Nov 21 2012
Table of Contents
Introduction
How Polymers are Configured
Intra- and Inter-Polymer Characteristics:
Glass Transition Temperature (Tg) and its Physical Meaning
Melting and Crystallization Temperatures Tm and Tc
Polymer Molecular Weight and its Meanings
Mechanical Properties of Polymers
Fracture Mechanics of Polymers and its Applications
Conclusion
About Ceram
Introduction
Polymers are the most widely used materials in the pharmaceutical and medical devices industry. However, there have been instances of unexpected product failure and yield deterioration driven by changes in the physical and chemical structure of polymer materials that may occur during production, post treatment, transportation, in storage or in use. These structural changes may range from millimeter, micro and up to nano scales, thus eventually affecting the performance of the product. This paper introduces the basic concepts related to polymeric materials’ structure and properties.
How Polymers are Configured
Polyethylene (PE), having the simple structure, is made from ethylene CH2=CH2 via a polymerization process that opens its double bond and forms a structure as follows.
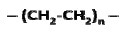
Figure 1
The average molecular weight for a linear PE ranges between 200,000 g/mole and 500,000 g/mole. A single PE chain can modify its configuration instantly and randomly. The long chain polymer, with a high length to diameter ratio, behaves like a soft rubber wherein highly entangled chains are stretchable under force and can retain their original state upon release. By replacing one H from each repeat unit of PE with Cl, poly-(vinyl chloride) (PVC) can be created.
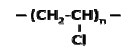
Figure 2
However, the change in element makes the -C-C- bond rotation in PVC difficult, making it stiff. The structural change from PE to PVC has significantly affected the properties and applications of the two polymers.
Intra- and Inter-Polymer Characteristics:
Intra-polymer structure characteristics: Polymer chains are mostly ‘soft’, ‘stiff’ or in-between. The intra-polymer structure characteristics of the polymers decide whether a long chain polymer is ‘stiff’ or ‘soft’ or something in between.
Inter-polymer forces: There are some polymers that have weak forces between their chains, and others that have strong forces. van der Waals forces decide this inter-polymer force. These two factors can help in understanding the varied properties of polymers and also the reason why polymers are very different from materials like metals and ceramics.
Glass Transition Temperature (Tg) and its Physical Meaning
An important parameter unique to polymers is Tg. The length of a polymer chain segment varies due to intra-and inter-polymer characteristics. Figure 3 illustrates the rapid changes in shape when a rope is moved up and down.
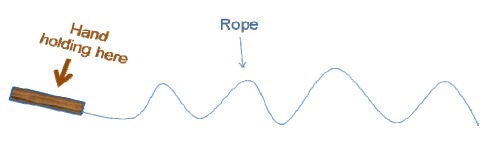
Figure 3
From this illustration, it has been observed that the stiffness of a polymer chain increases with the length of its segment. Tg can be defined as the transitional temperature at which polymer segments begin to flow from the frozen state (with raise in temperature), or start freezing (with drop in temperature). Figure 4 illustrates this change in the chain segment.
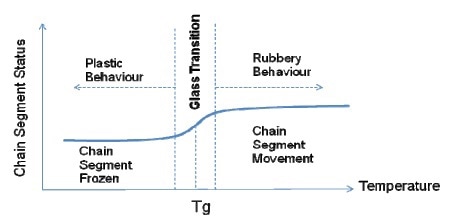
Figure 4
Melting and Crystallization Temperatures Tm and Tc
By contrast to majority of the inorganic crystalline materials, polymers are not able form 100% crystals. Polymers always have at least two phases namely, amorphous and crystalline. It is not its Tg, but rather its crystallinity that determines whether the material is a plastic or rubber. The crystals (hard phases) and rubbery (soft phases) make the PE behave as a plastic with toughness, and not as a rubber. Re-crystallization takes place on heating before melting, which increases complexity in polymers.
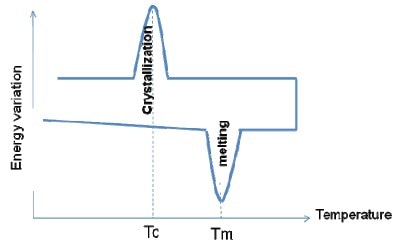
Figure 5
Both melting and crystallization cover a specific range of temperatures around the peak temperatures Tm and Tc. The uncompleted crystallization process is responsible for the re-crystalllization on heating. Hence, when the polymer is heated, re-crystallization will take place at temperatures before the melting temperature of the existing crystals. Hence, Differential Scanning Calorimetry is not reliable for polymer crystallinity measurement.
