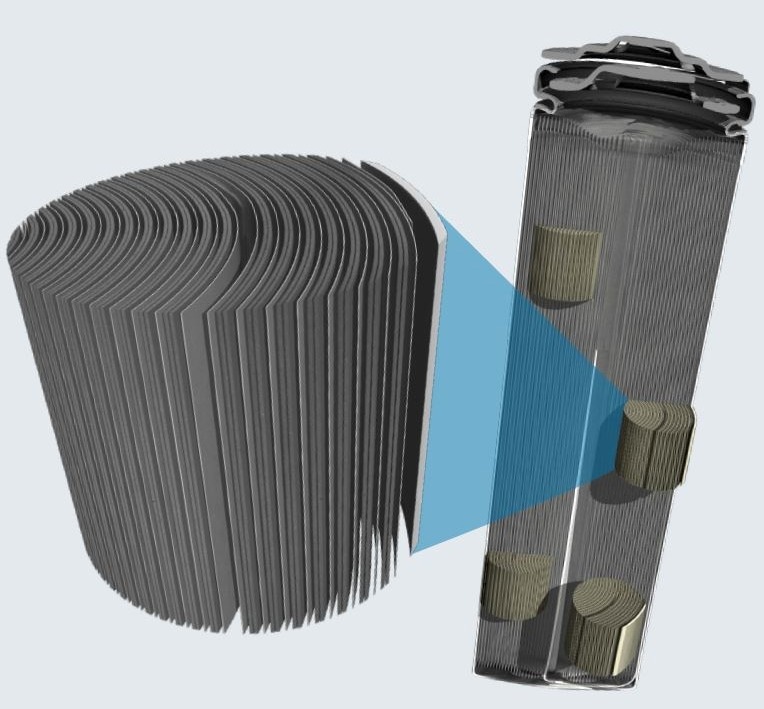
Image Credit: TESCAN USA Inc.
In theory, porosity also impacts electrode tape mechanical properties, electrochemical performance, and cell production cost. In plain terms, porosity directly influences product longevity, charging capacities, and overall cost, all of which are important issues that the battery industry today must deal with.
One of the most frequently performed analyses in battery production quality control processes is the characterization of porosity after calendaring. Naturally, many other parameters typical for electrode morphology can be measured.
Particle connectivity and particle shape may also influence electrical conductivity. Nevertheless, the chemicals and other materials, such as fillers or binders, used in the electrodes mostly co-determine the electrical transport phenomena.
The total porosity of the electrodes, as a whole, is tuned to ensure the highest energy density without inflating production costs. Micro-CT is an essential tool for materials characterization and modeling across a range of fields, from geology to additive manufacturing and even in the life sciences.
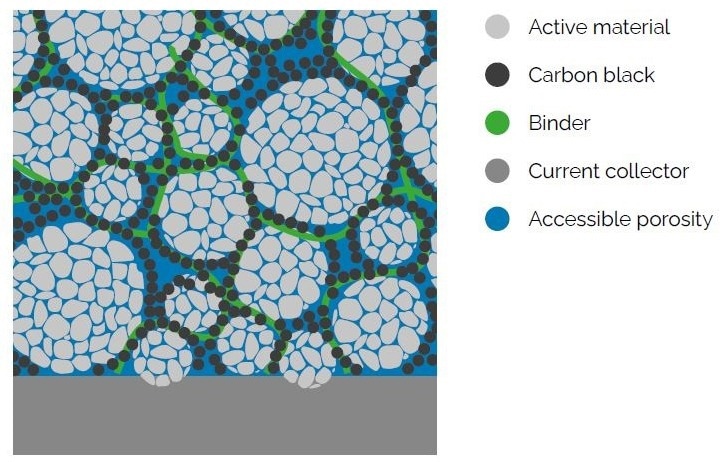
Figure 1. Scheme of the electrode structure showing total porosity (blue), active material (grey) and carbon filler (black). Image Credit: TESCAN USA Inc.
