Nov 13 2008
Silicon technology from Dow Corning is helping usher in a new generation of light emitting diodes (LEDs) that since their introduction in the 1960s have held the energy-saving promise of replacing incandescent, halogen and fluorescent light bulbs.
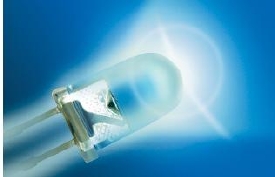
“LEDs have become common in niche applications such as cell phones keypads, large-screen televisions, and traffic signals, but until now they’ve been unable to generate light appropriate for broader use in homes and offices,” said Billy Han, global market manager, Dow Corning Light Management.
The hope is even more palpable in the United States, where consumers and businesses spend approximately $58 billion per year to light their homes, offices, streets, and factories, according to the U.S. Department of Energy. LEDs provide the same light as traditional bulbs but typically burn five times longer and require less than half the energy, according to industry estimates. A recent Department of Energy study (PDF size = 1.4 MB) concluded that current use of LEDs in such applications as traffic signals, holiday lights, indoor white lights, and outdoor lighting is saving consumers nearly $1 billion in electricity costs and if all of these markets switched to LEDs, energy savings would be the equivalent of taking 18 million residential households off the nation’s electrical grid and could save consumers more than $22 billion in electricity costs.
LEDs are semiconductor chips containing a chemical compound that gives off light when an electric current passes through it. The light can be focused into tight beam or a broad pattern through a lens, usually made of plastic or epoxy. The next generation of high brightness LEDs (HBLED) is partly the result of an environmental- and regulatory-inspired adoption of lead-free solder. When LED manufacturers found that existing lenses couldn’t withstand the heat necessary to use the new lead-free solder process, they turned to Dow Corning, a leader in silicon-based technology.
The materials science experts of Dow Corning collaborate with major LED manufactures to develop silicone-based encapsulants and moldable silicone optics that could withstand the heat, are able to use existing assembly techniques, and provide the durability and transparency needed for HBLED applications.
Silicone materials’ optical clarity and thermal stability makes them particularly useful in high-brightness LEDs and in high-reliability applications. Silicones are quickly replacing epoxies and other organic materials to be widely used as encapsulants, lenses, adhesives, sealants and conformal coatings for LED applications.
Those qualities are helping silicone make inroads into a variety of fast-growing HBLED markets, including automotive interior lighting, cell phone flash modules, general lighting and especially emerging liquid-crystal display (LCD) backlights.
Industry experts predict that the global HBLED market will grow from $4 billion in 2006 to $9 billion in 2011.
“Recent advances allowing HBLEDs’ broader adoption include significantly improved performance and reliability from new materials and packaging designs. Silicone materials have proven to be a key enabler to this broader adoption with their ability to increase light output and minimize heat build-up,” said Han. “Silicones are ideally matched to the demands of LED manufacturing because they offer exceptional reliability and optical clarity for brightness and more vivid colors.”