Collaborative robots (cobots) are revolutionizing the manufacturing assembly process. However, there are challenges in the field which must be addressed to provide improvements in the implementation of the technology. A study published in Materials has developed parametric models to assess collaborative robots in manufacturing assembly processes in terms of manufacturing cost and social impact.

Study: Evaluation of Collaborative Robot Sustainable Integration in Manufacturing Assembly by Using Process Time Savings. Image Credit: Phonlamai Photo/Shutterstock.com
Collaborative Robotics and the Manufacturing Assembly Process
Assembling transformed materials into components is a key step in the manufacturing process. Due to growing product complexity and variety, there is a need for the design of components that are constructed out of a variety of materials for diverse functional purposes alongside aesthetic value. Moreover, trends in manufacturing and industry are toward mass customization in highly competitive global markets, with assembly a key value-added activity at the end of the supply chain.
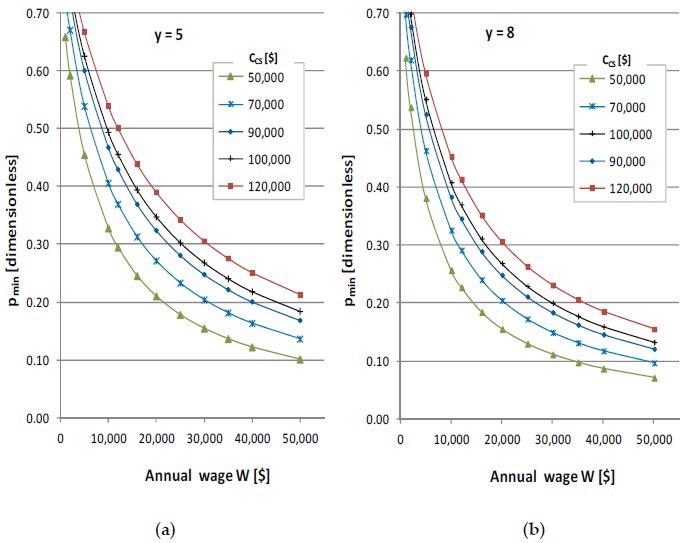
Minimum productivity pmin that supports cobot cost implementation: (a) y = 5; (b) y = 8. Image Credit: Calvo, R & Gil, P., Materials
The process of finishing products is carried out on assembly lines. These lines have varying degrees of automation and, indeed, automation has become a main trend in the industrial manufacturing process since the middle of the 20th century. Key advances in recent years in computer software, information systems, electronics, and robotics have driven automation to enable the mass production of increasingly complex products.
Collaborative robots (cobots) are a key development in the field of robotics that show vast potential for multiple industries, including manufacturing. Technologies such as artificial intelligence, machine learning, neural networks, and sensors (such as vision, contact, torque, and force detecting sensors) have given Cobots improved interaction with their environment. This has facilitated a new paradigm in robotics where operators and robots work together to share tasks.
This collaborative approach improves safety, cost savings, and overall production processes. Human operators can be freed from mundane, repetitive tasks to concentrate on more high-level, creative, and value-added tasks. Cobots act as smart tools. Precision tasks, which usually would be difficult for humans, are performed much more efficiently by collaborative robots. Additionally, cobots can be easily reprogrammed and reconfigured for multiple tasks, making them flexible. They can cope with fluctuating demand and increased customization of products.
Moving Beyond Traditional Industrial Robotics
The introduction of collaborative robotics has helped the industry move beyond traditional industrial robotics. Whereas manufacturing focus has for a long time mainly considered cost, quality, flexibility, and time, operational and strategic flexibility has become more relevant. Taking this into account mitigates market uncertainty and helps to achieve a sustainable balance between manufacturing, environmental, and social considerations.
