The range of industrial applications for the plasma carburising process has been increasing over the past ten years as its benefits have been recognised in the automotive, heat treatment and now aerospace industries. The Process Carburising is a batch process (figure 1) introduces a surface layer of metal carbide that improves the hardness and wear properties of components. Traditionally, gas-carburising is used, in which gaseous hydrocarbons undergo reactions to provide the source of the carbon. In plasma carburising, as the name suggests, these gaseous reactants form a plasma which is used to treat the component surface. 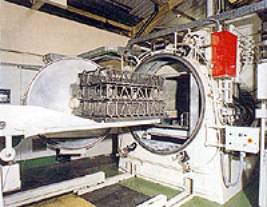 | Figure 1. A batch of components being loaded in preparation for plasma carburising. | Advantages of Plasma Carburising Plasma carburising offers a number of advantages over traditional gas carburising, according to Ipsen Abar. The carburised layers produced by the process have a better structure and so better properties. Thus, there is no internal oxidation, and the layer has better uniformity which often leads to lower distortion of the component. In addition, controlling the formation of carburised layers is easier with plasma carburising as the amount of carbon transferred to the surface depends on the electric plasma current density, which can be monitored and controlled. As a result, the process offers very good reproducibility. Ipsen’s recent furnace for GKN Westland Aerospace Transmissions comes equipped with Plasma-Prof, a control system that tracks process parameters, controls them, and monitors and archives the process. Plasma carburising can offer shorter cycle times than traditional processes, partly thanks to the use of higher temperatures. For example, case depths of 2.5-3mm can be achieved by low-pressure plasma carburising in 20 hours, roughly half the tune needed by conventional processes. Finally, plasma carburising also offers simple mechanical masking, allowing localised carburising. Thanks to electrical field effects, no carburising takes place underneath a mask, allowing traditional, costly masking methods such as copper electroplating and covering with stop-off paste to be eliminated. Acceptance of Plasma Carburinsing Similar plasma processing systems are already in use throughout Europe, for example at Ford's plant in Cologne and at a commercial heat treatment shop in France. With easy integration into production lines, plasma carburising systems, now proving beneficial in the aerospace sector, look set to take off and carry the process into an ever wider range of industrial applications. GKN Westlands Aerospace Transmissions GKN Westland Aerospace Transmissions is the latest company to employ the process, installing a production-size furnace from Ipsen Abar UK following its success in securing the Apache helicopter contract. The two chamber furnace, which can process loads of up to 800kg, can perform plasma carburising, vacuum carburising and vacuum hardening up to 1320°C. It will allow GKN Westland Transmissions to enhance the performance and properties of its components in a variety of military and civil transmissions programmes. |