Aug 14 2008
Manufacturers of check valves and pressure relief valves for hydraulic and pneumatic compressors are constantly looking for ways to improve the performance of their products. Valve performance, more than any other component, determines compressor efficiency.
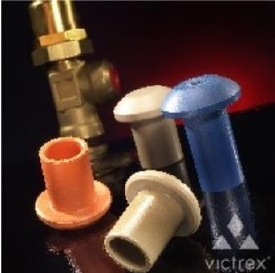
To achieve improvements such as reduced fluid leakage, noise reduction, longer valve life, and cost reduction, a number of manufacturers are turning to Performance Plastics Ltd. (PPL), a high performance injection molding specialist, for assistance. To meet the requirements, PPL suggests replacing the metal poppets in the valves with poppets made of VICTREX® PEEK™ polymer, a high performance thermoplastic. Substituting plastic for metal maintains strength while improving corrosion resistance, reducing weight, and allowing for greater design flexibility.
“Manufacturers have been quick to see the benefits,” explained Joe Simmons, Sales Engineer, at PPL. “The polymer’s superior combination of properties, including temperature performance, chemical resistance, friction and wear performance, as well as impact resistance make it a highly cost-effective solution for improving performance.” One of the major benefits using VICTREX PEEK polymer is that it allows the valves to operate in high and low pressure applications. “This is important for our customers,” explained Simmons. “It increases the number of applications in which their valves and compressors can be used. Having a wide operating range can improve customer satisfaction and lead to repeat sales.”
One of the primary reasons why valves fail are the fissures brought on by repeated impact pressure. “VICTREX PEEK polymer has superior impact resistance,” said Simmons. “We have had applications where VICTREX PEEK polymer has passed up to 20 million impact cycles.”
Metal poppets have always posed a number of challenges. They can be difficult and costly to machine and the sealing surface can be inconsistent due to difficulties in machining defect-free seat surfaces. “Because VICTREX PEEK polymer is compliant and can conform to the mating seat surface, it provides better sealing performance and less leakage than metal poppets in many applications. It also offers excellent wear resistance and improves wear conditions on the mating seat surface. Wear and damage to the mating seat surface is an important issue with metal poppets,” explained Simmons. “Our customers have also experienced a significant decrease in re-work of units on their production line caused by leakage of the metal poppets. Re-work of pumps and valve assemblies is both costly and time consuming on the production line. Converting to a poppet made from VICTREX PEEK polymer has provided tremendous improvements in our customers’ productivity.”
Plastic to metal conversions and metal part replacement applications are areas of expertise at Performance Plastics. “We’ve successfully used VICTREX PEEK polymer in many metal replacement applications over the years,” said Simmons. “For example,” he said, “A poppet made with VICTREX PEEK polymer replaced a two-piece metal assembly, resulting in a significant cost reduction. It also improved initial product quality and reduced customer valve rework from 200 units per week to less than five – and the poppet has never been the cause for the rework. In another application, poppets made with VICTREX PEEK polymer provided more sensitivity than the metal poppets, resulting in more consistent pressure relief actuation performance. The plastic poppets also provided a lower noise level than the metal poppets.”
For more information on thermoplastics, click here.