The large field of view and non-destructive nature of micro-CT fills a unique gap in characterization techniques for resolution levels from tens of microns to sub-micron.
Recently, the benefits of micro-CT have been celebrated in the energy materials community, and there has been a steady increase in the publication of various topics covering everything from traditional battery technology to innovative fuel cell designs.
In the rapidly expanding market of lithium-ion batteries, the versatility of micro-CT imaging means it can deliver information from the full-scale battery pack, individual cells, and even down to the singular electrode particles. Micro-CT systems are making their way out of the research lab into the quality and process control centers at battery manufacturing plants.
Materials and Methods
An industrial Li battery was scanned at 15-micron voxel size for an acquisition time of 120 minutes. The volume comprised four vertical sub-scans, reconstructed automatically and combined using TESCAN Panthera™ software.
For evaluation at high resolution, additional volumes of interest were extracted from the full volume. The control software positions these VOIs automatically and identifies the most optimal zoom factor.
For the anode porosity case study, a single graphite anode with dimensions around 10x10 mm was vacuum sealed in foil, then scanned using the TESCAN UniTOM HR at 1 µm voxel size.
TESCAN Panthera™ software was then used for reconstruction of the resulting CT scans. ORS Dragonfly software helped conduct 3D visualization and pore space analysis.
Results and Discussion
The main components of the battery were clearly resolved via an overview scan of the lithium-ion battery. From this scan (Figure 2), selected areas of interest, such as the anode, cathode, current collector and sleeve, can be evaluated while major defects at the battery cell level can also be identified.
Scans at this scale offer the ideal starting point for an analysis of common packing defects or geometrical quantifications, as is the case here for an indent in the copper current collector. However, the electrode was scanned separately to study porosity at the micron scale in a reasonable amount of time.
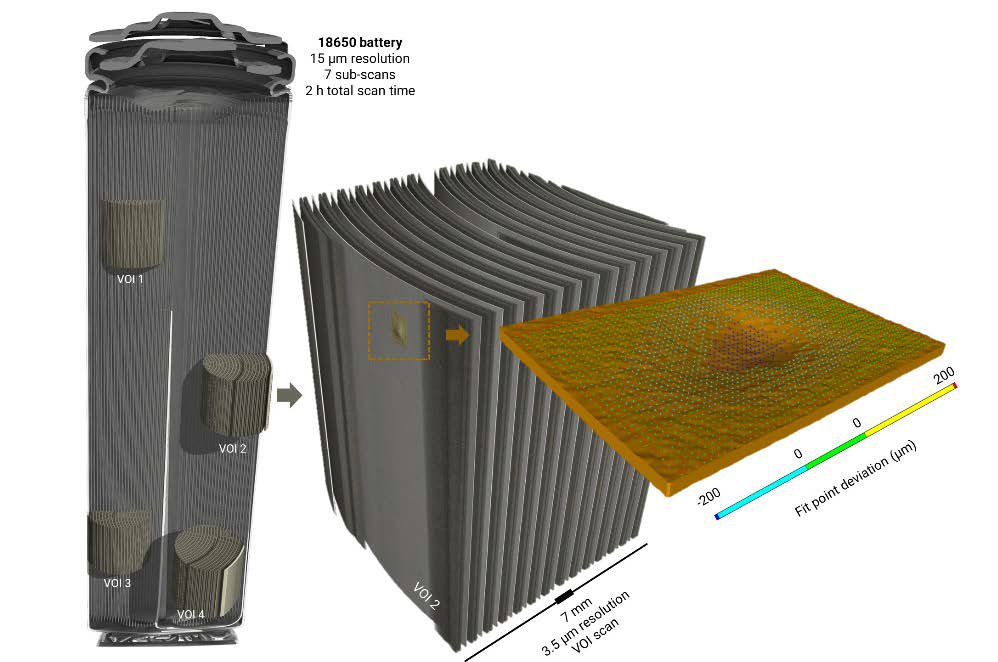
Figure 2. Li-ion battery: 20 µm stacked scan of the full battery. Major components—including anode, cathode, current collector, and sleeve—are clearly resolved, and major defects at the battery cell level can be evaluated. Image Credit: TESCAN USA Inc.
