3D MicroPrint GmbH (Chemnitz, Germany), a company pioneering the use of Additive Manufacturing (AM) to produce complex, micro-scale metal parts, is using the FT4 Powder Rheometer® from Freeman Technology (Tewkesbury, UK) to identify ultra-fine powders that will process efficiently. The company works with powders less than five microns in size to deliver components with cutting edge accuracy and resolution. The FT4 Powder Rheometer differentiates raw materials that exhibit the superior flow characteristics required for successful use of 3D MicroPrint’s Micro Laser Sintering (MLS) technology, for applications in the medical, semiconductor, aerospace, energy and chemical industries.
3D MicroPrint – Additive Manufacturing Powder Samples
‘With MLS we are essentially pushing standard AM towards its performance limits,’ said Joachim Goebner, CEO at 3D MicroPrint. ‘To achieve precise control at the micro scale we spread powders in layers just a few microns thick before selectively fusing areas of the powder bed with a highly focused laser beam. The ultra-fine powders required typically behave quite differently to powders of > 25µm particle size. We therefore rely on the FT4 Powder Rheometer to identify materials which will perform effectively with our machines, with specified process parameters. Before we had the instrument selecting a suitable powder was essentially a matter of trial and error, a far less efficient approach.’
.jpg)
3D MicroPrint – Micro Laser Sintering Machines
MLS is a highly specialised form of Selective Laser Sintering with the capability to cost-effectively produce highly complex and bespoke micro size designs. In addition to supplying machines and powders for MLS, 3D MicroPrint runs a job shop to manufacture components and offers expert support for those looking to adopt the technology. The powder materials used, including titanium, stainless-steel and others, are all specified in terms of chemical purity, particle size distribution and particle shape. The FT4 Powder Rheometer enables the complementary measurement of dynamic flow properties which have been shown to correlate well with performance in AM processes.
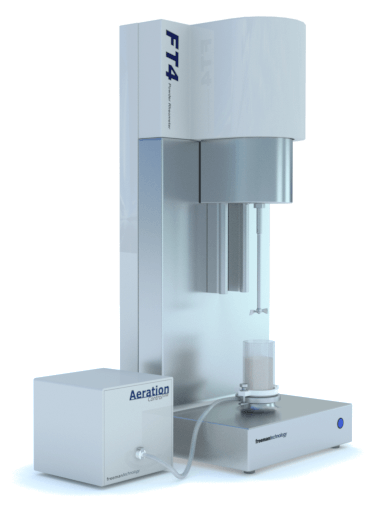
‘All AM processes require powders with optimised properties, and MLS is particularly exacting because of the powders used and the depth of layers required,’ said Goebner. ‘Exemplary powder handling skills underpin our success and the FT4 Powder Rheometer is essential in this regard. By providing sensitive, accurate, highly relevant data the instrument directly supports all our activities, increasing the efficiency with which we apply MLS technology to meet customer requirements’.
For more information about Freeman Technology, please go to www.freemantech.co.uk.
For more information about 3D MicroPrint, please go to www.3dmicroprint.com.