By Pritam RoyReviewed by Susha Cheriyedath, M.Sc.Sep 5 2022
In a pre-proof article posted in Materials & Designs, researchers quantified the extensional characteristics of battery electrode slurries by employing a miniature extensional rheometer. The novel technique aided the authors in comprehending the slurry structure and optimizing the process conditions to synthesize electrode coatings with the appropriate microstructure.
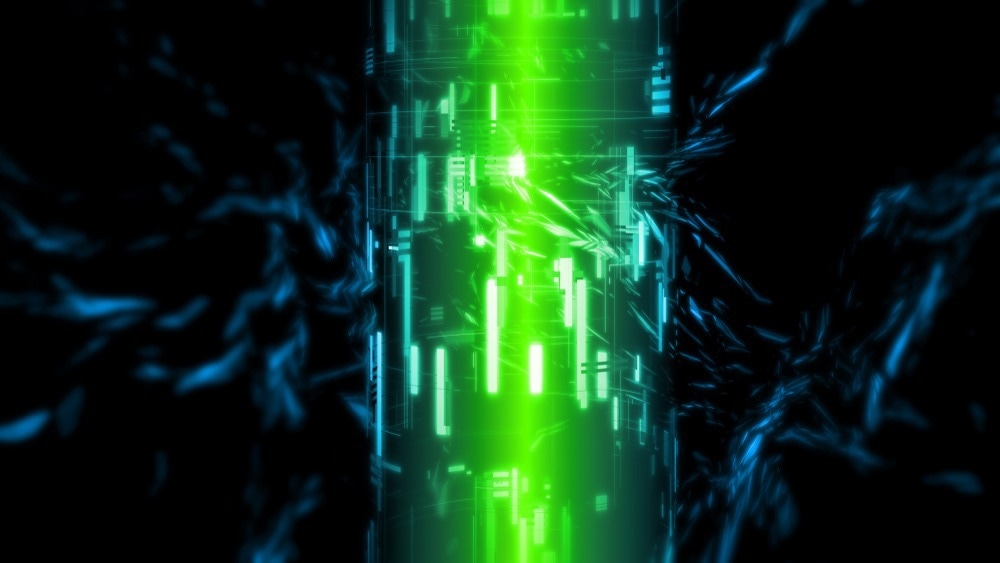
Study: Extensional Rheology of Battery Electrode Slurries with Water-based Binders. Image Credit: kkssr/Shutterstock.com
The proposed approach required samples of less than 1 ml and could rapidly capture the extensional properties, making repetition easy. Different formulations and binder systems demonstrated significantly diverse extensional behaviors. Shear rheology could not predict the additional extensional rheometry observations, which were crucial for comprehending coater flow and the underlying slurry structure.
When applied to battery electrode slurries, the new extensional rheology technique rapidly supplied key rheological parameters essential for understanding the particular rheological properties and controlling coating depositions.
About the Study
As the world shifts from petrol and diesel automobiles toward electric alternatives, scaling up battery production has emerged as a new hurdle. The search for new battery materials and the creation of manufacturing techniques that increase battery recyclability, minimize reliance on essential raw materials and enhance energy and power density are also receiving more attention.
Battery manufacturing is an intricate process involving multiple steps. Active materials, polymeric binders, and conductive additives are combined to create a slurry, which is then applied to a metallic current collector, compressed, and dried to synthesize the electrode. At each stage, various characteristics and properties can be adjusted and measured. The starting materials, electrode coating, and electrode slurry can currently only be characterized using a few metrology methods.
The workings and interactions of the constituents at each phase of the manufacturing process must be clarified using a more significant number of methodologies to create a predictive understanding of the procedure. Characterizing the slurry rheology is a crucial component of the manufacturing process. It is essential because it controls the coater's flow and has a significant impact on the microstructure of the final coating.
Slurry behavior in shear and extensional flows must be understood to describe the complex flow during coating. Electrode slurries are highly viscoelastic, and their rheology is crucial to the final coating microstructure and very sensitive to component ratios. It is likely that extensional rheology also plays a significant role in defining the coating microstructure, given the extensional flows involved in the coating.
