Jul 4 2008
Long Product Mill Balakovo”, OAO Severstal’s 100% subsidiary, has awarded Siemens VAI Metals Technologies a contract to supply a finger shaft electric arc furnace, a ladle furnace, a dedusting system and a billet caster for a new long-product steelmaking facility which will be built at Balakovo in the Saratov Oblast Region. The order value is a two-digit million Euro figure. Upon completion of this project scheduled for mid-2010, Severstal is planning to produce an additional one million tons of billets which will be rolled into structural steel products for use in the local market.
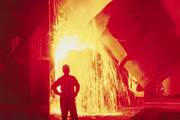
Severstal is the biggest steel manufacturer in Russia and the fifth largest in the world. Its “Russian Steel and Metalware” business division, with rolling and processing facilities located in Cherepovets, Kolpino and Izhora, including Severstal-Metiz, produced a total of 11.27 million tons of crude steel in 2006, comprising a wide range of flat steel and long products. These include hot- and cold-rolled flat steel (and also coated steel), hot-rolled sections, roll-formed shapes, rebars, wire rod and pipes. In order to broaden its product range of long products and to be closer to end-consumer customers, the company has decided to build a new steel works in the city of Balakovo, about 1,000 kilometers southeast of Moscow in the Saratov Oblast Region. This business unit will produce carbon and low-alloy structural steel which will be rolled into light structures, reinforcement bars and wire.
For the mill, Siemens Metals Technologies will supply a new 125-ton finger-shaft electric arc furnace, a 125-ton ladle furnace, the associated primary and secondary dedusting facilities and a 5-strand high-speed billet caster. The heat from the furnace offgas will be used to preheat the scrap, which is retained in the shaft by so-called “fingers”, and therefore significantly reduce both the electrical energy consumption and the tap-to-tap times. The diameters of the AC EAF electrodes will be 610 millimeters. The ladle furnace will be used to fine-tune the steel composition and to adjust the final temperature for casting. The billet caster will be equipped with DynaFlex Oscillators to enable the mold-oscillation parameters (stroke and oscillation frequency) to be adjusted online according to the steel grade, casting speed and operational requirements. The retractable type oscillator that will be used in the caster allows for continuous billet production during mold replacement on individual strands. The caster will also be fitted with Diamold high-speed casting molds characterized by tapered mold tubes with open bottom corners to reduce strand friction. 150x150-millimeter billet sections will be cast.