By Surbhi JainReviewed by Susha Cheriyedath, M.Sc.May 20 2022
In an article recently published in the journal Annals of 3D Printed Medicine, researchers discussed the development of 3D printed orthotic leg brace having movement assistance.
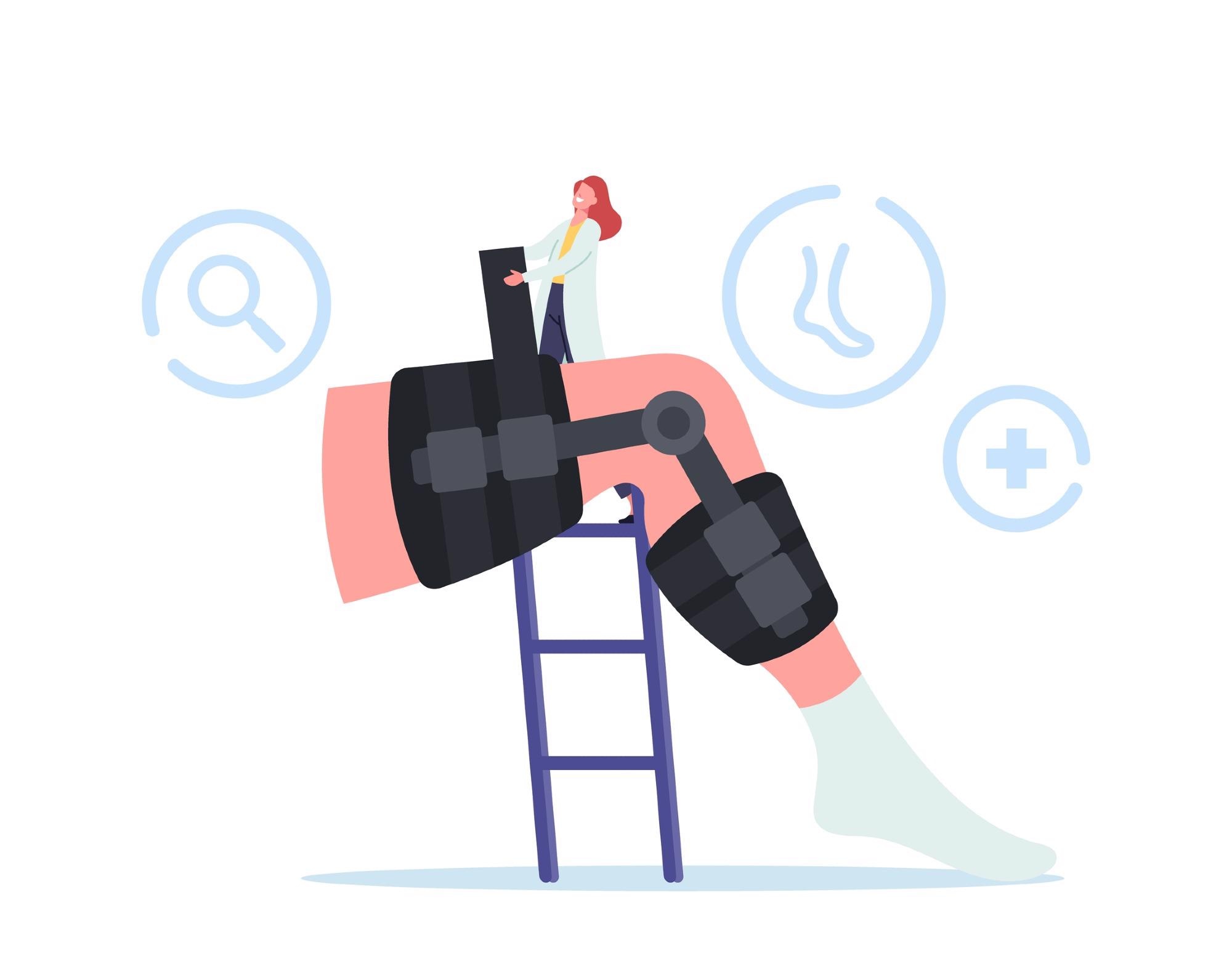
Study: 3D printed orthotic leg brace with movement assist. Annals of 3D Printed Medicine. Image Credit: ivector/Shutterstock.com
Background
People with neuromuscular disorders or spinal cord or brain injuries have limited mobility. Leg orthotic braces printed in 3D are becoming increasingly common. The enhanced characteristics of the 3D printed polymer components have made it possible to go beyond just cosmetic to load-bearing or structural applications. This, combined with the lesser cost of 3D printing, make additively generated orthotics a viable substitute for traditional orthotics.
