Nov 7 2009
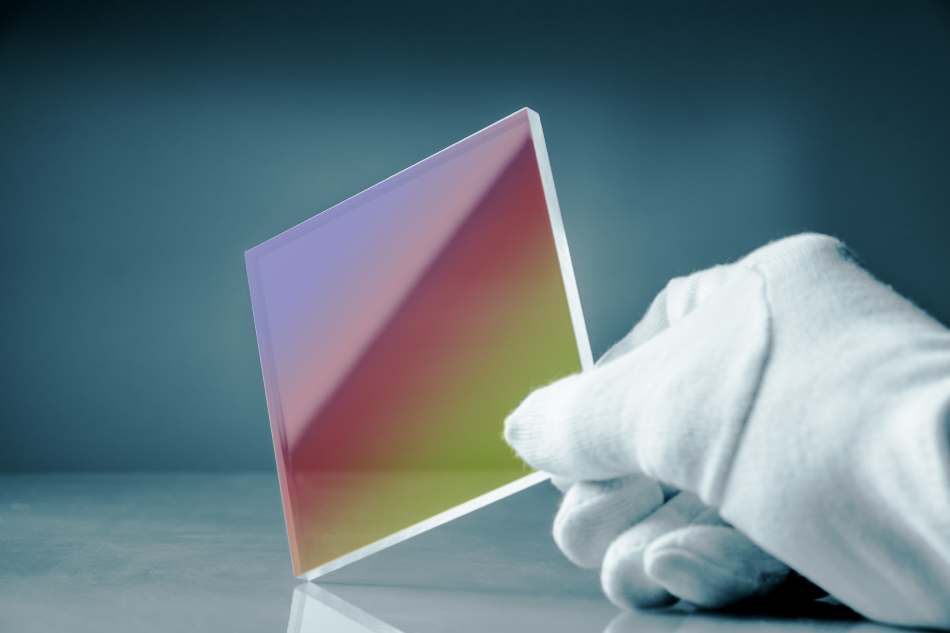
science photo / Shutterstock
Several advanced applications require engineers to specify a hard electrochemically deposited gold coating. This coating should be able to integrate the theoretical reflectivity and emissivity of gold with a surface that can essentially be cleaned physically. But this is very difficult to achieve.
However, in the last 20 years, a small company in Brooklyn, New York, has become the world’s top supplier of such material.
Epner Technology is a family-owned business that was set up in 1910. Beginning with decorative electroplating, the company has grown into the world’s top supplier of an electroplated, infrared-reflective, optical coating for the aerospace, computer, medical, and defense industries.
The proprietary Laser Gold™ material can be applied to imaging optics without distorting the optical figure, and the extraordinarily low emissivity (0.02) makes it the perfect choice for a vast number of unconventional applications. Surface analysis using a scanning electron microscope reveals a nano-crystalline deposit of pure gold.
Properties of Gold
Why was gold required for these applications? It may not be universally known, but gold is the most efficient and durable reflector of infrared energy. In visible light, gold might just reflect approximately 40%, but in the infrared spectrum, a freshly vapor-deposited or sputtered gold, although very fragile, can reflect over 99%!
Pure electroplated gold can virtually duplicate the reflectivity of the vapor-deposited gold, but it is also very fragile. If alloyed with cobalt, for instance, it becomes adequately strong, but the coating degrades with continual exposure to heat. The impetus to develop an ideal high-performance, strong coating came from Xerox company, and its pressing need to source such material for one of its machines.
With the advantage of more business ever witnessed by this small company, Epner’s chemical engineers started R&D to create a gold plating process. This process could endure the abrasion of the passing paper, the intermittent cleaning effort, and yet meet Xerox’s comparatively low reflectivity specification of 91%.
The researchers’ effort was fruitful, and Epner began to increase its production, but the excitement was short-lived. Tests conducted at Xerox revealed that the performance of the reflector was unreliable. Epner’s management and production team were disappointed to see hundreds of reflectors being rejected as “out of spec” for reflectivity, something that could not be ascertained with the naked eye.
It quickly became obvious that without the same instrument used by Xerox to measure reflectivity, Epner could never be certain that the product it was supplying met the specifications.
Xerox supplied Epner with an identical advanced infrared spectrophotometer. This single tool triggered a renewed R&D that over the following years constantly enhanced both the hardness and reflectivity. For more than two decades, Epner Technology has been the only supplier to the National Bureau of Standards, (currently known as NIST), of the gold reflectance reference standard. Customers can calibrate their spectrophotometer with a mirror made in Brooklyn.
Laser Gold™ Material
Despite the trade name, the Laser Gold™ material is not actually produced using a laser. The name was embraced when the first company (other than Xerox), to gain from this exceptional coating, was an Nd-Yag laser manufacturer.
Epner soon turned out to be the “go to” a source in the Nd-Yag laser industry for this high-efficiency coating. Thus, the name, Laser Gold™, is presently a trademarked brand known internationally.
With Epner’s commitment to stringent process control, the company’s customer list includes prominent—and demanding—companies in the aerospace, optical, electronics, and computer industries. During the past two decades, the most remarkable projects of Epner Technology have involved work for NASA, directly as well as indirectly through its suppliers such as Raytheon, Ball Aerospace, and Lockheed, among others.
An example is the Mars Orbiter Laser Altimeter Mirror (MOLA) developed to map the topography of the Red Planet, which used Laser Gold™ coatings.
Epner Technology has also taken part in one of the longest-running NASA programs—the Geostationary Operational Environmental Satellite (GOES). This satellite offers real-time weather images that are seen daily on the news, over the past 25 years. Its performance was improved with the consistently low emissivity of Laser Gold™. Such low emissivity helps keep the thermal stability of core instruments.
Commercial Applications of Laser Gold™ Material
There are a few exciting commercial applications for Laser Gold™ coating and other Epner Technology products, that are spin-offs of space and weapons project. Epner is presently working with Formula-1 and NASCAR designers to create a flexible heat barrier in racecars, delivering a safer and more comfortable driver’s compartment. In other cases, it allows fuel and brake fluid to run cooler and/or safeguard the carbon fiber composite material against the over curing of the heat of the exhaust pipe.
Another ongoing project will enable firemen in smoke-obscured buildings to view using infrared sensors that can read Laser Gold™ fabric reflectors, coded to recognize individual fire-fighters through the smoke. Flexible gold foil or mesh can be laminated to protective clothing to resist heat, thus enhancing the safety, comfort, and endurance of a worker on the job.
From gas detection cells to micro light-pipes that get threaded into the heart, it's been an exciting business. We've learned, we've grown, and we've participated in some of the most ‘envelope-pushing’ projects in the world. Almost every day a new challenge comes through the door, (more likely the Internet) and I get to have lunch with some of the top scientists and engineers in the U.S. and Europe. At 74, retirement is just not part of my lexicon.
David Epner, President, Epner Technology