By Surbhi JainReviewed by Susha Cheriyedath, M.Sc.May 10 2022
In an article recently published in the open-access journal Energies, researchers discussed the role of a gas turbine cycle in the improvement of electric vehicle autonomy.
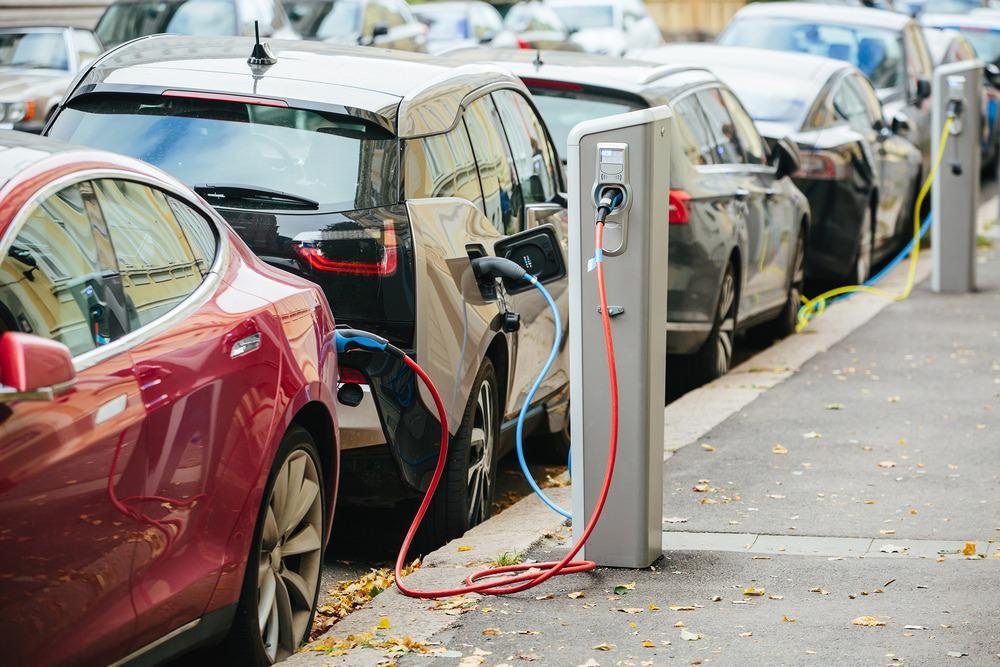
Study: Study of a Gas Turbine Cycle to Boost the Autonomy of Electric Cars. Image Credit: Scharfsinn/Shutterstock.com
Background
Gas turbines (GTs), among other powertrains, have piqued the interest of automakers due to their multiple advantages in several vehicle applications. Recent research has focused on employing GTs as supplementary power units as a solution to electric cars' limited range and high cost. The turbine's mechanical work is turned to electric power by combining the GTs with a generator.
The efficiency of the GT cycle is determined by a number of factors, including its maximum pressure, architecture, and turbine inlet temperature (TIT). As a result, the turbine cooling technology is used to boost TIT. The recuperated GT cycle has been examined as an extender in electric automobiles in some studies. It uses a Brayton cycle with a recuperator to recover heat from the turbine's discharge.
Gas turbine as an auxiliary power system for series hybrid electric vehicles. Image Credit: Najib, J.et al., Energies
About the Study
In this study, the authors proposed a novel design of the gas turbine cycle that could boost the efficiency of EV autonomy. The proposed two-step process started with a sensitivity analysis utilizing Visual Basic for Applications (VBA) and (the National Institute of Standards and Technology (NIST) REFPROP to discover the best operating parameters for increased efficiency.
The researchers presented a new efficient cycle to increase EV autonomy through the development of a thorough methodology. The recommended configuration was based on the proposed cycle since it had the maximum efficiency of the architectures presented to date. The primary focus was to boost the existing cycle's efficiency through an increase in the TIT at the HP cooled turbine and through the elimination of the second chamber.
The team demonstrated a complete sensitivities analysis of the recuperated gas turbine cycle to find the best operating parameters, such as ideal temperature and pressure, the number of compressors, and turbine stages. The GT HP cooling technology was also discussed in detail.