In the rehabilitation field, assisted leg brace orthotic devices are developed and tested on volunteers for many years. Recent research incorporates modern battery technology, 3D printing, and smaller microprocessors/controllers. These advancements have resulted in a lighter-weight, more compact, and less expensive design that is more user-friendly.
CAD image detailing the brace frame structure. Image Credit: Boolos, M et al., Annals of 3D Printed Medicine
About the Study
In this study, the authors discussed the development of a user-customizable 3D printed orthotic leg brace with enhanced rigidity and assisted mobility by using mechatronic linear actuators. The brace's 3D printed frame lattice structure was customized to the user's leg dimensions.
The goal of the design was to facilitate better alignment of the complicated anatomy of the knee joint and to eliminate or reduce the pain associated with long-term brace use. Dual linear actuators were built within the brace to help the user move their leg through the walking motions.
The team used a 3D printed frame lattice structure in the design, which was fitted with dual linear actuators to help the user move their leg at the knee.
The design was split down into ten sections, which were assembled using stainless steel key rings and clevis pins, cap screws, and heat set threaded brass inserts. The frame was fastened to the socket and ball joint modular components. Poly-lactic acid PLA was used to print the prototype bracing structure. Feedback from a thin film pressure transducer positioned between the front lower area of the brace and the user's leg was used to operate the actuation mechanism.
The researchers created the brace using a CAD software and a 3D printer. A bespoke 3D printed leg brace was provided to assist a user with decreased muscle composition in walking. Dual linear actuators and control circuits were used to build the assist mechanism, which aided the user in leg flexion and extension.
