Feb 17 2011
SKF, the world's leading knowledge engineering company, has enhanced its innovative range of lubrication systems for the wind energy sector with the introduction of a high performance feeder block for its MonoFlex single line lubrication systems.
Developed to improve the effectiveness of lubrication tasks significantly, this new block controls the flow of oil to multiple bearings of varying sizes and ensures that the optimum volume of lubricant is delivered to each one.
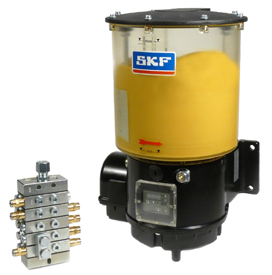
SKF's modular MonoFlex lubrication system is ideal for use with oil, semi-fluid grease and hard grease NLGI grades 000 - 2 and is suitable for a variety of components in wind turbines, including the main, generator, yaw and blade bearings, as well as yaw and blade gearings. Designed for pressures ranging from 16 to 315 bars and venting pressures from 2 to 70 bars, this system features a parallel set up of the single line metering valves to enable quick, simple and reliable installation and functionality. In operation, a pump supplies the lubricant to the distributors via a main feed line and one piston metering valve per lubricant point to ensure that the right amount of lubricant is delivered, regardless of any changes in viscosity or back pressure.
The MonoFlex system forms part of a family of high performance lubrication technologies, including dual line, multi line and circulating oil lubrication products, designed to enhance the performance and reliability of wind turbines. Indeed, regardless of where in the world SKF's proven lubrication systems are located, they have been developed to deliver a high level of operational reliability that protects the assets of those investing in wind power, particularly as increasing numbers of wind turbines move out of their manufacturers' warranty period.
For example, SKF's WindLub centralised system reduces the time needed for lubrication dramatically, as well as extending service intervals by reducing wear and retaining the value of modern high output systems to minimise operating costs. The lubricant reservoirs used in this system have the capacity to contain supplies for up to two years as grease consumption is optimised in an environmentally friendly manner, minimising the need for manual intervention and overcoming the problems of having to carry out lubrication in remote and hard to access areas.