Jun 20 2001
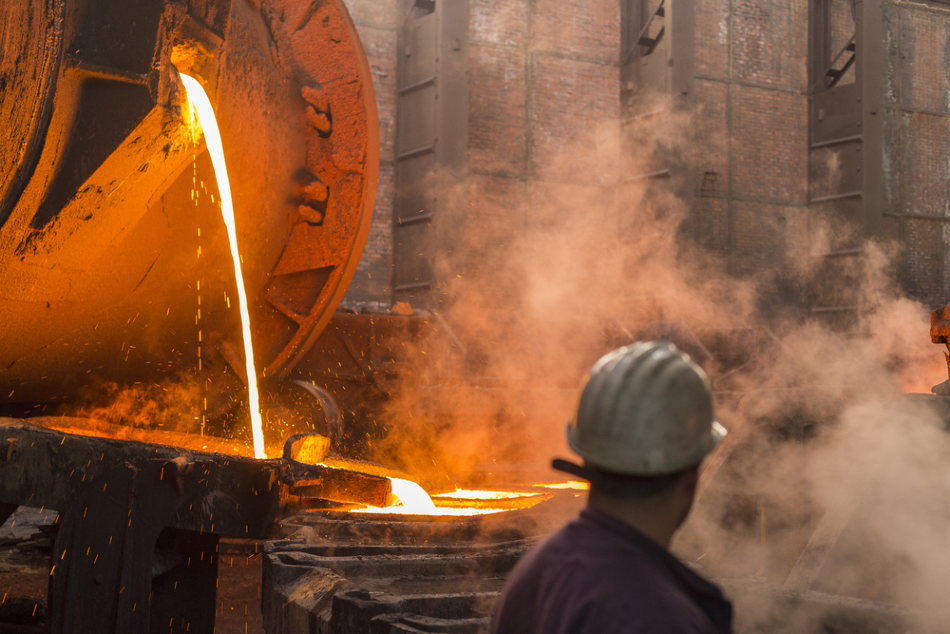
Image Credit: Djelen/Shutterstock.com
Article updated on 03/03/20 by Clare Kiernan
Industry is always keen to seek out cost-effective practices to compete and survive. Recognizing this trend, publications from the Copper Development Association (CDA) have emphasized production and lifetime economies as a paramount advantage.
After five thousand years of use, the technology of copper should be fairly well understood, and whilst this is true, there are still many considerations to be taken into account when electrical equipment is being designed.
Switched-Mode Power Supplies
Energy for most electronic equipment is provided by switched-mode power supplies, a solid-state power management system that gives close control of voltage requirements. These select the required power from each wave of AC power supplied from the utility, setting up distortions in the waveform and giving current harmonics at frequencies that are not accurately measured by conventional instruments. It can also result in the disturbance of power flow in conventional three-phase installations, such that abnormally high currents can be present in the neutral conductor. Conventional practice has been to consider downsizing the neutral conductors because they were not expected to carry the full current of phase conductors, through overheating, however, experience in many installations has proven the need for twin or double-sized neutral cables. This generated a need for five-core power cables that are only being met by specialist makers (figure 1).
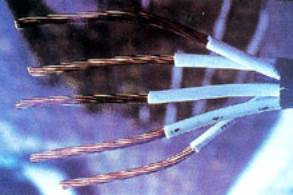
Figure 1. Five-core cable developed to handle modern power requirements.
Reliability
Reliability is a factor that must be considered when risk management is involved in commercial and industrial buildings. If the consequential cost of power failures is likely to be untenable, duplication of vital power supply circuits is normally recommended by the consultants responsible for mechanical and electrical services.
Employee Safety
Employee safety is always of paramount consideration and there is now a greater understanding of the possible effects of electric shocks and the ways in which earthing systems can be designed. Fifty volts are agreed to give the onset of danger of shock and a current of a few tens of milliamps passing through the heart region is enough to cause fatality. Earthing systems must be designed not just as a safety backup but to be conductors in continuous use.