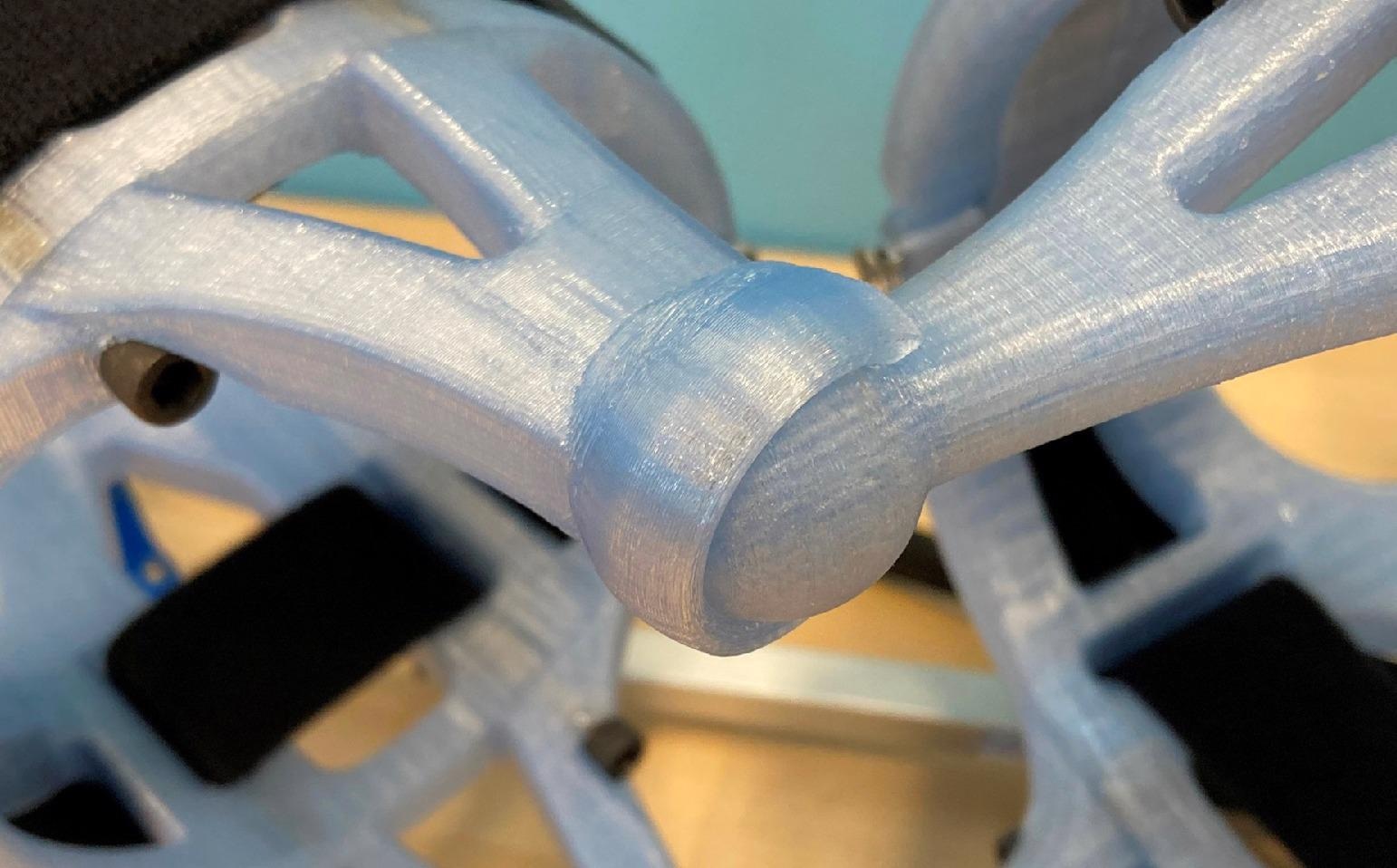
Ball and socket joint on the brace. Image Credit: Boolos, M et al., Annals of 3D Printed Medicine
Observations
Dual mechatronic linear actuators installed on the brace supported the leg in flexion and extension during the gait cycle as part of the movement assist mechanism. The brace was a lightweight, self-contained device that allowed the user to move around more freely. The user-initiated contraction and extension actions with their leg to control the brace. This assisted patients with weak leg muscles in maintaining their mobility for longer, which resulted in improved quality of life and independence.
A unique additively built "cage" for the leg and a ball and socket joint rather than a typical hinge joint made up the novel leg brace exhibited. The actuators could swing freely as the brace works owing to a finger joint and a pin.
The actuators helped with knee bending from 90 to 180 degrees. After analyzing the feedback data from both the sensors, it was discovered that the posterior sensor was unnecessary and could be deleted from the circuit. In the anterior position, the pressure between the brace and the leg provided a signal that indicated lower leg backward or forwards motion.
The ensuing change in anatomical position generated a change in the pressure sensed by the sensor when the user commenced the action of flexing their leg by lifting their heel. The system instructed the actuators to change their position and verify the pressure reading again when the pressure decreased below a configurable threshold. The pressure was checked and incremented until the pressure decreased below the threshold or the position variable reached 180 degrees. The dimensions and shape of this brace could be adjusted to accommodate any leg size.