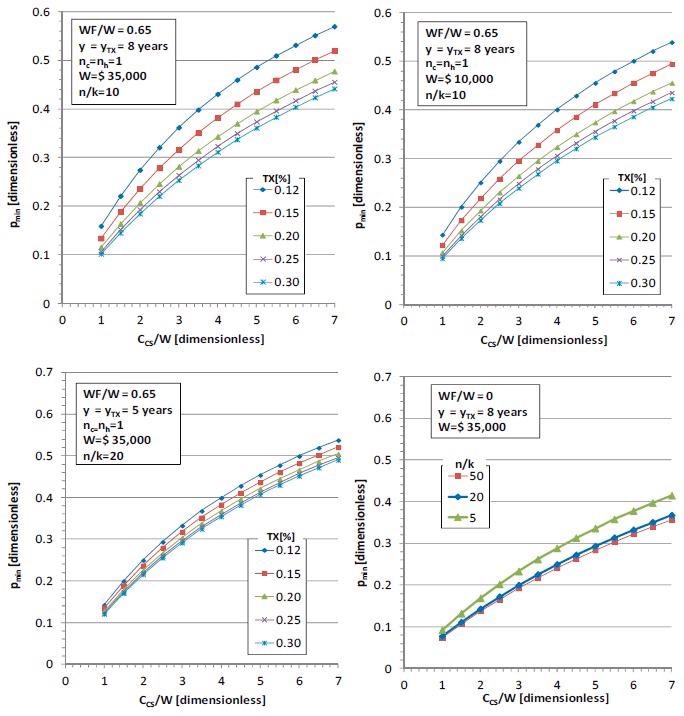
Minimum productivity pmin to support net replacement income WF. Image Credit: Calvo, R & Gil, P., Materials
The shift toward a more collaborative assembly process, where human operators and robots work together, taking advantage of supporting technologies, is a complex, multi-aspect process.
The Study
The study published in Materials has sought to provide an analysis of collaborative robotics implementation in the manufacturing assembly process. Research over the past few years has concentrated on different areas in the field. Studies have identified that one of the main drivers of cobot price is payload range, though there is huge variability. Other studies have found a correlation between payload and reach, but less correlation between payload and price.
In the study, two parametric models have been developed which use manufacturing cost and social impact indicators. Productivity gain and time-saving for processes have been used as decision-making parameters for evaluating collaborative robotics in the manufacturing assembly process. The parameters developed in the study can be used to assess both the cost and social impact of this shift toward a more collaborative manufacturing environment.
Analyzing the results of the experimental sections and case studies, the authors concluded that the economic justification of collaborative robotics implementation relies on achieving moderate time savings in order to become a feasible investment for companies.
Additionally, wages have a non-linear influence on the cost of replacing operators with collaborative robotics (for example, taking into account wage growth and capital) and the cost savings of using collaborative robotics are both short- and long-term. In low labor cost markets, the implementation of collaborative robots may be largely dependent on long-term strategic decision-making criteria.

A Rzeppa homokinetic joint assembly. Image Credit: Calvo, R & Gil, P., Materials
In terms of social impact, whilst the use of collaborative robotics vastly improves worker safety, it also leads to worker displacement and reduced employment availability. Welfare systems in high-income economies can mitigate this impact, but in poorer countries, this is less achievable. The productivity threshold in terms of a social impact compared to economic savings is, therefore, higher in low-wage, low-welfare societies.
The parametric models proposed in the study can be updated and integrated, allowing the development of models for different scenarios that take into account social and economic factors. Proposals for future research in the area include studying the limits of collaboration between operators and robots in parallel with technologies such as sensors and AI which increase the capabilities of cobots. Furthermore, opportunities for research in regard to environmental sustainability are identified by the authors.
Further Reading
Calvo, R & Gil, P (2022) Evaluation of Collaborative Robot Sustainable Integration in Manufacturing Assembly by Using Process Time Savings [online] Materials 15(2) 611 | mdpi.com. Available at: https://www.mdpi.com/1996-1944/15/2/611
Disclaimer: The views expressed here are those of the author expressed in their private capacity and do not necessarily represent the views of AZoM.com Limited T/A AZoNetwork the owner and operator of this website. This disclaimer forms part of the Terms and conditions of use of this website.