Polymer Molecular Weight and its Meanings
There are two ways widely utlized to present molecular weight as a polymer parameter. One is number average of molecular weight Mn, and the other is weight average Mw. Figure 6 illustrates a realistic molecular weight distribution.
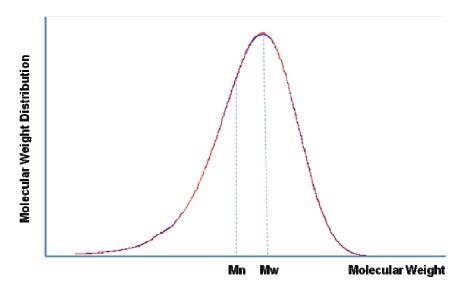
Figure 6
Mechanical Properties of Polymers
Two extreme cases namely a very brittle polymer and a very ductile polymer are illustrated to demonstrate the real performance of polymers in Figure 7.
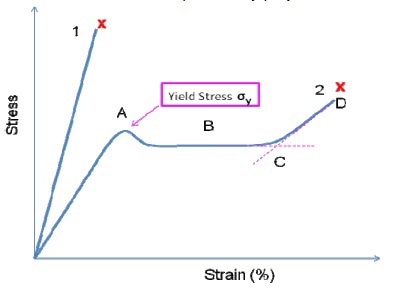
Figure 7
It is possible to obtain the polymer’s Young’s modulus (E) from the slope of the stress/strain curve’s initial linear elastic region. Other mechanical properties that can be obtained from the curve include:
- Initial yield stress prior to the polymer yield
- Minimum stress after initial yield
- Strain hardening at which the gradient begins to raise due to the polymer chain being completely stretched along its stress direction (higher stress is needed for further deformation).
- Failure stress at which the polymer has attained its maximum allowable stress.
Fracture Mechanics of Polymers and its Applications
In fracture mechanics, the concept of fracture toughness (KIC) is described as
KIC = σc (Πa) 1/2 eq (1)
In the equation, σc refers the critical failure stress for a defect size ‘a.’ The correlation between fracture stress and defect size is identified by the fracture toughness, a materials constant. Defects always present in different levels ranging between nano or micrometer scales and up to mm scales.
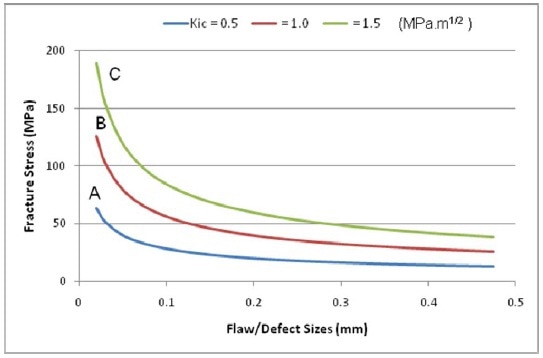
Figure 8
In the figure 8, for a given defect or crack size of 30 µm, Polymers A, B and C will not rupture until applied stress nears stresses of 52, 103 and 155 MPa respectively, highlighting the significance of increasing polymer fracture toughness to prevent product failure.
Conclusion
It is important to understand basic physics, chemistry and mechanisms of polymers for technologists, engineers, and scientists who are involved in new product development using polymers or who require to work out problems during production. Acquiring insights into the relationships between the demanded chemical and nano/micro structures of polymers and product performance will be helpful in accelerating the identification of the root causes of polymer failure to prevent future failures.
About Ceram
Ceram is an independent global expert in materials testing, analysis and consultancy. Ceram provide customized solutions that can help you to measurably improve performance and profitability through safer, regulatory-compliant and better-engineered products.
Ceram experts set new standards in materials testing and work as an extension of our clients’ teams, applying their expertise and capabilities to a wide range of industries, including:
- Aerospace & Defence
- Automotive & Transport
- Construction
- Consumer & Retail
- Electronics
- Energy & Environment
- Healthcare
- Materials Manufacturing
- Minerals
- Refractories
Headquartered in Staffordshire, UK, Ceram has accredited laboratories and offices around the world and employs a team of research and product development professionals who specialize in physical and chemical materials testing, research, process engineering, failure analysis and product design.
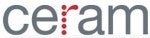
This information has been sourced, reviewed and adapted from materials provided by Ceram.
For more information on this source, please visit Ceram.
Disclaimer: The views expressed here are those of the interviewee and do not necessarily represent the views of AZoM.com Limited (T/A) AZoNetwork, the owner and operator of this website. This disclaimer forms part of the Terms and Conditions of use of this website.