The novel study published in the journal Materials Today: Proceedings was designed to look at how EDM with powder mixed in dielectric may change the spatial variation or qualities of die steel.
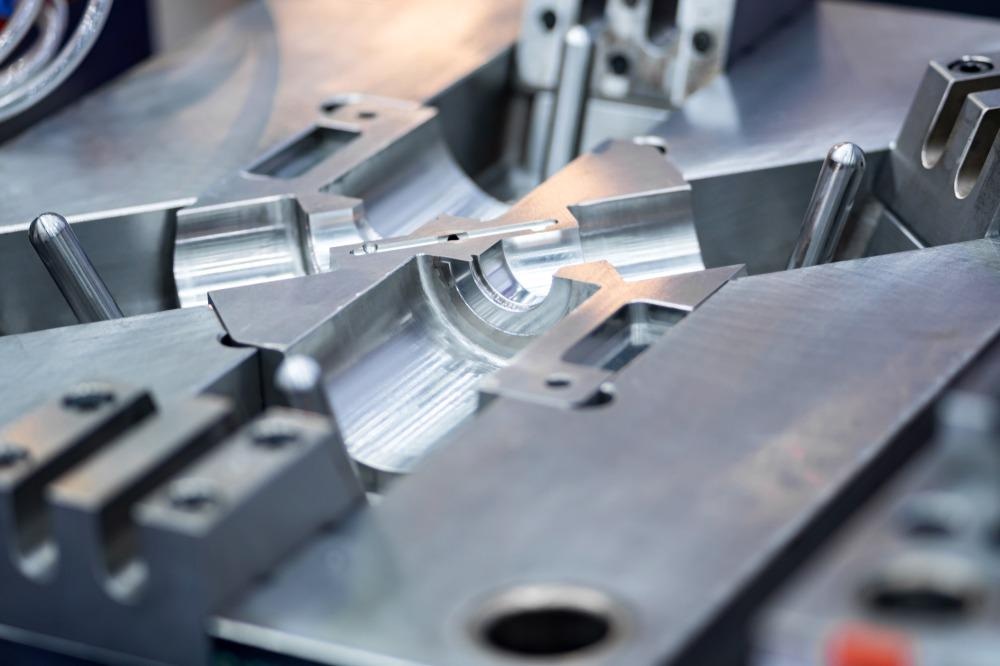
Study: Effect of nanopowder on machining of die steel with different parameters – an experimental approach. Image Credit: oYOo/Shutterstock.com
The investigation focused on two types of electrodes utilized in the machining of die steel. MRR and tool wear rate (TWR) has been greatly enhanced with the use of nanopowder diluted in dielectric when compared to when no nanopowder was employed.
Machining and EDM Process
In the context of the EDM process, the duplicate structure of the electrode was generated on the workpiece, and because of this quality, the EDM process was used to make the complicated forms on dying for manufacturing operations.
The space between the electrode and the workpiece was filled with dielectric throughout EDM cutting. Powder blended dielectric has considerably enhanced the surface morphology of die steel.
Methodology and Experimental Setup
For the workpiece, two different types of die steels were used: one high carbon high chromium and the other EN 31. For the machining operation, a tungsten-copper electrode was employed. The tool's diameter was 18 mm, and the workpiece's dimensions were 100 mm*60 mm*10 mm. Before beginning machining on the workpiece, it was properly ground to assure the leveling of the work piece's base.
The electrode was kept in the negative current trajectory, while the workpiece was kept in the positive current direction. For experiments, kerosene oil was employed as the dielectric. A motor-driven stirrer was employed to ensure optimum dielectric circulation and to prevent nanoparticles from accumulating in the dielectric. The stirrer was turning at a consistent pace.
Research Findings and Results
When nanopowder was added, the material removal rate was significantly higher than when no nanopowder was added. The explanation for this is because the addition of nanopowder to the attrition at the workpiece increases the time it takes to erode the material off the surface.
The present study has indicated a favorable trend for an increase in the MRR. MRR increases with increasing current, and the material removal rate at higher current levels is greater than at lower current values.
Estimating Tool Wear Rate, in addition to measuring MRR, is critical. The TWR increases as the process's input sequence increases, and it also considerably generates craters on the tool's cutting surface. The TWR has been lowered by using nanopowder in the machining dielectric fluid.
Using Dynamic Light Scattering (DLS) to Detect the Onset of Aggregation as a Function of pH of Iron Oxide Nanopowder
When the nanopowder was combined in the dielectric fluid of the EDM process, the tool wear rate in the EN 31 workpiece material was lower than in the HCHCr material workpiece. The tool wear rate at higher current values is lower in the powder mixed process than in the non-powder mixed-method under the same working circumstances.
Surface Properties Findings
The surface is enhanced with the addition of nanopowder as contrasted to the surface without the inclusion of nanopowder. Actual price, pulse on and off period, and nanopowder have all had an impact on the surface finish.
During the milling of the workpiece, the material is transported from the dielectric dispersed powder to the anode material, causing the surface properties to advance. The material was transported to the workpiece, and various compounds were formed on the exterior of the workpiece.
XRD Design
The XRD design reveals indications of copper and cementite components. Copper has transferred from powder floating in the dielectric, as well as from anode material. SEM micrographs of high carbon high chromium manufactured with the tungsten-copper termination without powder mixed in EDM at 200, 500, and 1000.
Conclusive Remarks
The results could be summarized as the increase in current input leading to an increase in MRR. It should be noted that the influence of pulse on and pulse off time on MRR is less pronounced. Also, the material removal rate was greater in the powder mixed process than in the non-powder mixed method. Under the identical working circumstances, the tool wear rate was lowered with the powder mixing technique as opposed to without the powder mixing technique.
According to X-Rd research, as the process progresses at increasing temperatures, less substance from the powder and electrode is transported to the workpiece. The production of cracks on the treated surface was seen with and without the powder mixing method, resulting in some unsatisfactory finish of the workpiece at high temperatures.
In short, the nanopowder substance has found vast application for the machining process of die steel and the results have acknowledged and confirmed their effectiveness.
References
Sokhal, G. S., Dhindsa, G. S., Malhi, G. S., Sindhi, S., & Boparai, R. S. (2021). Effect of nano powder on machining of die steel with different parameters – an experimental approach. Materials Today: Proceedings. https://www.sciencedirect.com/science/article/pii/S2214785321065032
Disclaimer: The views expressed here are those of the author expressed in their private capacity and do not necessarily represent the views of AZoM.com Limited T/A AZoNetwork the owner and operator of this website. This disclaimer forms part of the Terms and conditions of use of this website.