Earth Connections
Switched-mode power supplies for items such as computer equipment generally rely on an earth leakage current to stabilize the voltage control. This is limited by regulations to no more than 3.5mA, but an installation of ten or more pieces of equipment can easily reach a total that is potentially lethal to operators. A break in an earth connection can result in half of the mains voltage appearing on the earth line. If, for example, IT equipment is earthed through only one component, a serious shock may result if the equipment data cables are disconnected. Not only is it essential to ensure good earth continuity for every item of equipment, but it is also necessary to ensure that earth returns are not left to the sheathing or conduit with joints that may deteriorate in service. Good practice now requires that a dedicated copper conductor be used.
Equipotential Areas
The need to create an equipotential area requires the underground installation of a carefully planned network of bonded copper tapes or rods across the complete site to be protected. Above ground, other materials may sometimes be used for external conductors for a lightning protection system. In this event, it is essential to ensure that any bi-metallic joint to the underground copper conductor is made to recognized welding quality standards, is well above ground level and is adequately protected from ingress of moisture.
Underground Corrosion Behaviour
Copper water pipes have been successfully used underground for centuries. In most soils, the performance is totally satisfactory. Only when the area is severely contaminated with ashes or similar acid residues, have there been severe corrosion problems. Useful underground corrosion trials have been carried out in the UK and US but always on the deoxidized copper normally used for pipework. In general, experience shows that these values are not significantly different either for the high conductivity copper used in electrical applications or for the oxygen-free coppers being evaluated for the containment of nuclear waste.
Electric Motors
As electric motors running continuously can consume their own cost in electricity in less than four weeks, the need for considering energy-efficiency is obvious. This means designing motors with rotor and stator cores and windings that give minimum iron and copper losses in electrical terms. In the US, motors must meet the National Electrical Manufacturers Association (NEMA) standards for efficiency and it makes good sense to specify correctly rated high-efficiency motors for all applications. Continuing development resulted in the leading UK manufacturer being able to offer energy-efficient motors with no premium on price.
Power Cables
Less obvious is the need to specify power cables to give the lowest lifetime costs. The IEE regulations standardized in BS 7671 (≠IEC 364) specify minimum sizes needed to prevent overheating and possible fires. Surprisingly, efficiency is hardly considered in the standard, although BS 7450 (=IEC 1059) for the determination of economic optimization of power cable size was published in 1991. Upsizing to reduce power losses saves electricity directly. It can also save the cost of removing excess heat and ensure that motors being supplied by the power cables run at voltages designed for best efficiency.
Power Transformers
The specification of power transformers involves capitalizing energy losses to assess the most economic design needed to suit the lifetime and expected capital service costs. As the lifetime of transformers is usually measured in decades, the need for stipulating the lowest iron and copper losses is again paramount.
Bus Bars
Standard practice is normally to rate busbars for a working temperature of 95 °C. In practice, many run at higher temperatures due to being used as heat sinks by an adjacent plant. The systems are designed to survive severe mechanical stresses generated by short circuits, the number of supports installed means that this does not normally result in sagging because of creep problems.
Although welding is possible, copper busbars are usually joined by bolting (figure 2). This means that the system can be easily modified. Codes of practice recommend that the mating surfaces are tinned, petroleum jelly is used between the joints and that the bolts are tightened to a specified torque to give good contact for many years. Joint integrity does not then deteriorate in normal service due to oxidation or corrosion.
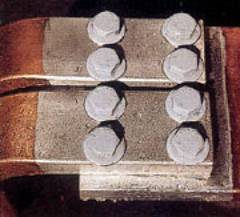
Figure 2. Busbar joints, properly tinned and bolted are reliable in service and easily modified.
Cooling of busbars is normally carried out by a combination of convection and radiation. Once they have been in service for some time, a thin coating of black oxide forms which gives a more efficient radiating surface and improves performance.
Summary
Besides it being the metals that are vitally needed to meet requirements for electrical and thermal conductivity together with strength, corrosion resistance and ease of fabrication, copper and copper alloys are also promoted for their cost-effectiveness properties. When lifetime service is evaluated, considering initial costs, production costs and running costs, copper is frequently the first choice. In many instances, copper alloys are also the cheapest first cost materials fit for the purpose. When machining is involved, components can frequently be made more cheaply from brass than from steel. This is especially true when the cost of the steel parts must consider finishing for corrosion protection.
Primary author: Vin Callcut
Source: Materials World, Vol. 5 no. 6, pp. 320-21 June 1997