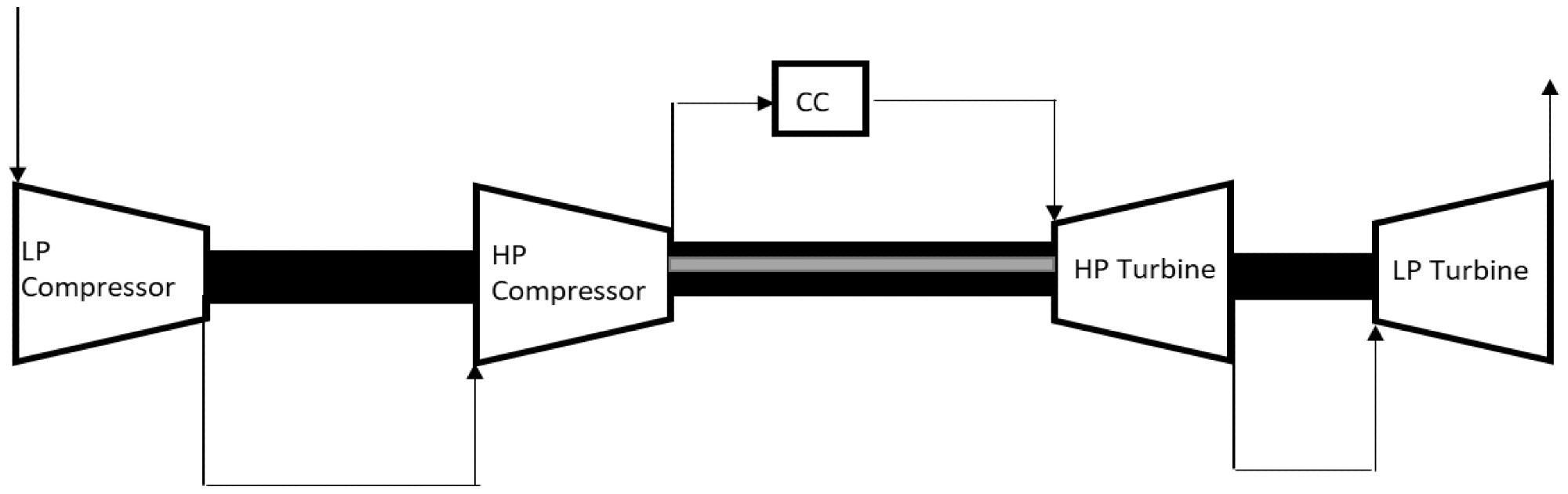
Multi-spool arrangement GT cycle. Image Credit: Najib, J.et al., Energies
Observations
When more modern materials capable of managing temperatures up to 1100 °C were used, efficiency increased to 46.9%. The cycle efficiency was 48.54%, with a 1.66% coolant mass fraction. When compared to the uncooled inter-cooled recuperated reheated (IRReGT) cycle, the efficiency improved by two points. The thermal efficiency of the gas turbine cycle increased at lower compression ratios, then decreased as the maximum pressure exceeded 9 bar. The mass flow rate was reduced from 336 kg/s to 244 kg/s when the maximum pressure increased from 4 bar to 9 bar.
When compared to a single-stage turbine, the work and efficiency of a dual-stage turbine were 65 kJ/kg and 4 points greater, respectively. Additional reheated turbine stages resulted in a less than 30 kJ/kg increase in turbine effort and a 2-point gain in cycle thermal efficiency. When compared to a single-stage, the inclusion of two compressor stages reduced compressor effort by 50 kJ/kg and boosted cycle efficiency by 4 points. When compared to a two-stage compressor, the addition of three compressor stages reduced compressor effort by 14 kJ/kg and enhanced cycle efficiency by two points.
The proposed design had an efficiency of 51.39% and was compact, owing to the elimination of the second combustion chamber.
