A group of researchers recently published a paper in the journal Materials that demonstrated the efficiency of electron beam melting (EBM) method in refining copper technogenic material with a significant impurity content and evaluated the effect of the kinetic parameters on the degree of removal and behavior of impurities.
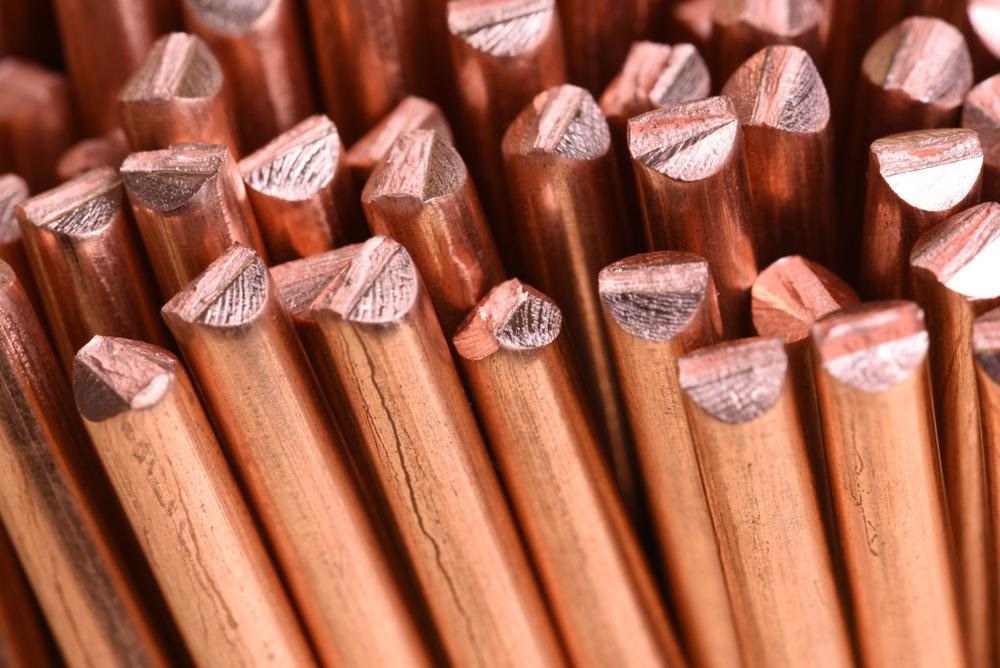
Study: Behaviour of Impurities during Electron Beam Melting of Copper Technogenic Material. Image Credit: Flegere/Shutterstock.com
Background
Copper is one of the most significant metals in the modern era for economic development and improving the standard of living owing to its unique chemical, physical, and mechanical properties. Currently, copper recycling is rapidly becoming one of the primary methods for the production of copper as the method requires substantially less energy than the traditional copper production methods.
(a) Principal scheme of the EBMR process: (1) electron optical system; (2) started metal rod; (3) generated droplets; (4) molten pool in the water-cooled crucible; (5) metal ingot; (b) fabricated copper sample. Image Credit: Vutova, K et al., Materials
In copper recycling, secondary copper is utilized as the main raw or input material. Secondary copper contains a considerable share of impurities that include sulfur (S), dissolved oxygen, and metal impurities such as silver (Ag), gold (Au), tellurium (Te), selenium (Se), bismuth (Bi), zinc (Zn), antimony (Sb), arsenic (As), nickel (Ni), iron (Fe), tin (Sn), and lead (Pb). These impurities are removed using different refining methods in order to obtain purified copper.
Traditionally, copper scrap is refined either by a hydrometallurgical or pyrometallurgical method. However, the growing requirement for copper with better structure and chemical composition with the development of new branches related to electronics and energy has necessitated the identification of new and effective methods for melting copper scrap.
Modern melting methods such as plasma melting, EBM, and laser melting are used to effectively melt such copper scrap. Among these methods, the EBM method is specifically beneficial as it combines the advantages of high-energy special electrometallurgy and vacuum conditions. The high vacuum and the electron beam ensure a greater degree of purification and degassing of the copper scrap.
In this study, researchers evaluated the behavior of impurities during the melting process and the impact of kinetic and thermodynamic technological parameters on the structure of the purified copper and refining efficiency.
