Mar 20 2015
Carbon3D presented their novel approach to polymer-based 3D printing at the TED conference. It is believed that polymer-based 3D printing will pave the way for the industry to move forward from simple prototyping to 3D manufacturing.
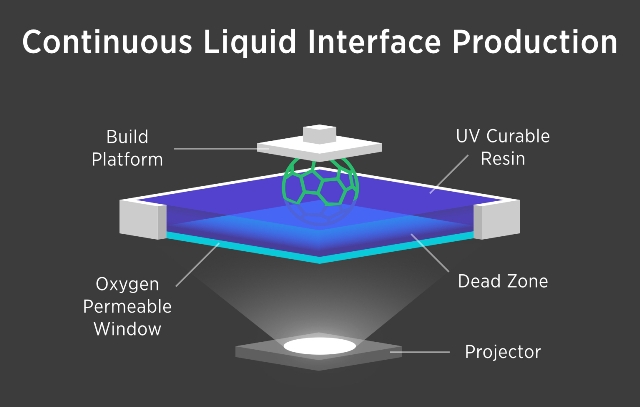
Carbon3D’s innovation is the Continuous Liquid Interface Production (CLIP) technology, which harvests oxygen and light to create objects from a resin pool rather using layer-by-layer printing.
The CLIP technology advances 3D printing in the following ways:
- Compared to traditional 3D printing, its game-changing speed is 25-100 times faster
- The choice of material allows a wide range of polymeric materials
- Commercial quality is ensured as the manufactured objects have consistent mechanical properties
The CLIP technology became the cover story in the journal Science.
“Current 3D printing technology has failed to deliver on its promise to revolutionize manufacturing,” said Dr. Joseph DeSimone, CEO and Co-Founder, Carbon3D. “Our CLIP technology offers the game-changing speed, consistent mechanical properties and choice of materials required for complex commercial quality parts.”
The 3D printing, or additive manufacturing, in use currently is merely 2D printing performed repeatedly. This is the reason why 3D printed components take several days or hours to produce, and the end product is quite mechanically weak because of the shale-like layers. Instead of the typical mechanical approach, a tunable photochemical method was chosen by Carbon3D. Carbon3D’s layerless CLIP technology overcomes these drawbacks in order to enable a rapid transformation from 3D models into physical objects.
Balancing carefully the UV light’s interaction, which helps to activate photo polymerization, and oxygen, which in turn hinders the reaction, thereby allowing CLIP to create objects continuously from a resin pool at very high speeds of about 25-100 times faster than conventional 3D printing.
The CLIP technology utilizes a unique window that is porous to oxygen and transparent to light, very similar to a contact lens. When the oxygen flux is controlled via the window, CLIP develops a “dead zone” in the resin pool, which measures about tens of microns thick (about 2-3 diameters of a red blood cell) wherein it is impossible for photopolymerization to occur. The physical object is continuously created from the region above the dead zone, as a sequence of 3D model cross-sectional images are played similar to a movie into the resin pool from below.
Traditionally manufactured 3D printed parts are unpopular for possessing mechanical properties which fluctuate based on the printing direction of the components due to the layer-by-layer process.
The CLIP technology can be compared to injection-molded parts as this new technology is capable of producing reliable and predictable mechanical properties - solid and smooth on the inner side and outer side respectively.
Carbon3D’s innovation was backed by Sequoia Capital, which took up the company’s Series A round of financing in 2013 along with Piedmont Capital Partners, Wakefield Group, and Northgate Partners. Silver Lake Kraftwerk took up the Series B round of financing in 2014 along with Sequoia Capital and Northgate Capital. The total amount raised to commercialize the technology was $41 million.
“If 3D printing hopes to break out of the prototyping niche it has been trapped in for decades, we need to find a disruptive technology that attacks the problem from a fresh perspective and addresses 3D printing’s fundamental weaknesses,” said Jim Goetz, Carbon3D board member and Sequoia partner. “When we met Joe and saw what his team had invented, it was immediately clear to us that 3D printing would never be the same.”
“We had studied the additive manufacturing ecosystem comprehensively and had concluded that the promise far exceeded the current reality in the marketplace,” said Adam Grosser, Carbon3D board member and Managing Director at Silver Lake Kraftwerk. “When we witnessed the CLIP process, we believed we had found a company that had invented a solution to speed, quality, and material selection. We are proud to work alongside Carbon3D to create a new category of 3D manufacturing.”