Additionally, since polymers are known to have complicated extensional behavior, the polymeric binder is presumably essential to the slurry's extensional properties. Therefore, extension could be crucial in developing new slurries and coating microstructures for the new generation batteries.
Various ways to quantify extensional flow could be employed with electrode slurries. This paper used a hard carbon anode as the test system to investigate the extensional characteristics of electrode slurries by substituting the polymeric binder. It was fitted with models to categorize the extensional behavior and offer parameters for slurry comparison. Quantification of shear rheology demonstrated that shear alone was insufficient to determine extensional behavior. The influence formulation had on these properties was also shown, and paths to develop formulations with particular extensional properties were further discussed.
Observations
The materials for the study included- (i) a Type 1 Kuraray Kuranode Hard Carbon, (ii) Imerys TIMCAL Super C65 as the carbon black, (iii) Ashland BVH8 indicated Carboxy Methyl Cellulose (CMC), (iv) Zeon BM451-B was the Styrene Butadiene Rubber (SBR), and (v) Sigma Aldrich was used to obtaining the sodium alginate. In addition, Fisher (AAJ6060322) provided the iota-carrageenan, while Sigma Aldrich (G4129) was used to obtain the guar gum.
Viscosity evaluations were performed on a Netzsch Kinexus Pro+ rheometer which consisted of a Peltier plate and a rough plate with a diameter of 40 mm and a gap of 1 mm. The samples were equilibrated for five minutes at 25 °C before assessing the shear rate range from 0.01 to 250 s-1.
Surface tension evaluations were performed with a Dyne Sigma 703D tensiometer, employing the Wilhelmy plate approach. The plate was dropped just below the slurry surface, retracted, and then the device zeroed. Finally, the plate was dipped into the slurry and retracted to bring it close to the surface. At this point, the surface tension was recorded after letting it stabilize.
Hard carbon anodes, a promising technique for lithium and sodium ion batteries, were selected as the test system because they could be added to current lithium-ion production lines. Surface tension and shear rheology were characterized using a consistent mixing process. A Seymour rheometer that was 3D printed was then used to characterize the slurries.
Degrees of viscosity fluctuated among the formulations in the shear rheology, but all displayed an identical reaction to shear thinning. The effects of binder volume fraction on the extensional rheometry response were also observed. Alginate had the lowest density at 1.1 g/cm3, whereas guar and carrageenan had higher densities of 1.6 g/cm3 and 1.37 g/cm3, respectively.
The findings revealed that the shear rheology was insufficient to predict the extensional effects, which were crucial for processing and handling. For instance, handling caused the guar-based slurry to form long strands. The sheer appearance of the guar and carrageenan slurries was almost identical, but their extension was distinctly different.
Conclusions
This paper demonstrated that shear measurements could not accurately capture the wide variations in extensional rheology between battery slurry formulations. Hence, the extensional rheometry of four different binder systems was measured using the proposed rapid extensional rheology measurement instrument.
The findings showed that excluding extensional measures affected the comprehension of the slurry structure and flow characteristics. Additionally, the results could inform modeling approaches and validate physical models of electrode slurries. Finally, the data could correctly predict the behavior under extensional flow, flow in the coater, and the final coating microstructure.
The analysis of extensional rheology in electrode production elucidated the microscale origin of the battery slurries' extensional rheology. The research aided the design of novel slurries with optimal extensional characteristics for coating, which allowed accurate designing of the final coating microstructure. Thus, quantifying the extension features of the electrode slurries could help to understand the manufacturing procedure, implement digital twins, and remove expensive optimization steps in industrial lines.
More from AZoM: A Closer Look at Semiconductor Test Equipment
Reference
Reynolds, C.D., Lam, J., Yang, L., E.Kendrick. (2022). Extensional Rheology of Battery Electrode Slurries with Water-based Binders. Materials & Design. https://www.sciencedirect.com/science/article/pii/S0264127522007262
Disclaimer: The views expressed here are those of the author expressed in their private capacity and do not necessarily represent the views of AZoM.com Limited T/A AZoNetwork the owner and operator of this website. This disclaimer forms part of the Terms and conditions of use of this website.