The Study
The copper content in the studied material was 99.45%. Impurities present at higher concentrations in the material were Ag, Bi, Pb, Se, O, As, and Ni, while impurities at lower concentrations were Zn, Sn, Te, Sb, and S. Other impurities with concentrations lower than 20 parts per million (ppm) were not considered for analysis.
Initially, the sample was melted at melting powers of 19.5 kW, 13 kW, 7 kW, and 6kW and at temperatures of 1800, 1700, 1500, and 1460 K, respectively, under single processing.
An EBM installation with 60 kW power was equipped with a water-cooled copper cylindrical crucible of a diameter of 50 mm, an extraction system, and a raw material feeding mechanism to perform the investigations related to copper technogenic material melting. The ARL 4460 OES Thermo Scientific spectrometer with a Paschen-Runge vacuum polychromator functioning in argon atmosphere was utilized to determine the chemical composition of the samples after and before the EBM method.
Oxygen analyses of the copper samples were performed using an ELTRA OH-900 oxygen/hydrogen determinator. The microstructure of the obtained copper samples was revealed using a 4% solution of nitric acid in ethyl alcohol. The solution was etched in the samples for a duration of 30 s.
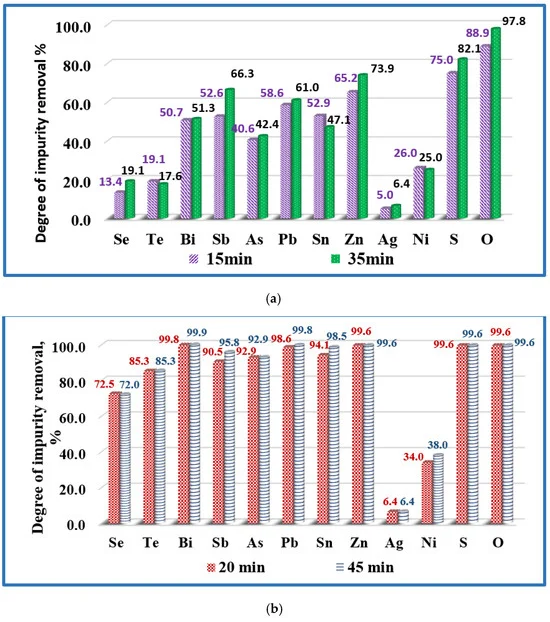
Influence of the melting time on the removal of impurities from copper technogenic material at temperatures: (a) T = 1500 K (samples Cu-02 and Cu-03); and (b) T = 1700 K (samples Cu-05 and Cu-06). Image Credit: Vutova, K et al., Materials
Observations
Observations indicated that at 1700 K, the retention time was 20 min and 45 min, while at 1500 K, the melting time was 15 min and 35 min. At 1800 K and 1460 K, the melting time was 25 min and 20 min, respectively. Metallic impurities such as Sn, Sb, As, Zn, Pb, and Bi were completely transitioned into the gaseous state under EBM conditions and attained an almost 100% removal degree, while Sb attained a slightly lower removal degree at 97%.
Non-metallic impurities such as O and S also attained more than 99% of removal degree. However, the removal degree of Te and Se were 85.3% and 73%, which was considerably lower than other impurities. Te and Se form intermetallic compounds with copper that makes their oxidation more difficult, resulting in a lower removal degree.
