Gramazio Kohler Research, in collaboration with researchers from the Swiss Federal Institute of Technology (ETH Zurich), has developed an advanced Mesh Mould 3D printing technology, and an autonomous construction robotic system that could meet the growing demand for 3D printed housing solutions for construction sites.
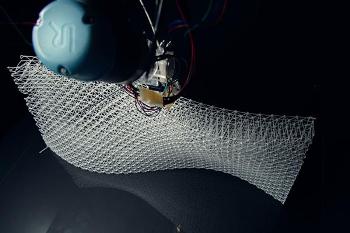
Over the years, there have been some major developments in the field of 3D printed construction. For instance, a large-scale architectural installation in Paris called Iridescence Print showed how 3D printed architectural structures can be easily created without using large amounts of material. Spatial restrictions could also be prevented in such structures. This latest advancement provides vast possibilities in the realm of 3D printed construction.
The Mesh Mould 3D printing technology uses an industrial robot which is integrated with a custom-made extrusion tool. With the help of this tool, continuous mesh structures can be easily 3D printed in space.
Compared to the most common 3D printing process, which involves 2D horizontal layering of materials, the Mesh Mould 3D printing method is much better suited to building complex, large-scales structures. The former is a time-consuming process, while the latter saves significant amount of both time and resources. This is because in the Mesh Mould method, the material is brought directly to the specified space. The new process redefines the traditional layer-based methods, and can be effectively leveraged to tap the scope of 3D printing in practical architecture applications.
In terms of construction context, the Mesh Mould technology can be applied to formwork fabrication. Formwork is a permanent or temporary mould to which concrete is added to create structures like walls and panels. Concrete is a core construction material that is often divided into a shape-defining, lightweight formwork and a heavy structural mass.
With the advanced Mesh Mould 3D printing technology, construction staff can easily extrude the polymers using a robotic arm, and then build customized and intricate formwork right at the construction site. This process can be used to produce a variety of formworks without wasting any material.
“A shift away from this outdated ‘one size fits all’ ideology towards a new fabrication paradigm based on flexible, robotic in-situ fabrication could promote an alternative tectonic that encourages variation and differentiation instead of being bound to geometric simplification, standardization, and repetition,” wrote Fabio Gramazio and Matthias Kohler. “The feasibility of non-standard fabrication…leaves little doubt over its potential at the construction scale.”
In addition to the Mesh Mould 3D printing technology, Kohler and Gramazio reviewed the development of the the first autonomous construction robot called In-Situ Fabricator. Similar to the Mesh Mould 3D printing technology, this robot is also based on an industrial robot arm, and can arrange bricks into pre-programmed structures.
“It’s the first machine that can actually go on construction sites and build non-standard designs, meaning designs which can vary and adapt to the local conditions directly in the building site,” said Kohler.
A 2D laser range finder is integrated in the robot, allowing it to create a 3D model of the construction site. In other words, the robot can adapt to unexpected situations and knows its geographical location; for instance, last-minute changes in design, or sudden drop of construction tools are taken care by the robot.
Mesh-Mould
Moreover, these construction robots provide a number of other advantages, such as minimizing the time required for planning before starting the construction, as well as offering a better and faster construction process. Indeed, these latest innovations indicate that actual human workers would no longer be needed at the construction site, but Kohler claimed that this is not the main focus of the study:
I think this will become a game-changer in construction, I believe so. I think that in the next five to ten years we are going to see mobile robots on the construction site, but they’re not going to replace humans. They’ll actually collaborate with humans, so the best of each kind of skills come together.
Nevertheless, additional studies are required to validate the feasibility of both the Situ Fabricator and the Mesh Mould 3D printing technology. This research clearly shows that mesh structures that are robotically printed can prove useful on the construction site, and may help create unique, unusual designs on-site. Given the recent advancements in this field, real-world implementation will be a reality in the near future.