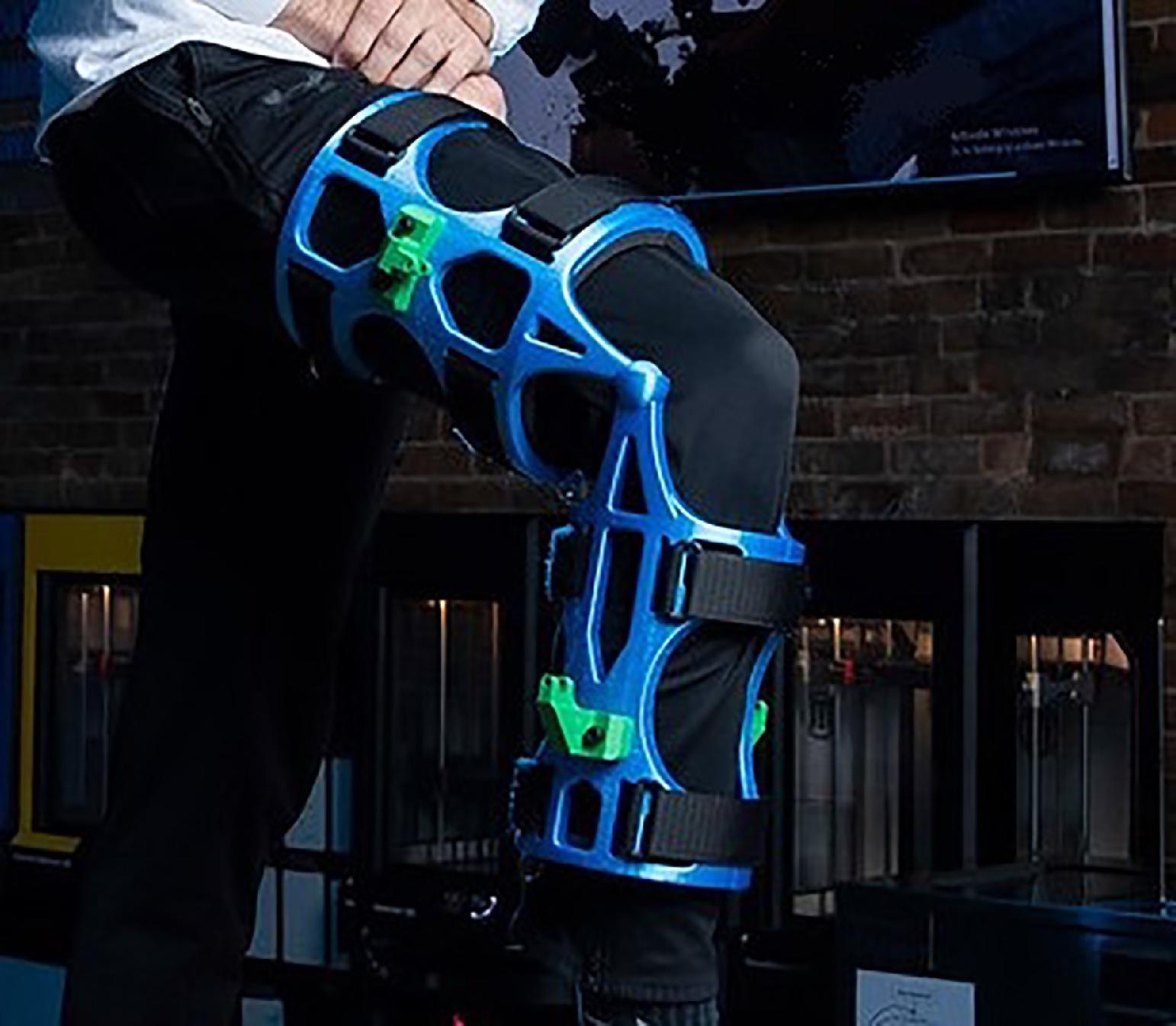
Brace fitted on a leg. Image Credit: Boolos, M et al., Annals of 3D Printed Medicine
Conclusions
In conclusion, this study elucidated the development of a self-contained orthotic leg brace that was operated by the user initiating contraction and extension motions with their leg. This brace will allow the user more mobility and thus a better quality of life.
The team described the testing, design, and 3D printing of a lightweight leg brace that acts as mobility assistance by reducing walking effort. They believe that the developed leg brace will help patients with impaired leg muscles to keep their mobility for longer, improving their quality of life and avoiding some of the consequences that come with a sedentary lifestyle like that of a permanent wheelchair user.
Disclaimer: The views expressed here are those of the author expressed in their private capacity and do not necessarily represent the views of AZoM.com Limited T/A AZoNetwork the owner and operator of this website. This disclaimer forms part of the Terms and conditions of use of this website.
Source:
Boolos, M., Corbin, S., Herrmann, A., et al. 3D printed orthotic leg brace with movement assist. Annals of 3D Printed Medicine 7 100062 (2022). https://www.sciencedirect.com/science/article/pii/S2666964122000182