Volume of interest scanning (VOIS) makes it possible to perform additional scans using different conditions, such as higher resolutions, at areas selected for further investigation. VOIS was applied to generate higher magnification visualizations of electrodes across various scan zones.
The 3.5-micron voxel size facilitates the geometrical qualification of the copper anode current collector. Performing a scan of the separate anode prior to battery assembly covers enough detail to see particle disintegration and delamination from the current collector.
Subsequently, once reconstructed, this can be used as a starting point for characterizing porosity because the particles and the pore-spaces are clear in both 3D and the single slice.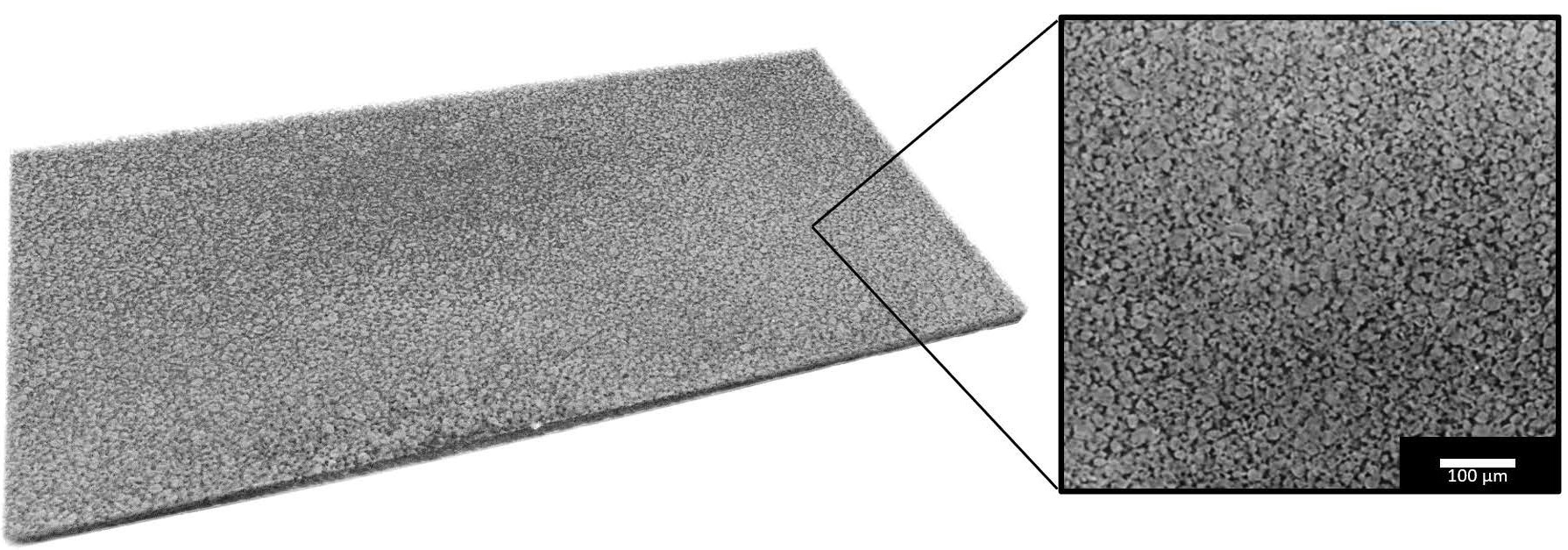
Figure 3. Anode foil scanned using the TESCAN UniTOM HR at 1 µm voxel size, scanned in 6 hours, visualized in 3D (left) and as a single slice through the volume (right). Porosity between the graphite particles (black areas) is clearly visible for further analysis. Image Credit: TESCAN USA Inc.