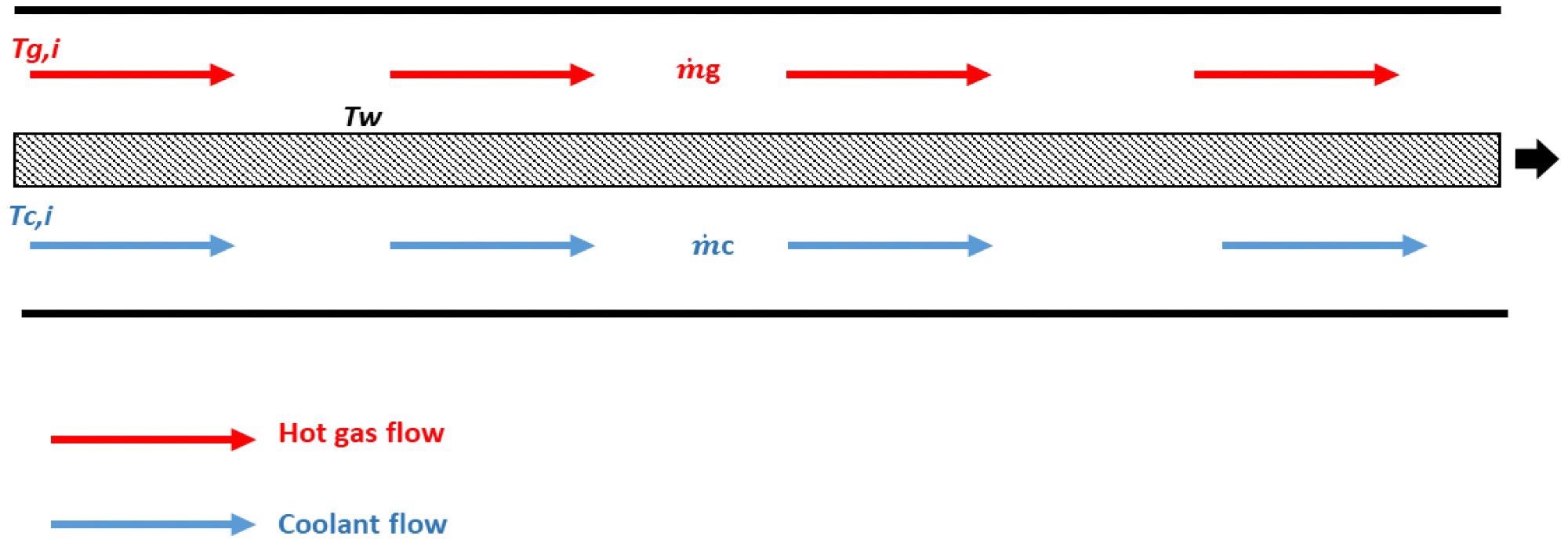
Schematic presentation of the HP cooled turbine as a heat exchanger. Image Credit: Najib, J.et al., Energies
Conclusions
In conclusion, this study identified a novel powertrain as an alternative to the internal combustion engine owing to climate change. Based on sensitivity analysis and a thermodynamic investigation utilizing VBA and Refprop, the ideal cycle configuration in terms of greater efficiency was chosen. Given its high efficiency and lesser complexity, the inter-cooled and recovered gas turbine cycle with an uncooled LP turbine and a cooled HP turbine was the most optimal of the numerous GT solutions evaluated. The HP turbine was cooled by compressed air from the first compressor, while the LP turbine was not. By enhancing the TIT of the corresponding HP turbine in prior arrangements, the second combustion could be eliminated.
The whole system's price and weight could be lowered without reducing the efficiency cycle or coolant mass fraction much. The cycle achieved a better efficiency of 51.39% than the ordinary IRReGT cycle having an efficiency of 46.9% and about similar efficiency as the IRReGT cycle having a cooled HP turbine at a maximum pressure of 9 bar and a TIT of the HP turbine of 1470 ◦C.
The authors mentioned that they plan to expand on a detailed analysis of the total system's cost and weight in future work. They also stated that they would assess the impact of rising temperatures on NOx emissions in the future.
Disclaimer: The views expressed here are those of the author expressed in their private capacity and do not necessarily represent the views of AZoM.com Limited T/A AZoNetwork the owner and operator of this website. This disclaimer forms part of the Terms and conditions of use of this website.
Source:
Najib, J., Nemer, M., Bouallou, C., Study of a Gas Turbine Cycle to Boost the Autonomy of Electric Cars. Energies 15(9) 3348 (2022). https://www.mdpi.com/1996-1073/15/9/3348