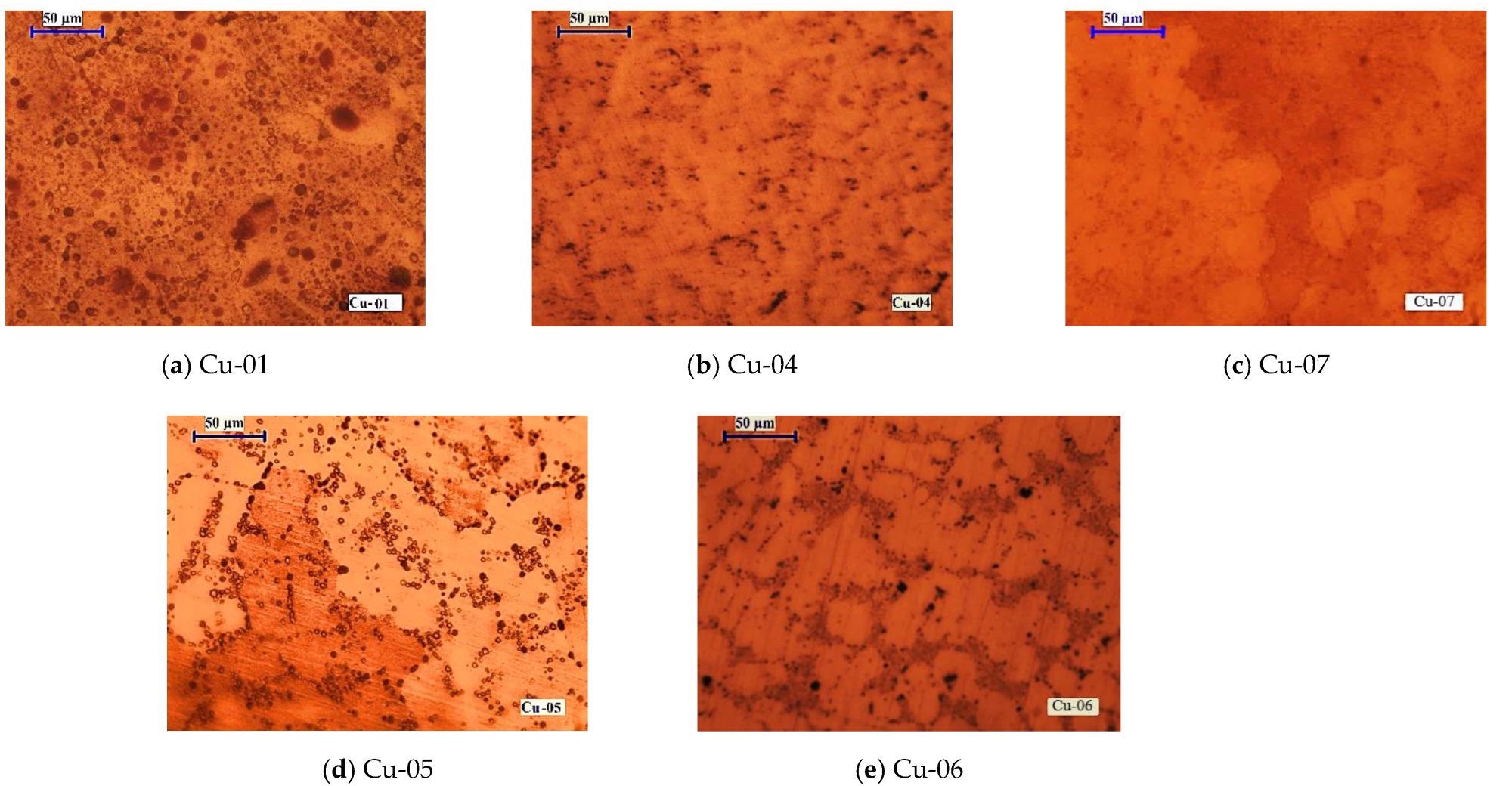
Macrostructures of copper samples manufactured at different EBMR conditions: (a) Pb = 6 kW, τ = 20 min; (b) Pb = 10 kW, τ = 20 min; (c) Pb = 19.5 kW, τ = 20 min; (d) Pb = 13 kW, τ = 20 min; and (e) Pb = 13 kW, τ = 45 min. Image Credit: Vutova, K et al., Materials
Ag cannot be removed by the EBM method as the temperature range of the method in the study and vacuum conditions were not sufficient for oxidizing Ag. The removal degree of Ni was 34-42%, which was significantly lower than other impurities. Good solubility of Ni in copper was primarily responsible for the lower removal degree of Ni. No change in the structure and purity of the refined copper was observed by increasing the melting time above 20 min and temperature above 1700 K.
At temperatures between 1600 K and 1800 K, the refining efficiency was 78-85%, while the purity of the copper obtained after the EBM process was 99.9%. The highest overall refining efficiency of 84.6% and the highest copper purity of 99.92% were observed when the beam power was set at 19.5 kW for 20 min.
This study demonstrated that the EBM method can be applied successfully for refining secondary copper with a high concentration of impurities.
Disclaimer: The views expressed here are those of the author expressed in their private capacity and do not necessarily represent the views of AZoM.com Limited T/A AZoNetwork the owner and operator of this website. This disclaimer forms part of the Terms and conditions of use of this website.
Source:
Vutova, K., Stefanova, V., Vassileva, V. et al. Behaviour of Impurities during Electron Beam Melting of Copper Technogenic Material. Materials 2022, 15, 936. https://www.mdpi.com/1996-1944/15/3/936/htm