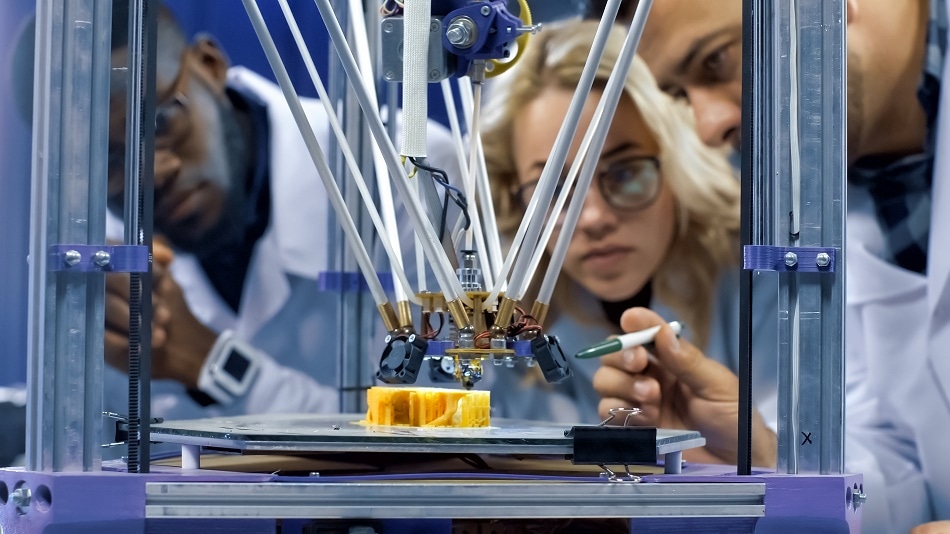
Image Credit: FrameStockFootages/ Shutterstock.com
A team of engineers at Rutgers University-New Brunswick, has developed an automated way to produce up to 384 different polymers simultaneously. The innovation will impact the future of medical manufacturing and is expected to improve healthcare by facilitating the creation of advanced materials.
A Major Limitation of Automated Polymer Synthesis
Polymers can be created by human researchers at the rate of just a few each day. The new system developed by the Rutgers team will see a liquid-handling robot combined with specialized software, allowing it to produce up to 384 different polymers simultaneously. The process is likely to change the way that polymers are produced in the biological sector, given the benefit it brings, of significantly decreased production times.
Other researchers in the chemical and biological sectors have previously begun using controlled living/radical polymerization (CLRP) techniques to produce advanced synthetic polymers, however, while the method has been considered a high throughput (HTP) research tool, with the benefits of increasing productivity, one major limitation has prevented its widespread adoption. This is that the oxygen intolerance of the method meant that large sample volumes and an inert atmosphere were required for the method to work. Methods for producing inert atmospheres are prone to error, making the technique inappropriate for widespread use.
The pharmaceutical industry has already benefitted greatly from the use of robotics in the discovery as well as the development of new drug therapies. However, their limitations have prevented their use in the creation of polymers. The team at Rutgers recognized the missed opportunity here and set about developing a method that overcame the oxygen intolerance of the automated polymer production method.
Creating A Method of Oxygen Tolerant CLRP
Biological research and the healthcare sector has relied on the use of synthetic polymers to develop new diagnostic methods and more effective medical devices. The technology industry has also greatly benefited, using polymers to help create new electronic devices, sensors, and robots.
Given the limitations of the automated method of polymer synthesis described above, the team wanted to resolve this in order to allow more applications to be developed from the rapid production of multiple polymers using a robotic platform.
Assistant Professor of Biomedical Engineering, Adam J. Gormley, and his team noted that recent techniques had been established to conduct controlled living/radical polymerization in an oxygen tolerant manner, such as oxygen tolerant PET-RAFT, Enz-RAFT, and ATRP.
In their paper published this month, in the journal Advanced Intelligent Systems, the Rutgers scientists describe how they automated CLRP reactions using a Hamilton MLSTARlet liquid handling robot. They used Python to create synthesis processes, dispensing sequences, automate reagent handling, and synthesis steps to create homopolymers, block copolymers in 96 well plates, random heteropolymers, as well as post-polymerization modifications. The team successfully demonstrated the harmony between oxygen tolerant CLRP and highly customizable liquid handling robotics for the automation of advanced polymer synthesis for HTP and combinatorial polymer research.
The Impact of Automating Polymer Synthesis
Researchers believe that what they have created is a significant step towards the development of large libraries of complex materials. It will enable scientists to explore the potential of polymers, and develop new chemical and biological applications, particularly in the field of pharmaceuticals. What’s most eagerly anticipated out of this advancement is the creation of regenerative medicine and drugs through the enabling of tissue engineering.
Before this happens though, we are likely to see more work to develop and advance what has been achieved by the Rutgers team, with further automation and integration of open-air chemistries, leading to methods that are more greatly accessible, even to teams who are not experts in the field.
Disclaimer: The views expressed here are those of the author expressed in their private capacity and do not necessarily represent the views of AZoM.com Limited T/A AZoNetwork the owner and operator of this website. This disclaimer forms part of the Terms and conditions of use of this website.