Nov 26 2008
Stork Technimet is proud to announce two new capabilities: Finite Element Analysis (FEA) and Dynamic Mechanical Analysis (DMA). FEA and DMA are just two of the sophisticated techniques Stork experts use to predict your product's performance, lifespan, and other important characteristics. If your product has quality specifications to meet, contact the experts at Stork Technimet for information about a cost-effective and customized testing program that helps you avoid the expense of unintended product failures.
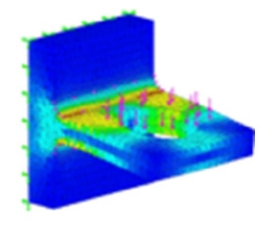
FEA analyzes strength without physical testing
Finite Element Analysis (FEA) is a useful tool for analyzing the strength of a product without physical testing. It can be used to simulate how and where structures bend or twist, and to show the distribution of stresses and displacements, thus giving insight as to how a product will perform in service.
Stork has now acquired Solidworks/COSMOS software, and is ready to perform Finite Element Analysis on your assembly or component.
Stork Technimet is now a one-stop shop for analysis and testing with the following services available:
- Solid model creation from 2-d drawings
- Determination of boundary conditions through field measurements and calculations
- linear, or nonlinear stress analysis
- fatigue analysis
- thermal analysis
- virtual drop tests
- frequency analysis
- buckling analysis
Stork Technimet can also help confirm the FEA results through physical tests and measurements.
DMA: a better way to predict performance
Dynamic Mechanical Analysis (DMA) is a thermal analysis technique that measures the modulus (stiffness) and damping (energy dissipation) of materials as they are deformed under periodic stress. It can be used to assess the effects of temperature on a material, and characterize its physical properties.
For plastics, rubbers, and other polymeric materials, which are viscoelastic and have mechanical properties that are subject to time, frequency and temperature, DMA is an effective method. Stork experts use DMA to measure:
- Modulus
- Creep and Stress Relaxation
- Fatigue Resistance
- Damping
- Glass Transition and Softening Temperature
- Degree of Cure
To fully understand properties and predict their performance over the lifetime of specific applications, engineers sometimes use short-term test information to project long-term high-temperature performance. DMA is a better way to evaluate and predict long term service life, and as such provides a more realistic indication of properties.