Nov 7 2009
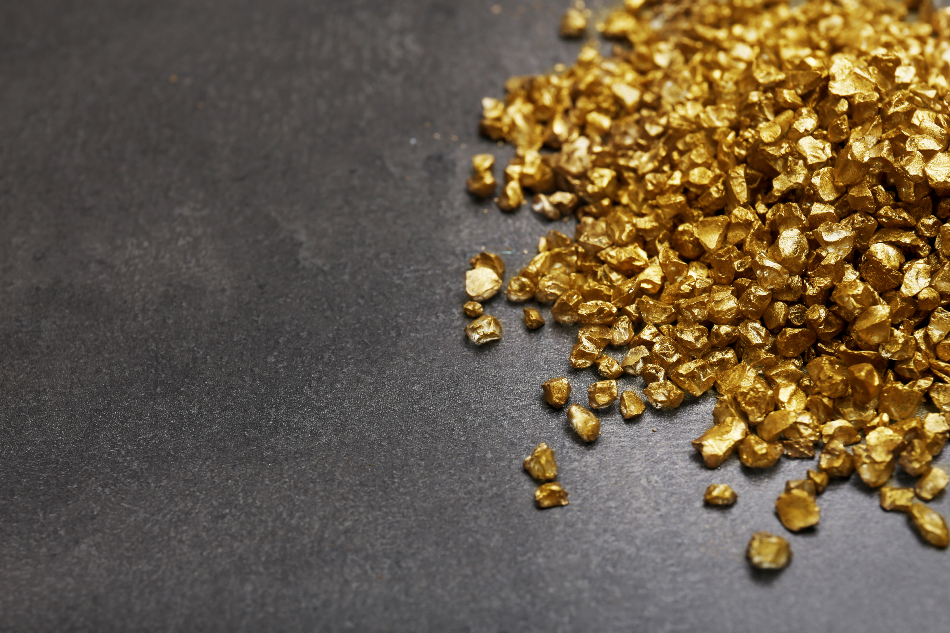
Africa Studio / Shutterstock
Electroforming of gold was conventionally used for manufacturing jewelry. Today, it is used for manufacturing industrial components.
Solid Gold Electroforms
UK-based company ABSSAC Ltd uses a novel patented electroforming technology to supply solid gold electroforms. This exclusive combination of properties makes gold an essential component in several electrical, medical, and industrial applications. In the application described below, electroformed gold contacts were utilized in a circuit testing machine.
The Electroforming Process
Electrodeposited products are initially made by machining a precision mandrel to the shape of the required form (or within the bellows). A correct thickness of the quality metal is then deposited on to the mandrel. When the mandrel is dissolved, the precision finished product is left behind. The use of gold within applications has made it possible to exploit a few exceptional properties of the material.
Desirable Properties of Gold
For instance, gold is known to be the most non-reactive of all metals. It is innocuous in all industrial and natural environments. Gold does not react with oxygen, implying that it will not tarnish or oxidize. It is also the most electrically conductive of all metals and can transmit even a small electrical current in temperatures ranging between –55 °C and +200 °C.
In addition, gold is the most reflective and lowest absorbing material of infrared (or heat) energy. High-purity gold can reflect up to 99% of infrared rays, yet it is also an excellent conductor of heat or thermal energy. Finally, gold is well-suited for implantable or invasive medical devices as it is one of the materials that is least rejected by the human body.
Electroforming of Complex Shapes
By improving the gold electroforming method, ABSSAC Ltd can supply highly complex parts with thin walls, deep crevices, unusual shapes, and other design features. The electroforming process has been specifically developed for tolerance-critical small parts and makes them appropriate for rigid electroformed components as well as flexible bellows.
Furthermore, the controlled electroforming process can lead to variations in the thickness of the wall in different places on the same part for selective flexibility and rigidity. This enables hollow parts with walls as thin as 0.0005″ (0.012 mm) suitable for miniature applications such as precision instruments and electrical bellows contacts.