A new paper published in the Energies journal seeks to evaluate the most commonly employed methods of repairing these wind turbine blades, investigating their effectiveness, robustness following repair, and their tendency to become damaged again, following repair.
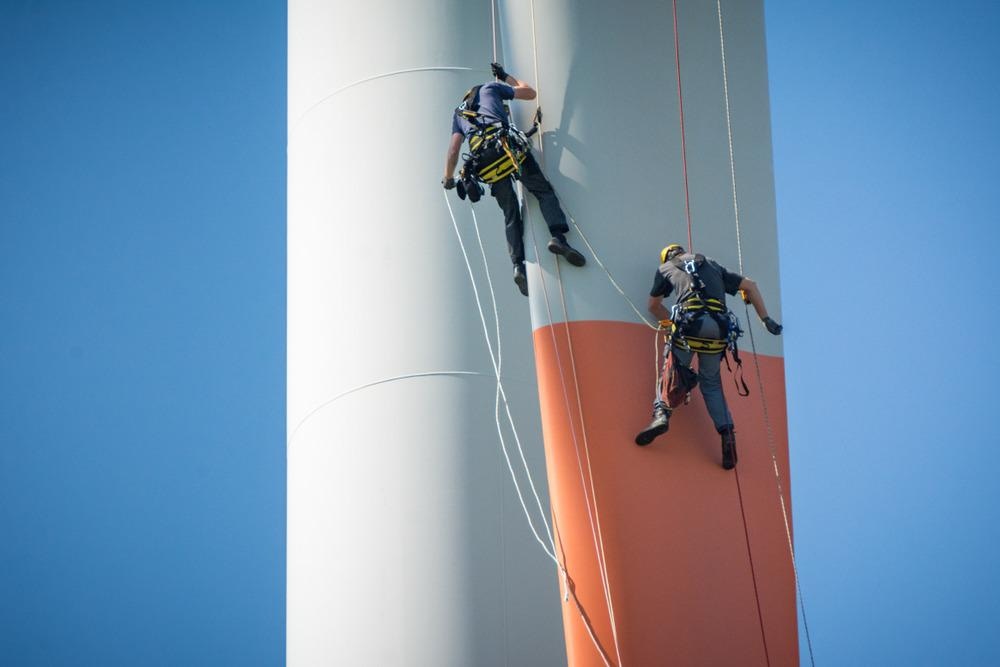
Study: Technologies of Wind Turbine Blade Repair: Practical Comparison. Image Credit: Jacques Tarnero/Shutterstock.com
There are an estimated 700,000 wind turbine blades in operation around the world, with an average of 3800 annual blade failure incidents requiring minor repairs, major repairs, or complete replacement.
The relatively high cost of wind energy is partially due to the cost and complexities of maintaining and repairing the wind turbines themselves, so investigation into and optimization of these repairs could be key to making wind energy more cost-effective and widely available.
Schema of damaged plate (a), photos of plate (b) and of repair procedure (c). Image Credit: Mishnaevsky L Jr et al., Energies
This work is especially relevant for a number of reasons. It is anticipated that the global market for wind power will reach as much as 69700 megawatts come 2027, with the European Union seeking to increase its wind power capacity from 180 gigawatts to 451 gigawatts by 2030 and the U.S. currently working towards generating 30 gigawatts of offshore wind power by 2030.
Reports have shown that onshore wind farm operators spent approximately USD 15 billion on operations and maintenance costs, with as much as 57% of these costs related to unplanned repairs.
Another important factor is the age of many wind turbines, with many of these being installed at the start of the 21st century beginning to deteriorate, requiring more frequent and expensive repairs. These aging turbines, coupled with the sheer number of new turbines coming online over the coming years, will increase the operations and maintenance burden significantly.
The paper’s authors focused on the structural repair of damaged and broken wind turbine blades, using a series of composite plates to simulate these and using a series of tests to evaluate their post-repair properties.
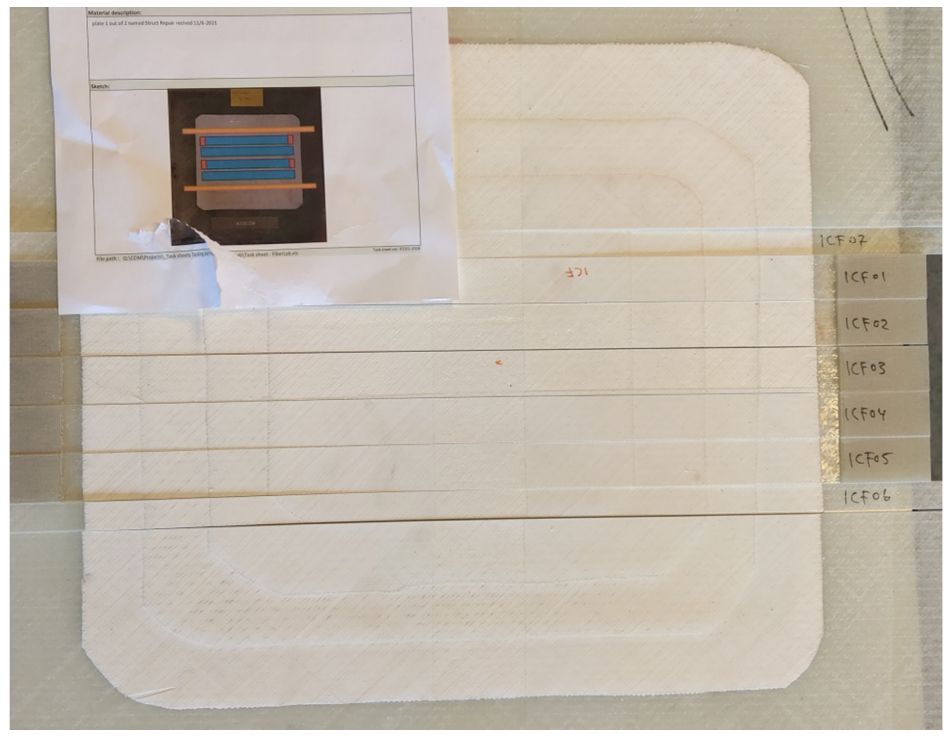
Photo of repaired plate, and geometry of samples to be cut out. Image Credit: Mishnaevsky L Jr et al., Energies
Their goal was to provide wind turbine service companies and management teams with a practical approach to selecting and evaluating repair technologies based on their specific needs, as well as evaluating the performance of the technologies under semi-real conditions and feeding this back to adhesive and equipment developers.
