The rapid growth in plastic use, waste, and environmental damage in recent decades has facilitated the search for more sustainable alternatives which are repeatedly recyclable and healable. Publishing in ACS Materials Letters, a team of researchers from the People’s Republic of China have presented an in-depth perspective on current progress in this field, as well as investigating challenges and future perspectives.
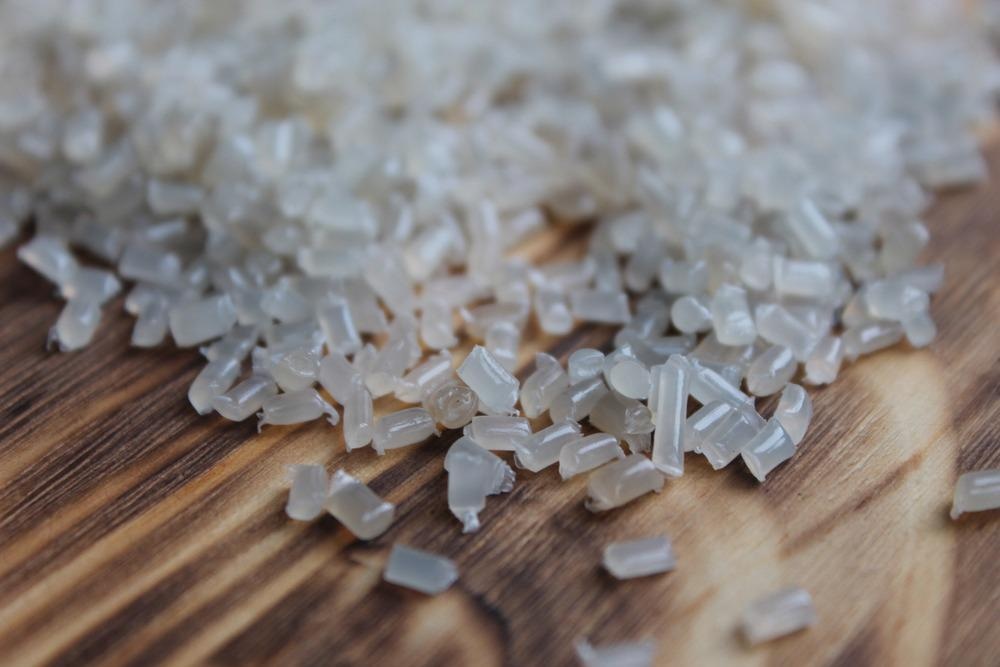
Study: Healable and Recyclable Polymeric Materials with High Mechanical Robustness. Image Credit: Anstasiya/Shutterstock.com
The Challenges with Polymeric Materials
Polymeric materials are a ubiquitous and supremely useful class of materials in modern society. Their superior mechanical properties, lightweight, low cost, and ease of manufacture have made them materials of choice for multiple applications such as consumer products and food packaging.
There are two main classes of plastics which are employed in modern industry for different uses: thermoplastics and thermosets. Thermoplastics possess melt processability due to the lack of covalent cross-linking, whereas thermosets possess covalent cross-linking due to irreversible curing of monomers, prepolymers, and/or oligopolymers.
Thermoplastics are easily recycled due to their processability under high temperatures, but mechanical degradation limits the number of times this is possible. Thermosets possess higher mechanical strength and excellent dimensional, chemical, and thermal stability, but are limited in their recyclability due to strong covalent cross-linking.
Improving Healability and Recyclability
Due to the issues with recyclability and the vast amount of plastic waste being generated annually (as of 2015, 6.3 million tons of plastic waste had been generated globally, with only 9% recycled), there has been significant research focus over the past two decades on developing polymeric materials which are repeatedly heatable and recyclable. Materials have been developed which possess reversible noncovalent and/or dynamic covalent polymer chain cross-linking.
After breaking down during recycling, polymeric chains in these materials can be easily reconstructed and reorganized. They can be repeatedly healed and recycled without the need for melting conditions (which can use more energy) under the conditions necessary for sufficient diffusion of material’s polymer chains. Dynamic covalent cross-linked polymer chains allow the material to act as thermosets under ambient conditions but upon specific stimuli such as heating, they can become endowed with improved healability and recyclability.
Typically, heating is used to cleave the reversible bonds in dynamically cross-linked polymeric materials to reprocess them. The main advantage of these materials is that polymer chain degradation is suppressed during the reprocessing and healing processes. This retains the material’s mechanical properties during repeated heating and reprocessing, making them a more sustainable option compared to currently widely available commercial polymers.
The Research
Publishing in ACS Materials Letters, the Chinese team has provided an in-depth perspective on current research and progress in manufacturing polymeric materials with improved recyclability and healability, and superior mechanical robustness.
Mechanical robustness is an issue with non-covalent and dynamically covalent cross-linked polymers because of bond weakness. One strategy to improve this is the use of dynamic covalent bonds as crosslinkers in materials. However, the healing and recycling of these types of polymers require high temperatures, which can be a huge drawback in terms of energy and cost.
In the research, strategies to improve the mechanical robustness of these materials are discussed, including reinforcing them with high-density covalent bonds and noncovalent aggregates. Additionally, the authors have presented dynamically cross-linked polymers with enhanced mechanical robustness which can be repeatedly healed and recycled under mild conditions and upon heating. Furthermore, the research introduces robust, healable, and recyclable polymers with well-designed functionalities.
More from AZoM: What is Femtosecond Laser-Based 3D Printing?
Over a hundred reviews and studies in the current literature have been explored to provide current research perspectives and progress in the development of this class of polymers. Most studies chosen span the last two decades.
Numerous approaches and materials have been explored in the growing body of literature in the area, with the authors themselves synthesizing polyurethane networks that comprise crystallized PCL and flexible PEG. Polymer chains in the material are dynamically cross-linked by two types of bonds: hindered urea bonds and hydrogen bonds. Ionic liquid skins were impregnated into the polyurethane networks, with the resulting material possessing good mechanical strength, elasticity, and Young’s modulus which is comparable to natural skin.
The impregnated ionic liquid skins possess ultradurable strain sensing capabilities, as well as monitoring strains and pressures with high sensitivity over a broad range. Mechanical damage can be healed by the material, and it retained a superior reliable response to 5% strain over 10,000 cycles, even after being stored in the open air for two hundred days. The material also displayed superior repeatable heatablity and recyclability. The researchers envisage its use in flexible robots and wearable devices.
Amongst current challenges, the authors have identified that industrial-scale protocols for processing this class of materials will be necessary for their future development, as current protocols for conventional thermosets and thermoplastics are not suitable. However, this class of robust polymers that can be repeatably healed and recycled have significant potential for closed-loop recycling and recovery of high-value monomers.
Further Reading
Liu, X et al. (2022) Healable and Recyclable Polymeric Materials with High Mechanical Robustness [online] ACS Materials Lett. 4 pp. 554-571 | pubs.acs.org. Available at: https://pubs.acs.org/doi/10.1021/acsmaterialslett.1c00795
Disclaimer: The views expressed here are those of the author expressed in their private capacity and do not necessarily represent the views of AZoM.com Limited T/A AZoNetwork the owner and operator of this website. This disclaimer forms part of the Terms and conditions of use of this website.