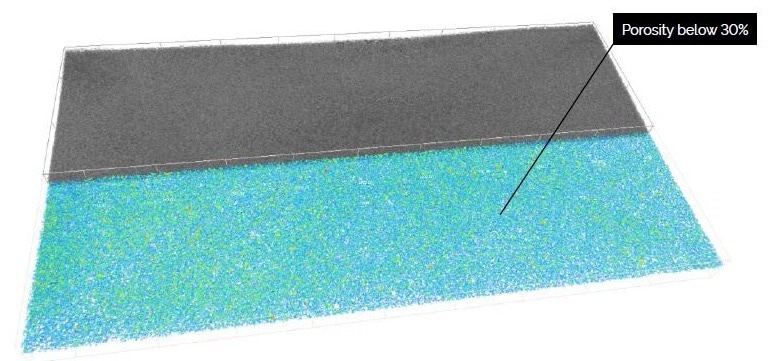
Figure 4. Visualization of the pore spaces in the anode. The color gradient reflects the actual size of the pore space; blue ~1.2 μm, green ~8 μm. (ORS Dragonfly was used for this analysis). Image Credit: TESCAN USA Inc.
Segmentation (Figure 4) and analysis performed using ORS Dragonfly revealed an average porosity of less than 30%, which is an acceptable void fraction for cell production. Although the scan was completed in a relatively short amount of time, the data was able to record pore sizes well below 2 µm.
In this case, the data proved that the battery anode had a wide variety of pore sizes, ranging from 1.2 µm to 9.6 µm, with relatively even distribution across the electrode volume as shown in Figure 5. This information proved crucial for optimizing electrical resistance and enhanced production economics by reducing the time for battery cell soaking with an electrolyte.
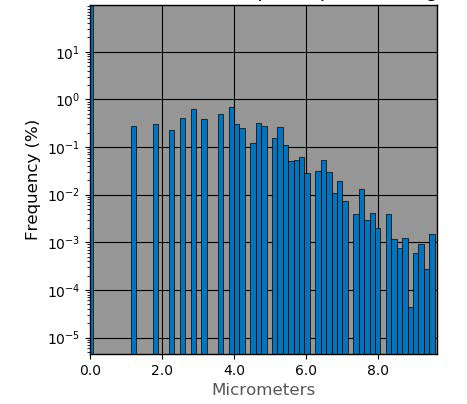
Figure 5. Histogram showing distribution of the volume thickness of pore space in the anode. Image Credit: TESCAN USA Inc.
Conclusions and Outlook
Optimized TESCAN UniTOM HR hardware and software for high-speed CT scanning is remarkably effective when analyzing anode porosity. It was possible to resolve graphite particles within the current collector without having to break the anode’s sealed packaging. As a result, porosity analysis is possible even on cycled anode specimens.
This study demonstrates that UniTOM HR is ideal if a rapid inspection of the anode or anodes is required. Furthermore, this technique is also useful for evaluating entire battery packs in quality assurance or research and development laboratories.
Sub-micron, high-resolution scans can be generated at unparalleled speeds, which facilitates rapid development of enhanced battery designs for almost immediate introduction to the market.
Automated Volume of Interest Scanning (VOIS) allows scanning of the battery components to be conducted in a quick and effortless manner at different scales, without requiring operator intervention. With this feature, a preview scan of the entire battery is quickly captured, which enables visualization of charge collector defects, delamination, or battery casing defects.
Once identified, these zones can be selected for further investigation at higher-resolutions and transmitted back to the scanner automatically. Other components such as electrodes can also be scanned in smaller volumes of interest at higher resolution.
Automated multi-scale analysis is a prize tool for any laboratory overseeing full design, development, and characterization of battery technologies.
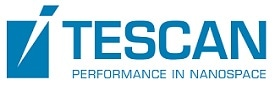
This information has been sourced, reviewed and adapted from materials provided by TESCAN USA Inc.
For more information on this source, please visit TESCAN USA Inc.