A total of six different technologies were used to repair damaged laminates under comparable conditions, with the repaired samples investigated using microscopic X-ray tomography and tested under tensile static and fatigue tests to evaluate their performance and characterize their failure mechanisms.
Hand layup lamination was evaluated – a conventional approach that involves an engineer putting resin on the laminate and hand-rolling this. Vacuum repair with hand layup saw vacuum applied following hand layup, and another version of this method was used with dry laminate put on the repair and vacuum. Two types of ultraviolet repair were tested, as well as high-temperature thermal curing.
The study’s findings were in-depth and interesting. It was determined that stiffer repair structures with lower maximum stress could be achieved by using repair techniques with applied vacuum, while high-temperature curing resulted in higher maximum stress but softer structures. Average stiffness and high strength were found to be achievable using ultraviolet curing technologies.
One notable disadvantage of the hand layup approach, both with and without vacuum, was the formation of many voids in the repaired part. There was also evidence of residual stresses in a number of samples after bending, suggesting that the repair techniques led to the creation of internal and thermal stresses.
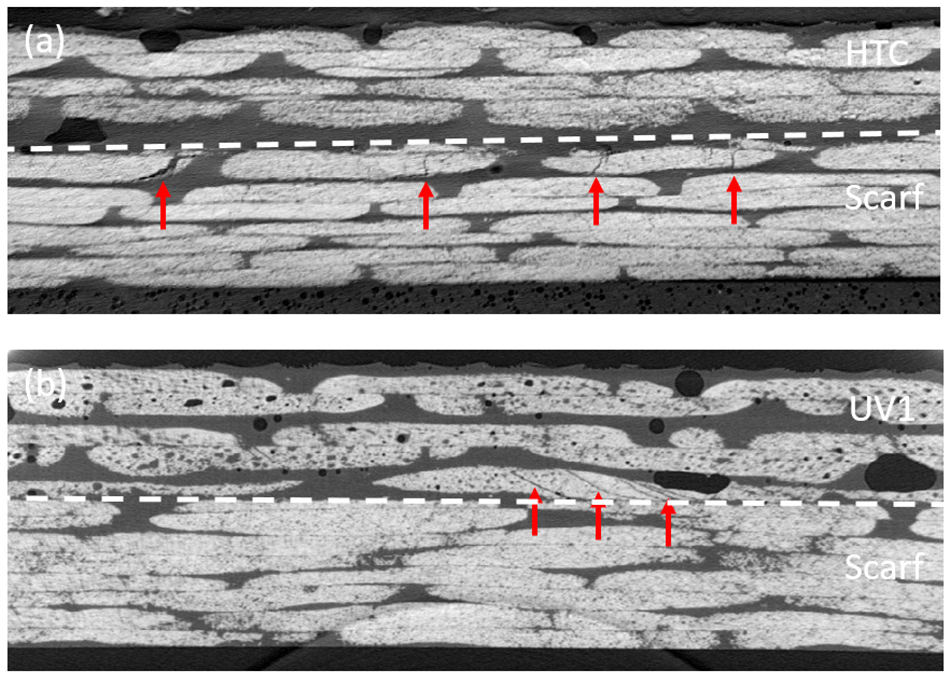
Cracks identified in samples (a) HTC and (b) UV1. The white dotted line indicates the interface between the scarf and the repair, and the red arrows indicate cracks. Image Credit: Mishnaevsky L Jr et al., Energies
The vacuum hand layup technology leads to the formation of a lot of voids in the repaired part, more than all other technologies. The hand layup without vacuum also creates long elongated voids, probably related to badly bonded fibers. In terms of fatigue lifetime, it was noted that vacuum hand layup technology demonstrated the lowest lifetime, UV and high-temperature curing demonstrated average results, while handheld UV curing offered the best performance.
The study offers a promising start to this relatively new area of research, and one which is set to become increasingly important as renewable energy – and most notably wind power – becomes a more central component of global energy production. The optimization of repair technologies and improvements in their effectiveness will be key to minimizing any planned or unplanned downtime of wind turbines and, therefore, maximizing their potential for energy generation.
Reference
Mishnaevsky L Jr., Frost-Jensen Johansen N, Fraisse A, Fæster S, Jensen T, Bendixen B. Technologies of Wind Turbine Blade Repair: Practical Comparison. Energies. 2022; 15(5):1767. https://www.mdpi.com/1996-1073/15/5/1767
Disclaimer: The views expressed here are those of the author expressed in their private capacity and do not necessarily represent the views of AZoM.com Limited T/A AZoNetwork the owner and operator of this website. This disclaimer forms part of the Terms and conditions of use of this website.