Sep 27 2006
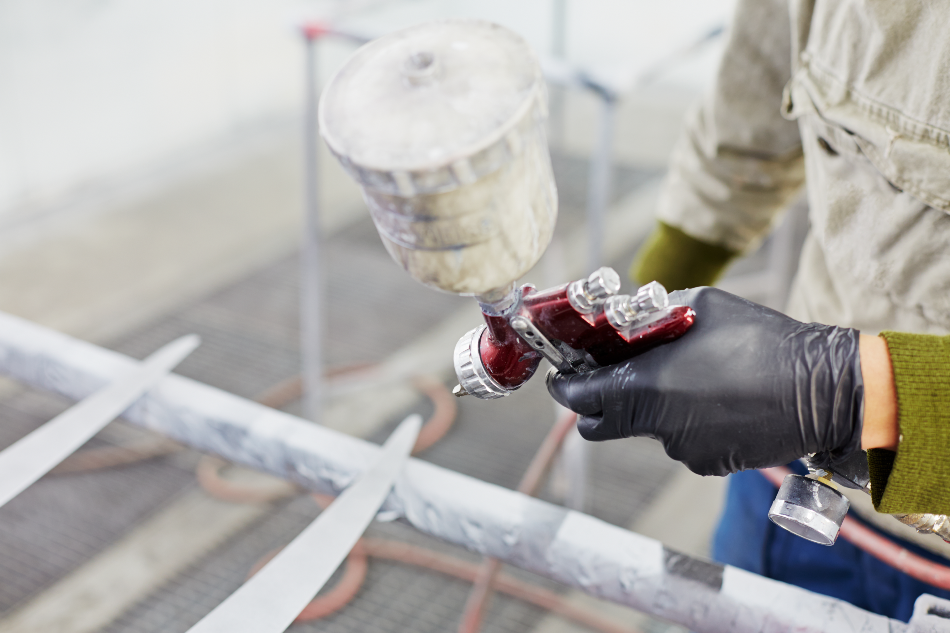
Pavel L Photo and Video / Shutterstock
Alumina-based Protective Coating is a revolutionary development that offers an exceptional protective oxide coating for titanium aluminide, with extremely strong substrate bonds.
At present, titanium aluminide compounds do not form a satisfying protective oxide coating that stops oxygen from diffusing into the titanium aluminide and forming oxides that degrade the compound.
The reason is that both TiO2 and alpha-Al2O3 form simultaneously in oxygen or air, but these oxides are not compatible. They do not produce a solid solution together. If these are the only oxides produced, then they would be too weak to bond together and thus form a weak bond in the titanium aluminide substrate. Consequently, the oxides tend to peel from the substrate.
Forming a Protective Coating on Titanium Aluminide
These problems are resolved and the protective coating is realized by using a two-step process that starts by making aluminum the dominant oxide developer. In the initial step of this process, a highly robust alpha-Al2O3/titanium aluminide substrate interface bond is created. Alpha-Al2O3 oxide then forms above this interface until another alpha-Al2O3 oxide layer of at least 5000-angstroms thick is created above the interface.
During this growth period, an attempt is made to form an entirely oxidized alpha-Al2O3 oxide, with the aluminum and oxygen atoms remaining in their chosen sites, and to form an ordered structure within the alpha-Al2O3 molecules.
In the meantime, titanium atoms diffusing from the titanium aluminide substrate may temporarily form an oxide, but aluminum atoms in the vicinity will instantly reduce the oxide to oxygen and titanium. However, as titanium atoms can diffuse faster than aluminum atoms in alpha-Al2O3 oxide, these titanium atoms will diffuse outward via the alpha-Al2O3 oxide and develop Ti2O3 molecules above the alpha-Al2O3 oxide coating.
Alpha-Al2O3 and Ti2O3 molecules are completely compatible because they produce the same crystalline structure and contain very similar lattice parameters. At this juncture, the original alpha-Al2O3 oxide layer will continue to grow gradually, but the mixed alpha-Al2O3 and Ti2O3 oxides will grow much more rapidly.
During the second-step process, TiO2 will start to form in a very accommodating manner: as fiber-like, micrometer-diameter columns embedded in the alpha-Al2O3/Ti2O3 matrix and growing almost perpendicular to the plane of the titanium aluminide surface.
The entire structure comprises a robustly adherent alpha-Al2O3/titanium aluminide interface with at least a 5000-angstrom thick alpha-Al2O3 oxide growing above it. It also has TiO2 fiber-like, micrometer-diameter columns embedded in the mixed alpha-Al2O3/Ti2O3 matrix, reinforcing it with the final surface.
The final surface displays the TiO2 fibers extending upward from the top of the mixed oxide matrix in which the fibers are embedded. A structure like this has been grown to thicknesses of up to 50 µm.
Stylometer measurements have revealed that the cohesive strength of the whole mixed oxide is a function of the degree of oxidation that has occurred. As the mixed oxide reaches a state of nearly full oxidation, the cohesive strength reaches the high cohesive strength of the original alpha-Al2O3 oxide coating measured at the end of the initial-step process.
Benefits of Using the Protective Coating on Titanium Aluminide
- Forms an absolute oxygen barrier coating for the titanium aluminide substrate.
- Serves as a self-healing coating with surface titanium oxides, in case some surface destruction is caused by an impinging particle, by diffusing titanium atoms to the surface to react with oxygen so as to affect a repair.
- The use of the total alpha-Al2O3/Ti2O3/TiO2 mixed oxide system is to guard the surface of titanium aluminide better than any known mix of oxides. Simultaneously, each of the oxides in the general coating has a very high cohesive strength, and each is attached to one another and to the substrate with extremely strong adhesive bonds.
- It offers an atmospherically exposed surface with fiber-like, micrometer-diameter crystalline columns, integrated into the mixed alpha-Al2O3 and Ti2O3 matrix. These matrices grow in a virtually perpendicular direction corresponding to the plane of the titanium aluminide substrate surface. The outer surface may attach well to an applied Thermal Barrier Coat (TBC).
Applications of the Coating
- Automobile manufacturing
- Aircraft manufacturing
- Aircraft engine manufacturing
- Steel and stainless steel products
- Manufacturing of superalloys
- Superalloy products
- Manufacturing of iron, chromium, nickel, and cobalt-based alloys
- Products that must be protected against oxidation over a broad range of temperatures
- Products made from iron, chromium, nickel, and cobalt-based alloys
- Alloy-based products that must be protected against atmospheric oxygen at all operable temperatures