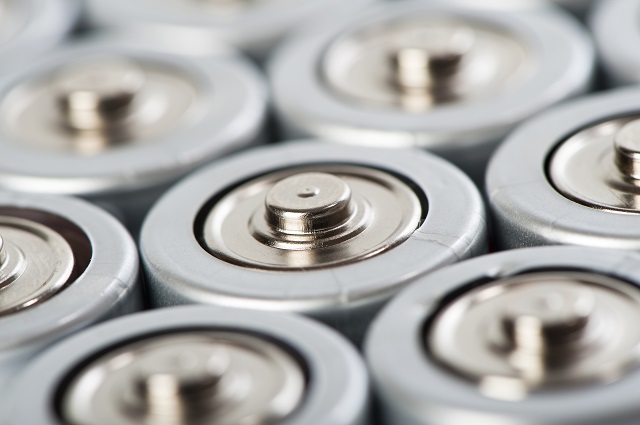
Image Credit: arttonick/Shutterstock.com
Researchers from the Case Western Reserve University and the University of North Texas have created a metal-free bifunctional electrocatalyst that could be used for rechargeable zinc-air batteries. They consider it to be the first electrocatalyst that is equivalent or better in performance to most electrodes made of metals and metal oxides in zinc-air batteries.
Lithium-ion batteries are widely used in mobile phones, laptops, and in electric and hybrid cars. When compared to lithium-ion batteries, zinc-air batteries are considered to be more powerful, cost-effective, durable, lighter and safer.
The metal-free electrocatalyst is based on carbon and is rechargeable, as it can function efficiently in oxygen reduction and oxygen evolution reactions. When compared to most other alternative materials, this catalyst is more ecological. Further, it is easier to produce and is also cost-effective.
With batteries, cost is always an issue and metal-free catalysts can reduce cost while improving performance. These batteries could be used in computers, data stations, for lighting— anyplace batteries are used now.
Dai, professor of macromolecular science and engineering at Case Western Reserve University and senior author of the study
The other collaborators in the study were Jintao Zhang, a Case Western Reserve postdoctor; Zhenhai Xia, professor of materials science and engineering at North Texas University, and Zhenghang Zhao, a PhD student. The experimental work was done by Zhang, while the theoretical simulations were performed by Zhao.
In order to create a charge, zinc-air batteries mix zinc in a liquid alkaline electrolyte with oxygen from the air. These batteries demonstrate three times higher density than lithium-ion batteries, however, they are sluggish. To address this issue, different catalyst materials are being sought by researchers.
In this experiment, the catalyst used is a stable carbon foam or aerogel, having pores of diameter 2nm-50nm. This provides a very large surface area and provides more room for the diffusion of battery electrolyte to take place.
In 2012, scientists at Stanford University had published a foam-making procedure, and this procedure was followed in the current experiment. In a phytic acid solution, the researchers polymerized aniline molecules into long chains. The three-dimensional hydrogel was then freeze-dried into an aerogel. Aniline is an organic compound.
What we did that’s new is carbonized the 3-D structure, changing it into a graphitic carbon material.
Jintao Zhang, a Case Western Reserve postdoctor
The researchers used the pyrolysis process which involved heating of the aerogel to 1,000°C, without the presence of oxygen. This causes a thermochemical reaction which converts the foam into a graphitic network that has many graphene edges. This is very important for the catalysis.
“This is a low-cost, one-step, scalable process,” Dai said. “The electrocatalyst produces comparable or better results than more costly materials.”
The foam is doped with nitrogen by aniline, and this boosts the oxygen reduction reaction. The foam is infused with phosphorus by the phytic acid. “The co-doping of nitrogen and phosphorus enhances both the oxygen reduction and oxygen evolution reactions, as confirmed by the first-principles calculations”, Xia said.
When compared, the performance of carbon foam in a rechargeable and non-rechargeable battery was equivalent to or better than that of platinum/metal oxide-based catalysts that are more expensive.
Further, the carbon foam also demonstrated better long-term stability, and matched or performed better than most other metal-free catalysts and carbon-based catalysts with metals.
The team is making advances in the study, by trying to optimize the process further. They are also conducting studies on other graphitic carbon materials that are co-doped with various other elements for applications in other environmental and energy related technologies.
Earler, Dai's lab had created carbon-based catalysts that performed better than or were equivalent to more expensive metal-based catalysts that are used in dye-sensitized solar cells, and acidic and alkaline fuel cells.
“Maybe it’s time to push for metal-free catalysts in commercial devices,” Dai said.
This study has been published online in the journal, Nature Nanotechnology.
The National Science Foundation and the Air Force Office of Scientific Research have provided support for this study.
References